14/05/2020 - Oliver Hagenlocher - Press
W 11 CNC from EMAG Weiss—Manual CNC-Supported External and Internal Cylindrical Grinder
The EMAG Group is breaking new ground with the W 11 CNC cylindrical grinder from EMAG Weiss. The company from Salach, near Stuttgart, Germany, is primarily known for its turning and grinding machines intended for high-volume production. With its W 11 CNC, it now aims to reach those who produce individual parts, prototypes or small batches. The W 11 CNC also offers users many carefully engineering operating aids, including the machine’s optimal ease of operation – allowing it to be operated using an intuitive touchscreen control panel or a traditional button panel.
Immagini
The W 11 CNC is a manual CNC-supported external and internal cylindrical grinder. Bernd Weiß, Managing Director of EMAG Weiss, explains the advantages this provides its users: “The W 11 CNC is a conventional universal cylindrical grinder with a two-in-one concept, achieved by using a modern CNC control unit. Since this system can be easily operated using its touchscreen control panel, it allows the user to ignore previous tedious tasks so they can fully focus on the machining of the part,” explains Bernd Weiß.
Optimization through Automating Time Consuming Processes
EMAG Weiss is an expert when it comes to grinding technology, and that is how they know exactly what processes are the most time consuming and perfect for automating to improve the efficiency of the grinding process. Dressing the grinding wheel is just one example of this type of process. “We are grinders ourselves, so we know exactly how time-consuming dressing a grinding wheel can be, especially when done manually. First, you most remove the workpiece, then bring it to the diamond, set the dressing amount and speed, then return to the workpiece and consider the new values after dressing with these values. This takes time, and, that’s precisely why this is one of the processes we’ve automated in the W 11 CNC. If the diamond and workpiece are set, you can dress in full automatic mode, i.e. radii, bevels, cones and much more. The dressing amount is then adjusted automatically,” explains Bernd Weiß.
In addition to dressing, the CNC control panel provides additional advantages: For instance, several diameters can be automatically ground in a single clamping operation. In path mode, the W 11 CNC also enables the grinding of cones and contours. The automatic retraction of the grinding wheel to a safe changing position is just one of many convenient features that ensure fast tooling times.
Modern and Fast Control Unit Geared for Grinding
Just like the rest of the machine, the modern control panel was designed entirely for the optimization of the grinding process. All data entry and control operations are performed via touchscreen. The machine can be programmed using a dialog interface or DIN ISO programming. Since all the software is based on Windows, data can be quickly exchanged on a desktop computer via a USB interface. Grinding programs can be written in the development department and then quickly and easily transferred to the machine. The standard version of the software contains all common grinding cycles. However, if required, a DXF converter, a geometry editor and even programming of special custom grinding cycles by the experts at EMAG Weiss are also available. “Obviously, users can also perform simple plunge-cut or longitudinal grinding processes manually without using the control unit. In this case, it merely serves as a monitor for data entry. However, the interesting feature is that this manual data can be easily transferred to the control unit using “teach-in” so that they are automatically ready for subsequent parts. This truly provides an optimal degree of freedom when operating the machine and at the same time simple grinding processes can be programmed in no time,” adds Bernd Weiß.
Modular Machines for Every User
The versatility of the W 11 CNC is not only apparent in the machine’s flexible control unit, but even the basic machine configuration is flexible, so the machine can be used for a variety of different things.
Featuring an MK 4 to MK 6 spindle mount and a speed of up to 1,000 rpm, the workpiece headstock is available with a large selection of clamping devices. This is matched by a foot switch-operated tailstock having an MK 4 tool socket that enables clamping of up 250 kg (551 lbs) between the tips. The core of the machine is the grinding headstock on precision bearings with an output of up to 11 kW (15 hp) that can be fitted with grinding wheels up to 500 mm (20 in) in diameter and 120 mm (5 in) in width. Here again, there are a number of options available, such as control of the grinding wheel’s circumferential speed (Vc) or GAP control.
“Additionally, the grinding headstock can be equipped with a continuously programmable B-axis, which continues to increase the machine’s versatility. This means that the grinding spindle can be extended with an additional grinding head for external or internal grinding, allowing for quick machining of various grinding positions using different tools in a single clamping operation. Allowing for even complex workpieces to be ground in no time,” according to Bernd Weiß.
Positive Market Response
“So far, we’ve only received positive feedback from customers who use the W 11 CNC. This is mainly due to the flexibility that the machine offers users and the quality parts that it produces. By joining EMAG we will now be able to build even more machines, which will decrease delivery times,” concludes Bernd Weiß.
Also interesting: EMAG blog post - interview with Bernd Weiß, Managing Director of EMAG CNC-Technik Weiss GmbH
Referenti
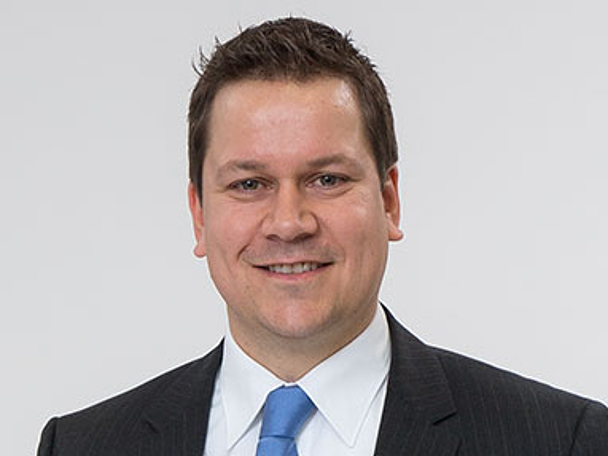
Oliver Hagenlocher
Zona
Press and Communication