VL Series - Vertical Modular Turning Machines - Low Unit Costs Guaranteed
A design that results in higher production performance: The lathes in the VL series are space-saving vertical turning machines with integrated automation.
Maximum performance at low costs per piece – this performance is based on high-quality components. All VL lathes feature a machine body made of MINERALIT® polymer concrete with world-class damping properties, a pick-up working spindle that moves in the X- and Z-axes with minimum response times and a tool turret that guarantees short swiveling times.
Furthermore, the machines can be fitted with a Y-axis in the turret to allow for the machining of complex geometries. The possible fields of applications for the machines are thus increased massively.
The result: the machine structure ensures a high level of component quality and process reliability while requiring minimum floor space.
Overview of the VL Series of Modular Turning Machines
(5) machines found
EDNA IOT-READY EX-WORKS: Get started with data-optimized production with VL series
Using data analysis, unnecessary downtimes – due to component wear or, in the worst case, due to the failure of a machine – can be reduced or even avoided entirely. Productivity increases of over 10% are the rule here. To make entering the world of data-optimized production as easy as possible for our customers, all the machines of the VL Series now come standard in an IoT-ready state. This means that data analysis on the machines can be started virtually immediately.
More information about IoT Ready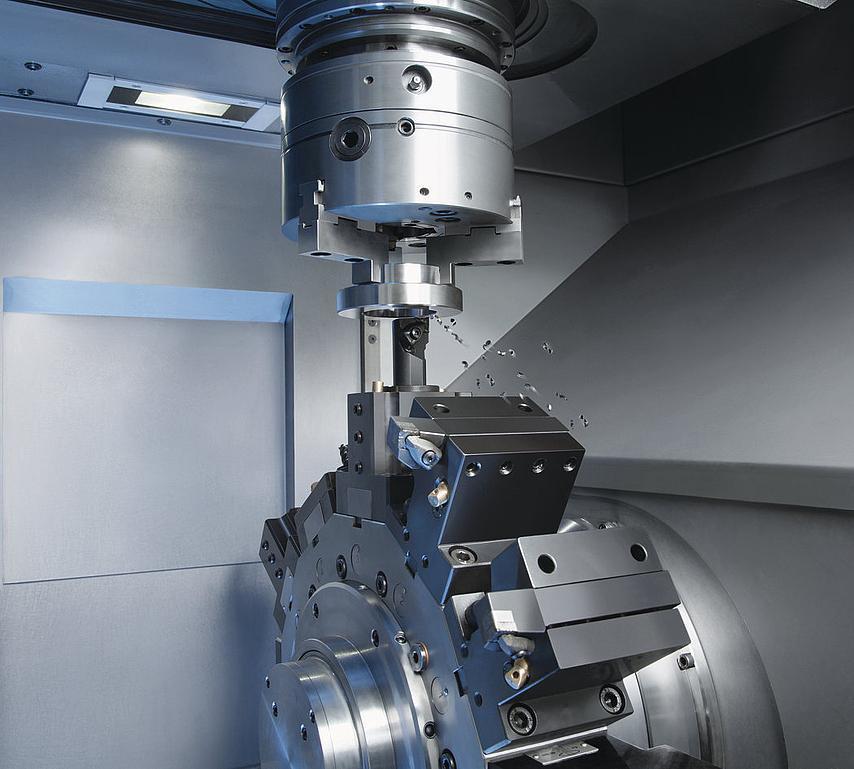
Highlights of the VL Series of Modular Turning Machines
- Consistent vertical model families with modular design ensure a large range of versions
- Ideal for medium and large scale production
- Every machine features the full range of automation and handling technologies.
- Designed for manual loading, but also easy to automate
- Suitable for operation of multiple machines
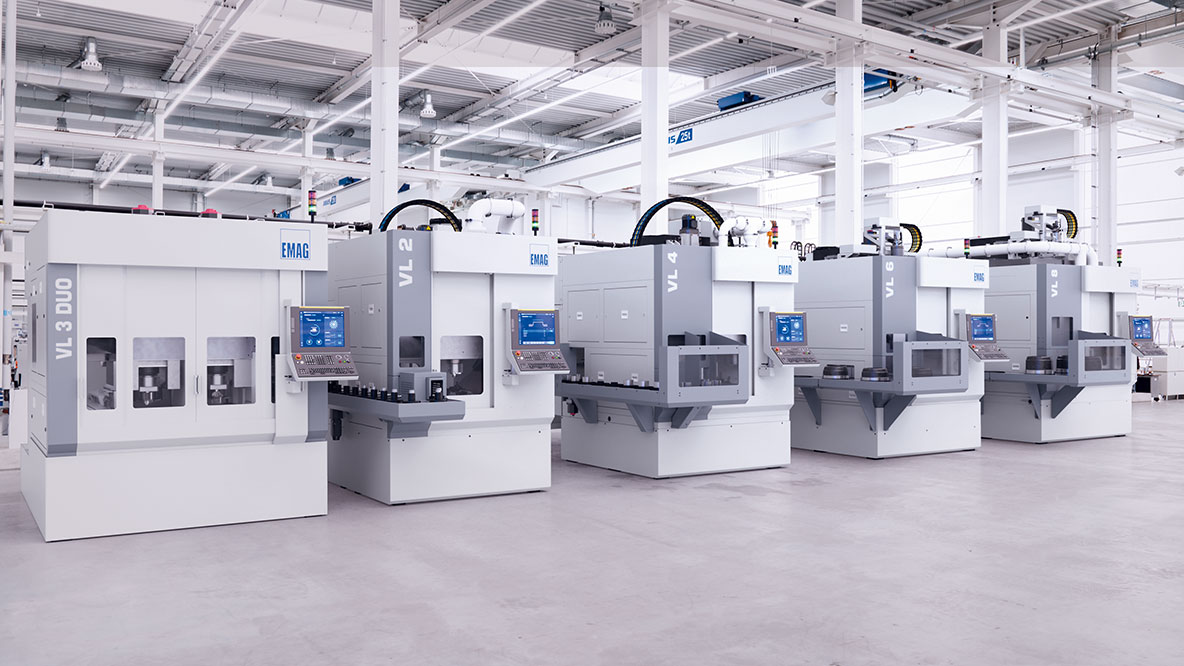
The Benefits of the VL Series of Modular Turning Machines
- Machining of chucked parts = Standard machine concept
- Small footprint (chaku-chaku or close linear arrangement) = Reduced floor space costs, more possibilities for the machine layout
- Possibility of simple interlinking via central feeding and discharge belts and pick-and-place unit/changer = flexible as regards to future developments, lower automation costs, and shorter tooling times
- Integrated automation = No additional costs (interface, etc.)
- Short transport distances = Optimization of idle times
- Common parts strategy, standard spare parts warehousing = Lower maintenance costs
- Ease of operation (extremely accessible machining area) = Quicker machine set-up
- High energy efficiency = Reduction in energy costs