10/14/2019 - Oliver Hagenlocher - 보도자료
EMAG의 생산 시스템: 터보차저 샤프트의 완벽한 마무리 가공
터보차저의 생산은 자동차 제조 분야에서 가장 까다로운 작업에 속합니다. 고강도 소재, 외형에 대한 정밀한 요건, 대량 생산 및 가격 압력은 OEM과 공급 회사가 처리해야 할 과제입니다. 그뿐만이 아닙니다. 자동차 제조 분야에서 점증하고 있는 다운사이징 추세로 인해 배기량은 점점 더 줄어드는 반면 출력은 더욱 더 강해지고 있어 생산 계획자들은 터보차저의 샤프트와 같은 부품에 점점 더 많이 주목합니다. 따라서 생산량은 높이는 반면 ‘단가’는 낮출 수 있는, 고도로 정밀한 프로세스를 보장하는 자동화된 생산 솔루션을 요구하게 됩니다. 현재 직면한 이러한 과제에 대한 어떤 통일된 솔루션을 EMAG이 최근에 개발하였습니다. ‘자체 개발된’ 연결 생산 시스템에서 황삭, 경화 및 연삭 및 ECM 밸런싱까지 터보차저의 샤프트에 대한 완전한 마무리 가공이 이루어집니다. 이 시스템에서는 ‘최종 품질’ 상태의 부품이 50초 이내에 생산됩니다.
자동차 제조 분야에서는 다운사이징 경향이 계속되고 있습니다. 따라서 VDMA는 최근에 발표한 연구 ‘변화하고 있는 구동장치’에서 2030년까지는 승용차에 장착된 실린더의 개수가 현재의 평균 4.3개에서 4개로 감소할 것이고 예측하고 있습니다. 엔진도 향후 더 작아질 것입니다. 이와 동시에 엔진의 배기량도 감소하여 이는 증가한 터보차저의 급기에 의해 보상됩니다. 흡입된 공기는 더욱 더 강하게 농축되어 최고 압력으로 연소실로 압축됩니다. 실제로 이로 인해 출력값이 최대가 됩니다. 최신 엔진에서는 컴프레서 휠이 최고 290,000rpm의 속도로 회전하므로 부품에서 엄청나게 높은 온도가 발생합니다. 이러한 상황에서 터보차저 샤프트의 생산은 자동차 제조 분야에서 특히 까다로운 과제에 속합니다. 이 샤프트는 섭씨 1000도 이상의 고온에서도 견디지만, 그 경도로 인해 가공하기 어려운 인코넬과 같은 고성능 소재로 생산됩니다. 그럼에도 바로 이 터보차저 분야에서는 높은 정밀도와 공정 안전성으로 대량 생산을 하는 것이 중요하며, 이는 EMAG이 항상 수행하는 작업 방법임을 응용 기술 엔지니어인 마르쿠스 노이바우어(Markus Neubauer)는 강조합니다. “저희 회사의 광범위한 노하우는 이 점에서 상당히 유용합니다. 왜냐하면 저희가 보유하고 있는 다양한 기술을 이용하여 전처리에서부터 밸런싱을 포함한 광택 처리에 이르기까지 모든 공정 체인을 처리할 수 있기 때문입니다. 따라서 계획 수립, 프로젝트 관리, 구현 및 서비스가 포함된 완전한 패키지를 자체 개발합니다. 이것이 바로 새로운 터보차저 생산을 구축할 때도 결정적인 역할을 하는 품질입니다. 고객을 위해 계획 수립 및 애프터 세일즈 과정 전체를 과감하게 단순화하였습니다”.
한 생산 라인에서 선삭 가공, 경화, 연삭 가공 및 밸런싱
이것이 왜 커다란 이점인가 하는 것에 대해서는 황삭 및 유도식 열처리, 연삭 그리고 전기화학적 밸런싱에 이르기까지의 까다로운 공정을 한 번 보기만 해도 잘 알 수 있습니다. 여기에는 모두 합하여 다음 다섯 개의 주요 작업이 있습니다.
- 생산을 시작할 때 팔레트 로봇이 원자재를 수직형 선반 VLC 100-4의 컨베이어 벨트 위에 놓으면, 선반의 공작물 그리퍼가 그 부품을 작업실로 이송합니다. 한 번의 클램핑으로 터빈 샤프트의 황삭이 이루어지고, 이때 4-축 가공으로 인해 작업 시간의 단축이 확실히 보장됩니다. 이 선반은 그 구조가 수직형이고 비산하는 칩이 구조물과 결합되므로 칩이 쌓이지 않습니다.
- 두 번째 로봇이 황삭된 부품을 VTC 100-4의 컨베이어 벨트에서 집어내어 EMAG eldec의 MIND-M 1000 내 열처리 장치로 이송하면, 이 장치에서 부품이 상당히 빠르게 정확한 온도로 가열됩니다. 전문가들은 이 공정에서 ‘응력 경감’이 이루어진다고 말합니다. 따라서 부품 내에 있는 응력이 명확히 감소됩니다. 부품의 베어링 시트를 경화해야 할 경우에도 이 장비에서 가능합니다.
- 세 번째 및 네 번째 작업에서는 다양한 연삭 가공이 이루어집니다. 먼저 EMAG의 HG 204에서 샤프트의 수평 연삭 가공이 실행됩니다. 그 다음 수직형 연삭기 VLC 200 GT에서 터빈 휠의 방사형 홈과 임펠러 외곽에 대한 정밀 가공이 실행됩니다. 또는 추가로 장착된 구동형 솔을 사용하여 VLC 200 GT의 작업실에서 임펠러 외곽을 디버링할 수 있습니다.
- 부품이 세척장치와 측정 시스템을 통과하면 마지막 작업인 EMAG ECM의 CS 장비 내에서 전기화학적 금속 가공을 통한 밸런싱이 이루어집니다. 또한 단 한 번의 반복 단계로 칩이 없는 공정이 이루어집니다. 무접촉식 재료 절삭에 의해 공구의 마모가 최소화됩니다. 이는 절삭 가공과 비교할 때 큰 장점입니다.
즉시 장착할 수 있는 최종 품질을 위한 완벽한 공정
승용차용 터보차저 샤프트(터빈 회전자)의 마무리 공정 전체는 50초 미만의 라인 사이클 타임에 이루어집니다. 3교대 작업 시 매년 420,000개에서 450,000개까지의 터빈 회전자를 생산하게 됩니다. 결국 마무리 공정인 밸런싱 후 그 부품은 즉시 장착할 수 있는 ‘최종 품질’을 갖게 됩니다. “마침내 저희는 이 제품 또는 이와 유사한 제품의 경우 항상 완벽한 맞춤형 설비 아키텍처를 보장합니다. 이 외에도 EMAG은 고객과 함께 다양한 공구 애플리케이션, 다기능 공작기계의 컨셉트, 전체적인 제어 및 체인화, 그리고 상위 시스템으로 연결 등 모든 지식을 공유합니다.”고 마르쿠스 노이바우어는 요약합니다. “이러한 자체적인 노하우는 바로 이러한 까다로운 부품의 생산 시에도 우리가 시장에서 확신할 수 있는 성공을 보장합니다.”
이미지
다운로드
담당자
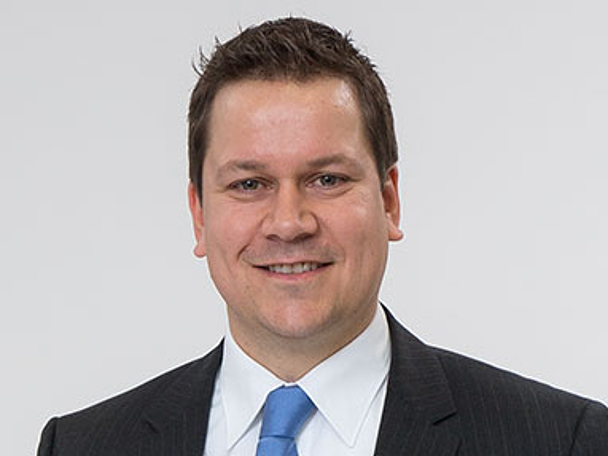