Classic - Chucked Components – MSC
MSC 5 DUO
- Turning diameter, max.: 120 / 240 mm | 4.5 / 9.5 in
- Maximum turning length: 85 / 145 mm | 3.5 / 5.5 in
- X-axis travel: 130 mm | 5 in
High-productivity twin-spindle lathe for automated batch production
Main advantages of the MSC 5 DUO lathe
- High productivity levels enabled by simultaneous machining on both spindles
- Reduced non-productive times due to the integrated 3-axis gantry loading system
- Maximum precision achieved through the split-bed design and thermally stabilized spindles
- Compact design for space-saving integration into existing production lines
- High process reliability ensured by the intelligent coolant system and spindle monitoring
- Easy servicing with easily accessible service components and clear fault diagnostics
The basis for the excellent machining results is the innovative split-bed design of the machine base. This sophisticated design mechanically decouples the two work areas from each other and, thus, prevents the transmission of vibrations during simultaneous machining. This ensures constant dimensional accuracy on both spindles, even during demanding machining processes.
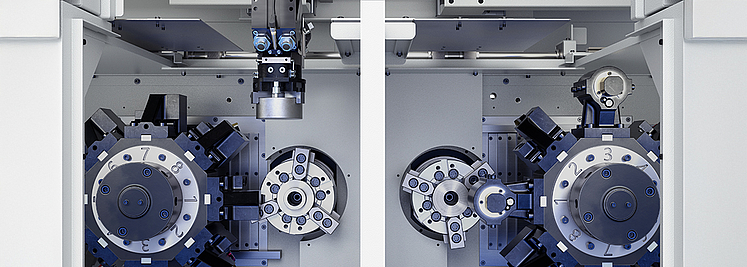
Main Features of the Machine:

Powerful spindles for a wide range of applications
The main spindles of the MSC 5 DUO have been designed for a wide range of applications:
- Maximum speed of 4,500 rpm for dynamic machining processes
- Spindle power of 5.5 kW in continuous operation or 7.5 kW for up to 30 minutes (optional: 7.5 kW / 11 kW)
- A2-5 Spindle nose for holding various chucks up to 210 mm (8 inch) diameter
- Constant torque in the speed range of 1,125-4,500 rpm for consistent cutting performance
An intelligent cooling concept with active temperature monitoring ensures constant machining conditions even in continuous operation.
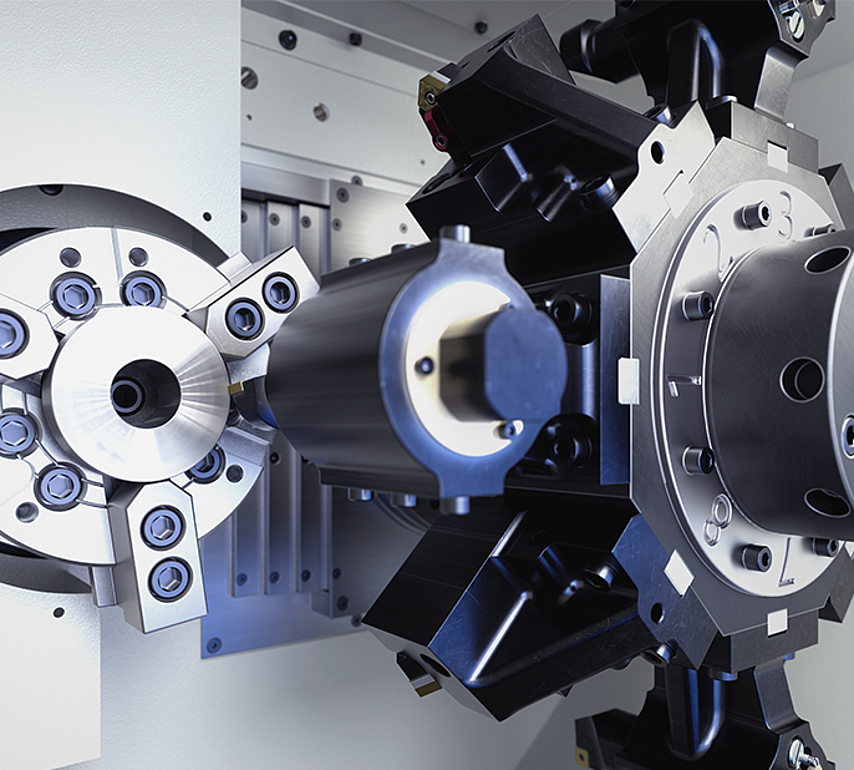
Highly dynamic turret with servo drive
Two servo-controlled turrets form the heart of the MSC 5 DUO:
- 8 standard tool positions (optionally expandable to 12)
- BMT tool interface for high rigidity
- Holds drilling tools up to 40 mm in diameter for internal machining
- Tools with shank 25 x 25 mm for external machining
- Highly dynamic indexing for short tool change times
- Hydraulic clamping for precision positioning
Sophisticated coolant concept for optimum machining results
The cooling lubricant management system was specifically designed to meet the requirements of batch production:
1. Multiple, specifically aligned coolant nozzles for effective cooling in the cutting area
2. Optimized flushing effect for reliable chip removal even with difficult materials
3. Targeted coolant supply for long tool life and high surface quality
Efficient gantry loading system for minimum non-productive time
Integrated 3-axis gantry loading system
The 3-axis gantry loading system, which is fully integrated into the machine control system, automatically loads and unloads the workpieces:
- Fast loading/unloading times
- Precision parts transfer thanks to servomotor-driven axes
- Integrated part turner for complete machining from two sides
- Flexibly configurable workpiece pallets for different workpiece geometries
- Automatic workpiece feed and removal for low-manpower production
Compact stacking storage system
The stacking system (stacker) for raw and finished parts integrated into the machine saves valuable space and enables automation without additional footprint. The flexible pallet system can be adapted to different workpiece diameters.
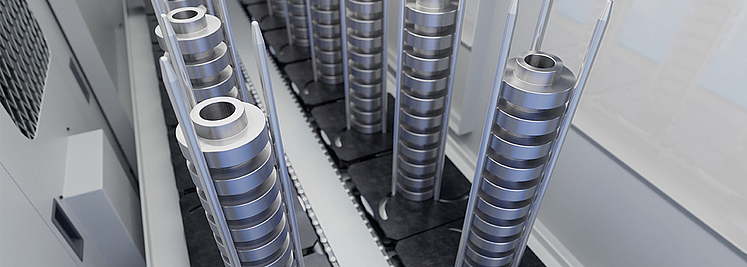
Simple servicing for minimal downtime
When designing the MSC 5 DUO lathe, special emphasis was placed on easy servicing:
- Easily accessible service components for quick maintenance
- Ergonomic tool change from the front
- Clear fault diagnosis of the control unit for fast troubleshooting
- Direct access to the workpiece gripper system
- Large work area door for changing tools and retooling components
These well-thought-out details reduce downtimes for maintenance work to a minimum and contribute to the high availability of the machine.
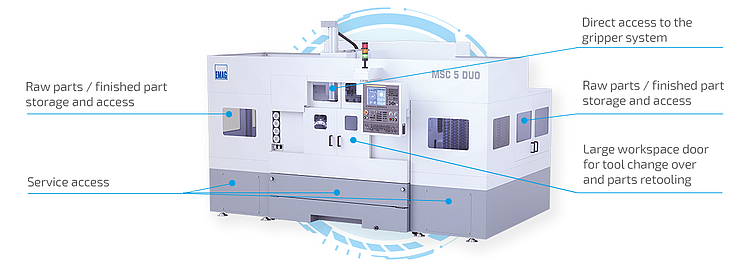
Optimal areas of application for the MSC 5 DUOThe MSC 5 DUO is particularly suitable for:
|
MSC 5 DUO - Component of the EMAG Classic series
The MSC 5 DUO is part of the EMAG Classic series, which is characterized by clarity, efficiency and economy and is the ideal entry-level solution into the world of EMAG.
Features of the EMAG Classic series:
- Optimized basic machines equipped with proven EMAG technologies
- Worldwide service with full access to the global service network
- Focus on low investment budgets with maximum efficiency
- Reduced selection of options with a focus on high-productivity soft turning
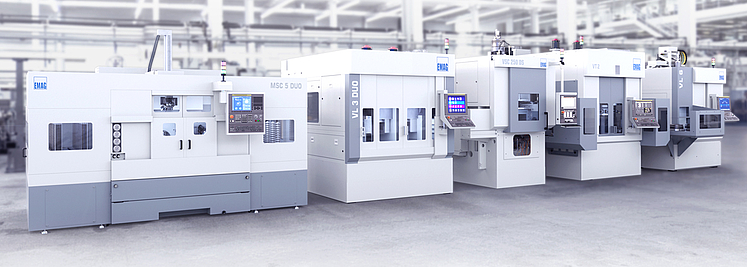
Advantages MSC 5 DUO
- Low non-productive times thanks to automated loading and unloading
- Simultaneous machining on both spindles
- Minimal set-up times thanks to sophisticated tool concept
- High quality for various turned parts
- Energy-efficient drives for low operating costs
- Low maintenance requirements thanks to service-friendly design
- Turn-key solutions for your production