Sistemi di rivestimento laser
ELC LMD Series
Precision hard coating for long-lasting brake discs
Customized configuration for your production
The ELC LMD machines combine state-of-the-art laser coating technology with a flexible modular concept. This combination enables precision adaptation of the system to a wide range of production scenarios - from single part production to mass production. The modular concept of the ELC LMD machines enables optimum adaptation to your production requirements:
The Mono Variant
The mono variant with one process module is ideal for smaller production volumes, special coating tasks or as a prototype system for coating development.
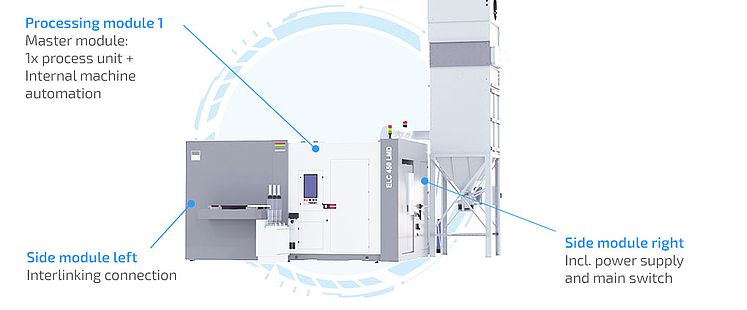
The Duo Variant
The Duo variant doubles the processing capacity with two process modules working in parallel - ideal for medium to large batch production.
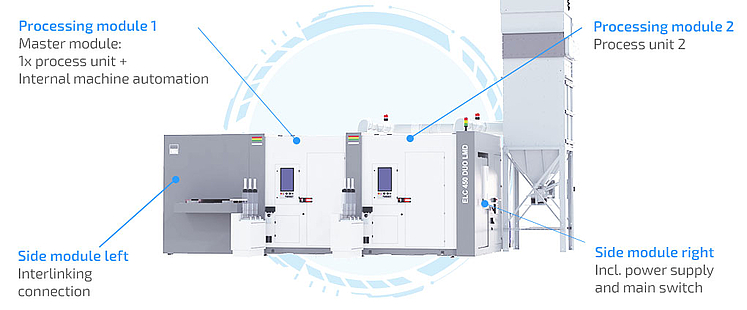
The Trio Variant
For maximum productivity, the Trio variant with three process modules is available, which enables the highest throughput rates. Each module works independently and can be serviced individually if necessary without interrupting overall production.
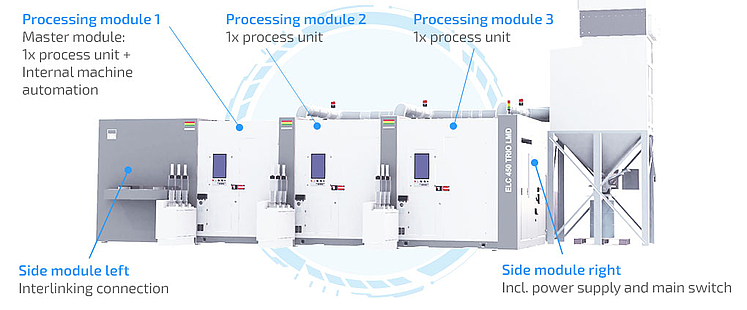

Precision machining thanks to intelligent process monitoring
The ELC LMD machines have a multi-stage monitoring system for consistent coating quality:
A high-resolution in-process camera continuously monitors the molten pool, enabling direct control of the coating process. The integrated surface scanner measures the coating thickness with precision during machining and ensures uniform coating results. The optional powder gas jet analysis ensures optimum distribution of the coating material and minimizes powder consumption.
- Integrated melt pool monitoring with high-resolution in-process camera
- Precision coating thickness control using a surface scanner
- Powder gas jet analysis for consistent process quality
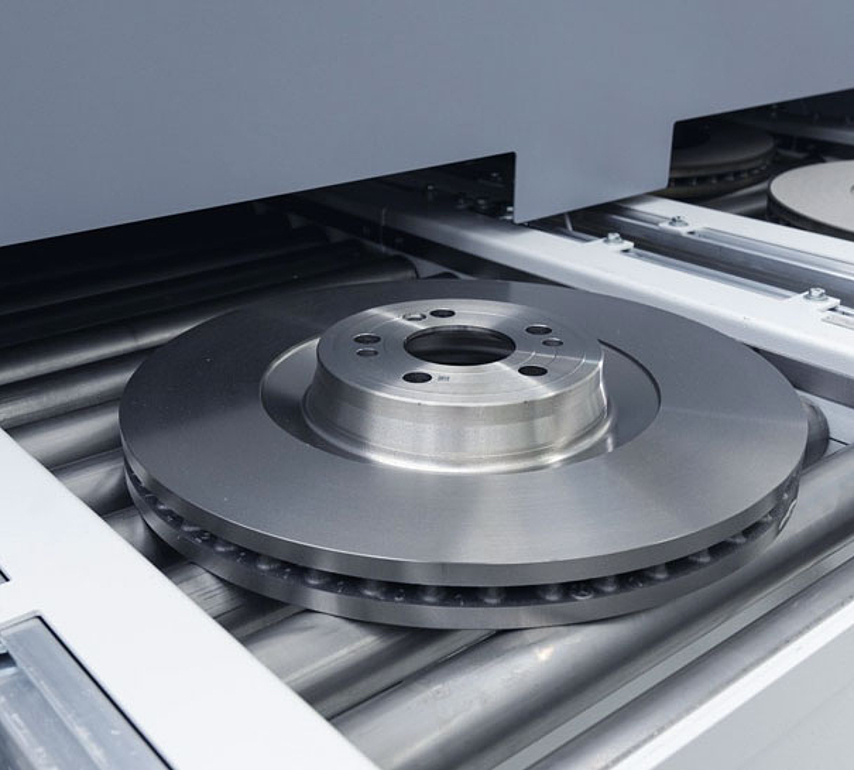
Sophisticated component handling for batch production
The fully integrated handling system was specially developed for the requirements of batch production:
Sequentially controlled friction roller conveyors transport the workpieces gently through the system. This reliably prevents damage to raw and finished parts. The integrated swivel device positions the components in just 0.8 seconds - an important factor for short cycle times in batch production.
The automated loading and unloading system reduces manual intervention to a minimum and ensures a continuous material flow.
- Gentle component transport thanks to sequentially controlled friction roller conveyors
- Panning time of just 0.8 seconds minimizes non-productive time
- Integrated handling system for automated loading and unloading
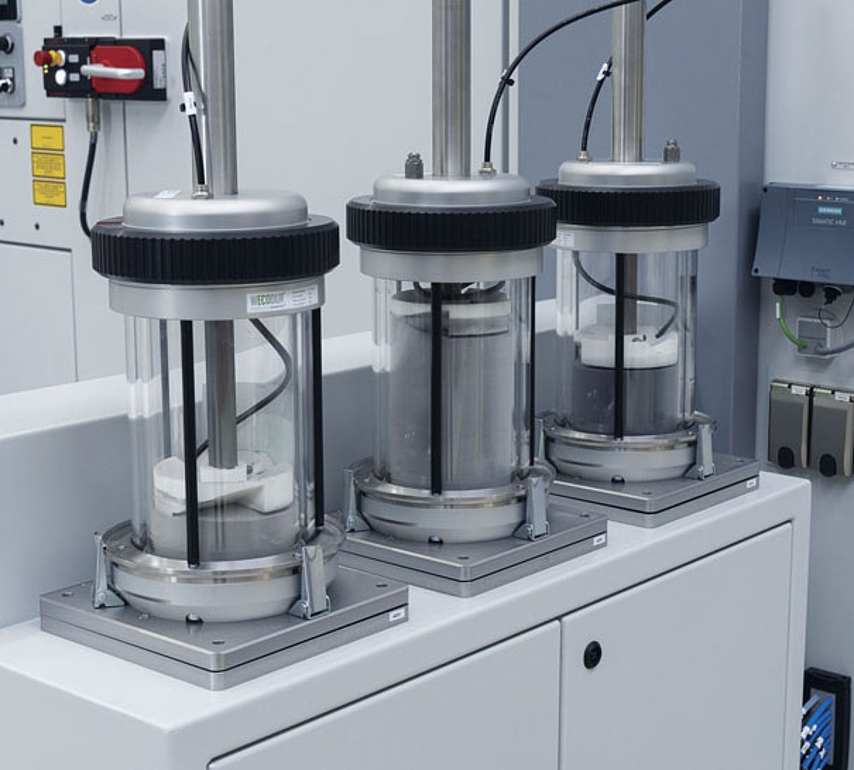
Flexible powder conveying system
The system can be equipped with various powder feed systems to optimally meet your specific coating requirements.
- Conveying capacity of up to 150 grams per minute for high application rates
- Material change in under 30 seconds for flexible production processes
- Even powder feed thanks to sophisticated top-down system
Efficiency through integration
The ELC LMD machines are designed as complete manufacturing cells. All process-relevant components - from the laser sources to the extraction system - are integrated into the system to save space. A central supply interface simplifies integration into existing production lines. The optional connection to handling systems enables complete automation of the coating process and integration into a fully integrated process chain.
Vantaggi ELC LMD Series
- Flexible modular concept - The system can be configured as a mono, duo or trio version and can be optimally adapted to different production requirements.
- Two-stage precision process - The coordinated coating process with adhesive and wear protection layer guarantees long-lasting brake disc coatings.
- Seamless quality control - Continuous process monitoring with in-process camera and surface scanner ensures constant coating quality.
- Minimized non-productive times - Fast swivel times of 0.8 seconds and process modules working in parallel ensure the highest productivity level.
- High system availability - The option of separate module maintenance minimizes downtimes.
- Compact complete solution - All process-relevant components are integrated into the system to save space.
- Flexible powder processing - The system processes different powder systems and enables quick material changes.
- Optimized process control - The swivelling process table and efficient heat management ensure stable coating results.
- Simple integration - The central supply interface allows the system to be easily integrated into existing production lines.
Visit the EMAG Media Center for more Information
Whitepaper Laser Metal Deposition: Perfect and reliable coating of brake discs
To the WHITEPAPER
Pezzi
The Right Manufacturing Solution for Every Workpiece
Tecnologie
Complex Manufacturing Systems from a Single Source thanks to a High Range of Technologies
Euro 7 standard mandates lower non-emissions particulate matter - the previous passenger car brake disc is to become obsolete and discontinued model.…