12/14/2021 - Oliver Hagenlocher - 보도자료
EMAG ECM의 전해가공: 드릴 및 밀링 커터 대신 전기를 사용한 가공: 절삭 가공의 대안 ECM
전해가공(ECM)은 디버링에 사용되는 확립된 기술입니다. 하지만 ECM은 그 이상의 기능을 탑재하고 있습니다. EMAG ECM은 기존의 보링은 물론 브로칭 가공, 심지어 밀링 가공까지 대체할 것입니다. 절삭 가공에 비해 이미 수많은 장점들이 입증되었습니다.
이미지
"지금 한창 진행 중인 구조 변화는 제조업에도 일어나고 있습니다."라고 호이바흐(Heubach)에 소재한 EMAG ECM의 영업부장인 프란츠 그로스(Franz Groß) 씨는 확신하며 말합니다. 이미 발전하고 있는 E-모빌리티만으로도 필요한 부품의 전체 수량이 차츰 줄어들고 있습니다. 게다가 향후 부품들의 형태도 변할 것입니다. 이와 동시에 소재, 형상, 복합성 및 정확도에 대한 요건도 증가하고 있습니다. 예를 들어, 자연에서 영감을 얻고 흐름에 최적화된 부품들이 더 많이 개발될 것입니다.
이 과제에 대한 솔루션이 바로 ECM 전해가공입니다. ECM 전해가공은 현재 다수의 영역에서 품질과 경제성의 이점을 가지고 기존의 절삭 가공을 보안하거나 대체할 수 있습니다. "기계적 부하 및 열적 부하에 노출되지 않기 때문에 공구의 마모 현상이 절삭 가공 시보다 현저히 감소하고, 공작물 또한 조심스럽게 다루어집니다."라고 그로스 씨는 설명합니다.
공구는 주로 1.4301(X5CrNi18-10) 또는 1.4303(X5CrNi18-10)과 같은 일반 상용의 스테인리스강으로 구성됩니다. 이는 특히 내식성이 우수하고 가공이 수월할 뿐만 아니라 경화처리가 필요하지 않습니다. 공작물의 소재에 따라 표면조도는 최대 Ra 0.5μm 또는 더 우수할 수 있습니다. 이렇게 윤곽, 원형관, 홈 혹은 중공이 비접촉 방식에 의해 최고의 정밀도로 생성됩니다. 정교한 공구의 형태로 인해 접근이 어려운 지점도 원활하게 가공되며, 심지어 부품 내부의 복잡한 형태도 가공할 수 있습니다."라고 그로스 씨는 설명합니다.
전기분해 기술에 근거
ECM은 전기분해 기술의 물리화학적 처리 방식을 이용합니다. 어떤 방식으로 작동하는지 프란츠 그로스 씨는 다음과 같이 설명합니다. "공구와 공작물은 전해질 용액에 들어 있습니다. 양쪽에 정전류 또는 맥동 전류의 직류 전원이 연결됩니다. 공구는 음극을 형성하여 양극인 공작물로 가까이 이동합니다. 그러면 방전 현상이 발생하여 공작물의 소재가 전해질 용액에 의해 제거되어 분리됩니다.
각 스트로크 전 깨끗한 전해질이 재충전됩니다. 이 절차는 폐쇄형 회로의 전해질 관리 시스템에 의해 이루어집니다. 고성능의 필터가 제거된 소재를 전해질에서 픽업한 다음 깨끗하게 세정하여 다시 공급합니다. "각 요건에 따라 전해질 관리 시스템은 개별 기계에 통합되는 부품을 형성하거나 여러 ECM 모듈을 별도의 구성요소로 공급합니다."라고 그로스 씨는 말합니다. 여과장치는 교체용 카트리지, 빗형 필터 프레스 또는 역세척 미세여과지를 갖추고 있습니다. 자동 처리장치가 pH 값을 중성 범위로 유지합니다. "전해질은 평균적으로 일 년에 한 번 교체해야 합니다."라고 ECM 전문가는 권고합니다.
ECM 공정에 대한 세부 설명 및 비디오: https://www.EMAG.com/technologies/ecm-electro-chemical-machining.html
문제되지 않는 소재의 경도
가공 목적에 따라 여러 공정으로 구분됩니다. 교차점의 디버링 및 라운딩에는 고정형 공구가 적합합니다. 음극 이동 시에는 일정량 이동하는 공구가 공작물 안으로 이동합니다. 이는 보링과 브로칭 가공과 비교할 수 있습니다. 3차원 가공을 위해서는 정밀한 전해가공(PECM) 방식이 사용됩니다. 이때 공구는 제조할 공작물의 주형입니다. "PECM 공정에서 이송 및 펄스 전자장치는 진동 운동과 중첩되어 현저히 작은 작동 간극에서도 정확한 오차를 보장합니다."라고 그로스 씨는 설명합니다.
이어서 "공구와 공작물이 비접촉 상태임에도 불구하고 이송 속도는 브로칭 가공 시 1분당 4mm이며, 매우 섬세한 부품 가공 시에도 여전히 0.2mm에 달합니다." 또한 실질적으로 소재와 전혀 무관합니다. "유일한 전제조건이라면 전기 전도율입니다."라고 덧붙입니다. 절삭 가공과는 달리 공정 및 공정 시간을 위한 소재의 경화처리는 실질적으로 중요한 역할을 하지 않습니다. "따라서 경화처리 전의 연질가공이 생략되기 때문에 공정 단계가 감축됩니다."
필요에 따라 선택 가능한 기계
디버링와 보링에는 EMAG 시스템의 CI 및 CS 타입이 적합합니다. CI는 Comfort Integrated의 약자이며 전해질 관리 시스템이 통합된 기계를 말합니다. "그 밖에 두 대의 CI 모듈은 CI Duo와 결합이 가능합니다. 그러면 이 두 장비는 통합된 전해질 관리 시스템을 공유하고, 따라서 생산량을 쉽게 확장할 수 있을 뿐만 아니라 ECM 공정에 자동화 시스템을 도입할 수 있습니다." CS는 중앙 전해질 관리시스템에 연결되는 표준 모델을 나타냅니다.
프리미엄 내장형(Premium Integrated/PI) 모듈은 정밀 전해가공(PECM) 공정을 위한 모듈식의 기계 플랫폼으로 절삭방법의 브로칭과 가공을 대체합니다. PI는 컴팩트한 크기의 CI을 기반으로 합니다. 전해질 관리 및 전기공학을 포함한 전체 기계 기술은 적재 가능한 기본 골격에 사용되었으며, 소요 설치면적은 단지 5.5m²에 불과합니다."라고 그로스 씨는 설명합니다.
모듈식의 가공실은 두 개의 모듈, 즉 발진기를 갖춘 PECM 모듈 또는 ECM 하강 모듈을 수용할 수 있습니다. 이 두 모듈은 여러 개의 동일한 공작물을 동시에 가공합니다. 또한 한 대의 중앙 전해질 관리시스템을 공유하는 여러 대의 기계 사용에 적합한 표준 모델(PS)도 있습니다.
기계의 제어는 폭넓게 이용되는 Siemens 사의 Simatik S7-1500 및 Sinumerik 840D sl 제어기에 의해 동일한 프로그래밍으로 실행됩니다. 프란츠 그로스 씨는 "새 공작물의 경우에는 저장되어 있는 적합한 타입 프로그램을 호출한 다음 적절한 매개변수만 입력하면 됩니다."라고 덧붙여 설명합니다.
ECM 공정의 장점 요약
- 공구 마모 감소(음극), 대량 생산에 적합한 전제조건 확보
- 표면조도 최대 Ra 0.05μm
- 정밀 가공
- 부품에 열적 영향 및 기계적 영향이 미치지 않아 소재 특성의 변형이 없음
- 경도, 인성 및 자성 변형 없음
- 소형의 얇은 벽 윤곽 생성
- 매우 높은 표면 구조의 반복 정밀도
- 고효율적이고 간단한 생산 공정, 디버링 또는 폴리싱과 같은 추가 작업 불필요
- 한 번의 작업으로 이루어지는 황삭 / 연삭 / 폴리싱
- 초내열 합금 가공
- 매크로 및 마이크로 구조의 동시 가공
EMAG ECM
EMAG ECM GmbH는 호이바흐(Heubach)에 소재한 전해가공 분야의 기술을 개발하는 EMAG 그룹의 자회사입니다. 이 회사는 절삭 공정의 디버링 공정 개발에 역점을 둡니다. 이 부분을 계획 수립시 자주 간과하기 때문에 전체 시스템의 경제성이 약화됩니다. EMAG은 이러한 틈새를 막기 위해 디버링을 포함한 전체 절삭 공정을 자체 개발하여 제공합니다. 이외에도 EMAG ECM은 현재 기존 절삭방식의 보링, 브로칭 및 가공 대신 사용할 수 있는 공정을 개발하였습니다. 이로써 고경도 소재의 가공과 전략적인 부품의 잔류물 없는 생산을 위한 솔루션을 제공합니다. ECM 기계를 사용하여 블리스크(Blisk)와 같은 엔진 부품을 절삭가공보다 더 생산적으로 처리할 수 있습니다. 전해가공 방식을 위한 서비스 범위는 상담, 개발 및 시제품 생산 그리고 완전 솔루션까지 선택의 폭이 넓습니다.
담당자
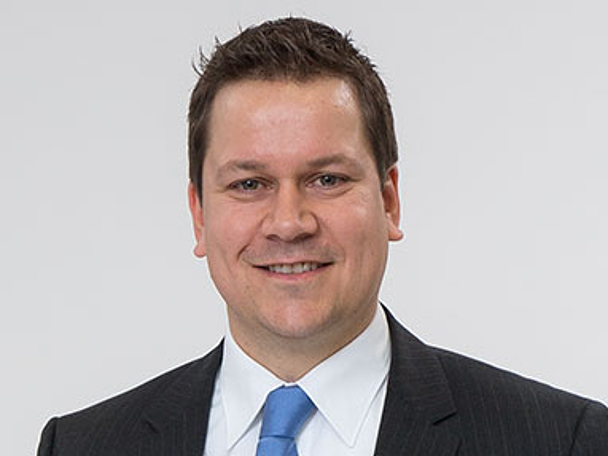