Multi-Spindle Automatics
VST 50
- Workpiece dia., max.: 40 mm | 1.5 in
- Workpiece length, max.: 455 mm | 18 in
VST 50 - minimum chip-to-chip times for the ball pin
The machine scores with extreme performance figures. For example, the chip-to-chip time is less than 2 seconds - a ball pin leaves the VST 50 every seven seconds. This speed is made possible by a work area with two workpiece spindles and two optional tailstocks as well as a total of three robots for loading the work area and transporting the components to and from the outside. While one spindle is machining, the other spindle can be loaded and unloaded.
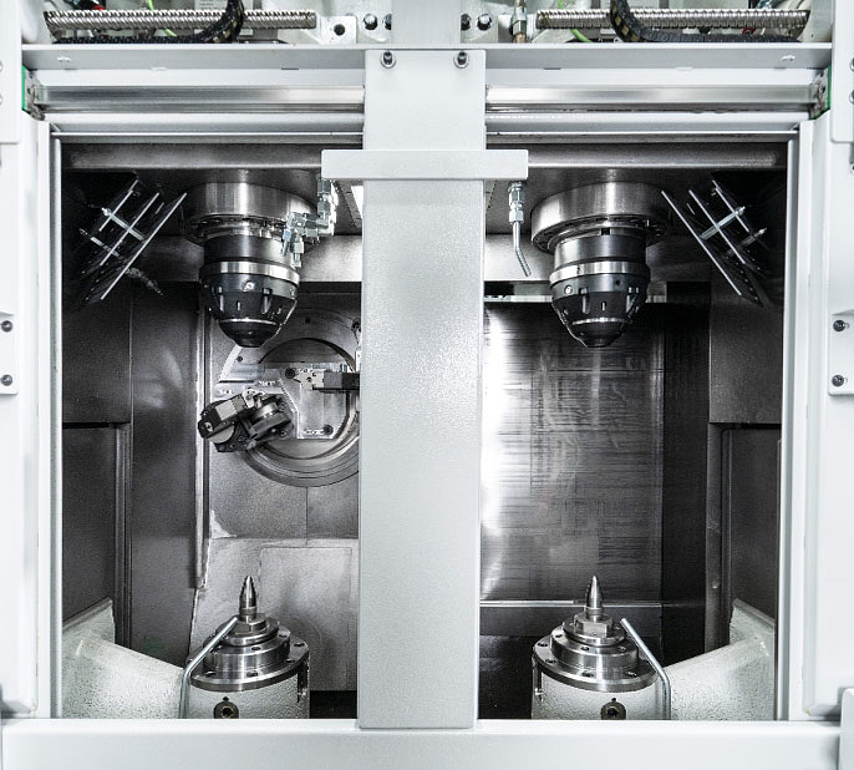
Focus on short and long ball pins
For the demanding turning and smoothing of the ball and neck of the trunnion, the VST 50 has compound slides with a U-axis for infeed to the ball and a rotating B-axis for turning the ball geometry. There are also tools for neck machining. Both short ball pins (ball diameter 16 to 40 mm, component length 50 to 150 mm) and long ball pins (ball diameter 22 to 35 mm, component length 150 to 455 mm) can be machined in this way.

Tool changes made easy
Tool changes on the VST 50 are carried out at high speed with a display on the control system informing the operator when a change is due. To insert the tools, the operator simply presses a button and the fully automatic tool magazine swivels outwards for the change without interrupting the production process. The tool change inside the machine is carried out by one of the robots, and in less than 90 seconds, it removes the worn tool from the interior of the machine and replaces it with a new one, taking it from the magazine.
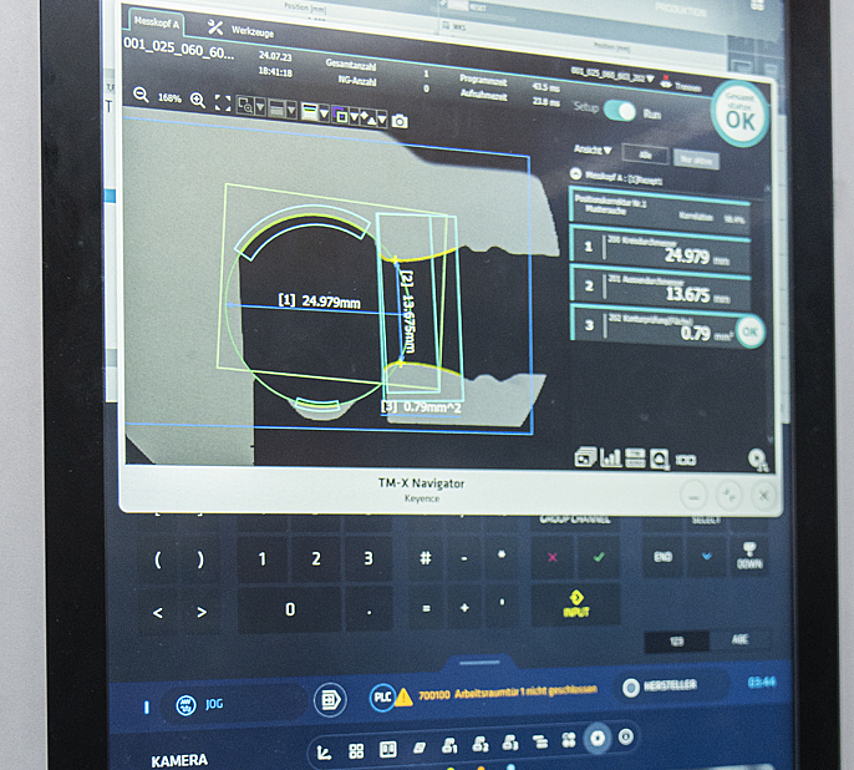
Process reliability "built-in"
For maximum process reliability, the VST 50 is equipped with a light band micrometer, which measures the final ball and neck diameter in fractions of a second and also detects any chips. In addition, there is also a process camera in front of the loading hatches, displaying live images to the operator on the control system, as well as automatic part detection on the conveyor belt.
Advantages VST 50
- Chip-to-chip time less than 2 seconds
- Tool change in 90 seconds by robot
- High-speed automation
- Latest Sinumerik One software generation
- Measuring unit including chip detection outside the work area
- Part recognition on the conveyor belt
- Fully automatic tool magazine (incl. RFID)
- High usability via EDNA apps
Technologies
Complex Manufacturing Systems from a Single Source thanks to a High Range of Technologies
Vertical turning is a machining process for metal components. EMAG was one of the first machine tool manufacturers to use the vertical turning process…