Efficient components and energy management in EMAG machines: reducing consumption for a greener future
In the context of constantly rising energy prices and growing environmental regulations, the topic of energy efficiency is becoming increasingly important in industry. EMAG recognized this trend early on and relies on energy-efficient components and intelligent energy management in its machines.
Optimization of energy consumption in EMAG machines
We pay particular attention to optimizing the energy consumption of our machines. We therefore analyze energy consumption and use energy flow diagrams to analyze where and how electrical power is called up. In this way, we were able to determine that a large part of the energy consumption is caused by ancillary units such as cooling and hydraulics, and that only 10% of the total energy flows into the direct cutting process, while 90% can be considered "unproductive". Nevertheless, this "unproductive" 90 % is necessary for the operation of the machine. EMAG sees considerable potential for improvement and optimization here, without compromising the performance of the machine. An energy flow measurement is therefore the first step in the revision of existing machines; on this basis, the potential for increasing efficiency is evaluated.
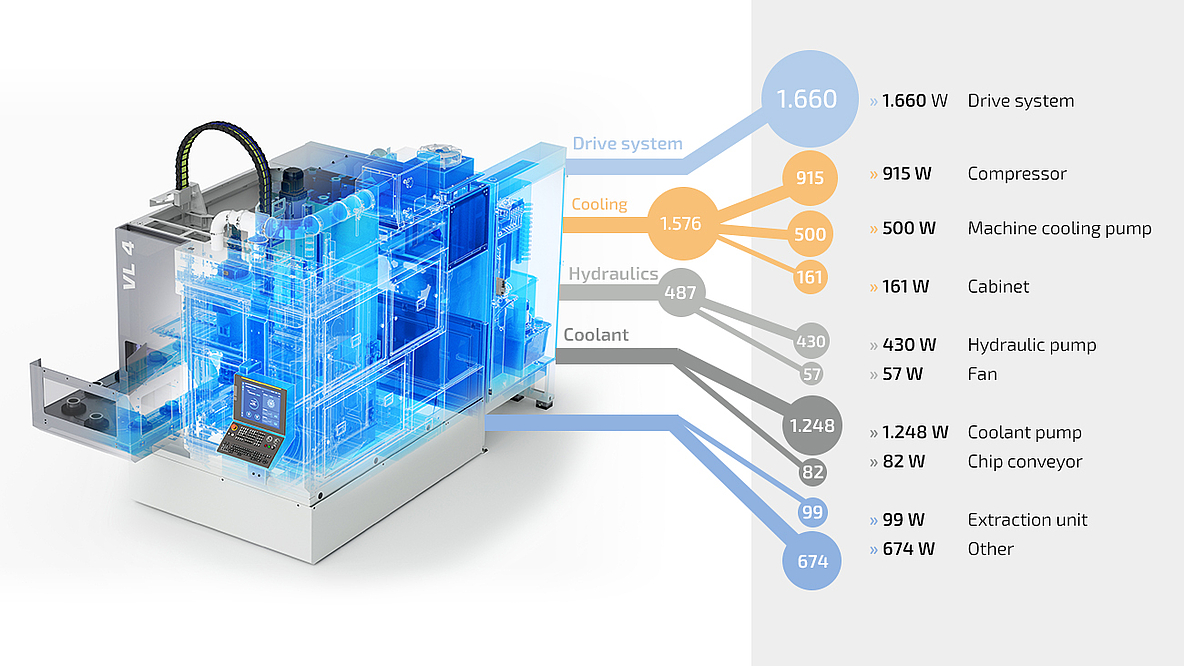
Innovations and continuous development
EMAG machines are continuously developed with regard to their energy consumption. EMAG follows a fixed release cycle in which innovations are incorporated into the standard. This is evident, for example, in the areas of hydraulics and cooling units, where the latest models are always to be used wherever possible in order to ensure even better energy efficiency. In addition, lightweight construction is playing an increasingly important role by reducing the mass of moving parts without compromising on rigidity or dynamic behavior.

Energy efficiency retrofit
Existing machines also benefit from this. For example, EMAG carried out an energy efficiency retrofit on a lathe from 2008, which enabled energy savings of over 18,000 Kwh per year. This is equivalent to the energy consumption of more than two single-family homes. The retrofit took only one and a half days and the machine was immediately ready for use again. The payback period for such a project is about two and a half years with government subsidies and about three and a half years without subsidies.
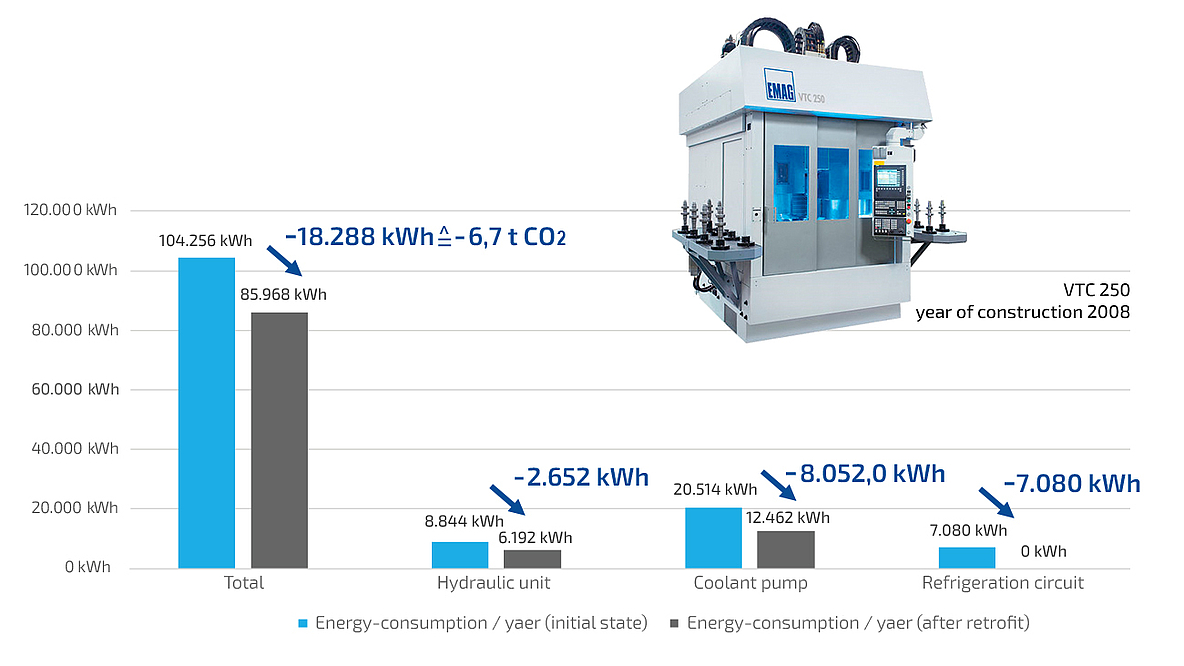
The efficiency factory
The orientation of the EMAG Group is evident in the cooperation with the ETA Factory of the Technical University of Darmstadt. The research project, which is funded by the German Federal Ministry of Economics and Climate Protection, aims not only to improve the efficiency of individual machine components, but also to exploit synergies within the production chain.
For example, the waste heat from a lathe can be used to heat a cleaning machine. A current project in the Efficiency Factory is looking at compensating for the pausing and cold-starting behavior of machines in order to eliminate the need to warm up and keep machines warm and compensate for thermal behavior. This involves collaboration with experts in data and artificial intelligence in production.
The EMAG Group's efforts to improve the energy efficiency of machines and further develop components show how industrial companies can improve their CO2 balance sheet and at the same time increase their profitability. Continuous innovation and cooperation with leading research institutions such as the ETA Factory at Darmstadt Technical University ensure that EMAG can always offer a high level of energy efficiency and sustainable manufacturing processes.
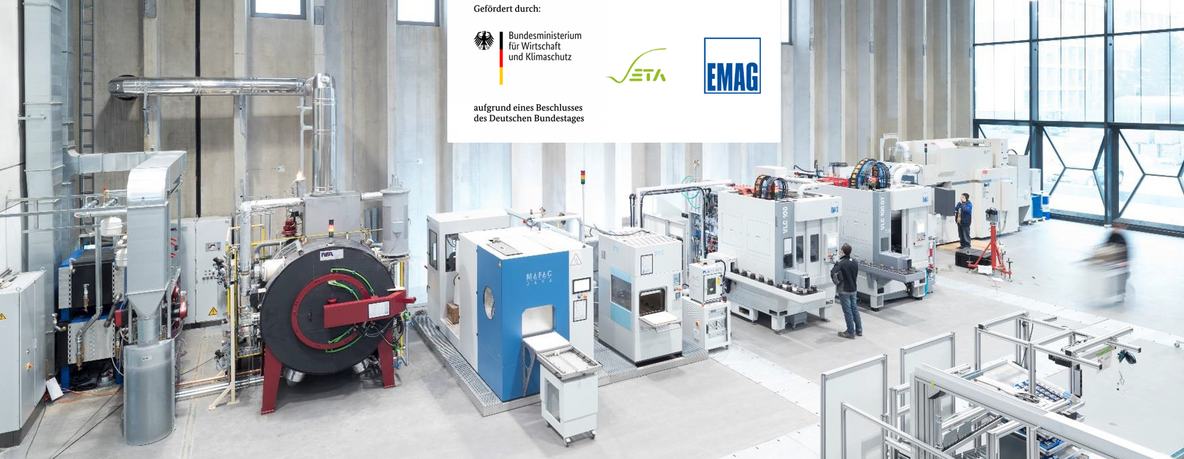