15/06/2020 - Oliver Hagenlocher - Stampa
VL 1 TWIN di EMAG: riduzione massiccia dei costi per pezzo di ingranaggi conici
Gli ingranaggi conici per autovetture sono componenti realizzati in massa. I subfornitori producono milioni e milioni di ruote dentate centrali per il rotismo del differenziale. Non c’è da stupirsi: in ogni singolo differenziale sono presenti quattro di questi ingranaggi. Inoltre, è in continua crescita il numero di veicoli a trazione integrale (ciascuno dei quali dispone di un doppio rotismo del differenziale). Di conseguenza, aumenta anche il numero di ingranaggi conici. Pertanto, molti subfornitori si concentrano sui processi produttivi di questo componente. Si cercano nuove soluzioni di ingegneria meccanica per garantire costi per pezzo sensibilmente minori mantenendo elevata la qualità. La soluzione adatta è stata sviluppata da EMAG con il nuovo centro di tornitura pick-up a doppio mandrino VL 1 TWIN, che consente di lavorare ad alta velocità simultaneamente due ingranaggi conici uguali nella stessa area di lavoro. Inoltre, è possibile anche caricare la macchina tramite cella robot e tavola orientabile. In questo modo il tempo ciclo si riduce a soli 4,5 secondi.
L’avanzata dei veicoli a trazione integrale è inarrestabile. Ad oggi in Germania, ad esempio, costituiscono il 20% dei veicoli di prima immatricolazione. In altri Paesi, come ad esempio la Svezia o la Svizzera, la percentuale è ancora più elevata. Questo sviluppo del mercato si associa all’aumento significativo delle cifre di produzione degli ingranaggi conici, che sono soggetti a una crescente pressione dei costi come tutti i componenti automobilistici realizzati in massa. Il relativo processo produttivo inizia per lo più con un processo di forgiatura complesso, durante il quale si ottiene la caratteristica dentatura dell’ingranaggio conico. Seguono poi diversi processi di tornitura per produrre la superficie conica opposta alla dentatura, un piccolo gradino sulla superficie conica, la foratura interna e una superficie frontale. In base alla singola soluzione di produzione del produttore, questi processi possono avvenire direttamente nell’ambito della lavorazione su temprato conclusiva o, in alternativa, i singoli componenti possono essere torniti prima da non temprati e poi da temprati. “In ogni caso, si tratta di gestire grandi quantitativi di produzionesenza errori, in maniera rapida ed efficiente dal punto di vista dei costi” spiega Daniele Loporchio, Technical Sales Manager di EMAG. “È per questo che abbiamo progettato la VL 1 TWIN. Questa macchina è ideale per la lavorazione su temprato e non temprato dei più diversi ingranaggi conici con diametro fino a 75 mm.”
Solo 20 secondi di tempo ciclo
Il principio alla base di questo centro di tornitura pick-up riveste un ruolo decisivo. La macchina è dotata di due mandrini pick-up (9,9 kW/136 Nm a 40% rapp. inserzione), grazie ai quali viene sempre eseguita la lavorazione in parallelo di due ingranaggi conici uguali (OP 10 – OP 10) ad alta velocità: i due mandrini caricano e scaricano l’area di lavoro in soli 5-6 secondi. Le fasi di lavorazione sopra descritte vengono quindi eseguite in sequenza e in un’unica fase di serraggio, con un tempo ciclo complessivo da 25 a 40 secondi (a seconda delle dimensioni e del tipo di componente). Il tempo truciolo/truciolo medio è quindi di appena sei secondi. Una speciale soluzione di serraggio riproduce in negativo la dentatura del componente e lo mantiene stabilmente in posizione per tutto il tempo. Inoltre, con la VL 1 TWIN è possibile eseguire forature complete. Perfette per realizzare il foro centrale dell’ingranaggio conico.
L’approccio complessivo alla base della macchina permette rendimenti elevati a intervalli ridotti. Inoltre, gli sviluppatori sono riusciti a ridurre sensibilmente il costo per mandrino grazie a un monitoraggio consistente dei costi. Anche questo contribuisce all’ottenimento di costi per pezzo molto bassi.
Attenzione anche alla qualità dei componenti
La qualità dei componenti e la sicurezza di processo sono garantite da una serie di caratteristiche specifiche delle dotazioni EMAG. La VL 1 TWIN, ad esempio, presenta un basamento in Mineralit® che riduce sensibilmente le oscillazioni durante il processo di tornitura. Da ciò deriva direttamente un aumento della durata degli utensili (e quindi una riduzione dei relativi costi). Le teste portamandrino possono traslare in modo indipendente tra loro. Diametro e lunghezza (direzione X / Z) dei due componenti possono quindi essere corretti indipendentemente l’uno dall’altro in caso di scostamenti, ad esempio dopo la sostituzione degli inserti. Un altro elemento importante è l’azionamento lineare non soggetto ad usura nell’asse X, comprensivo di sistemi di misurazione diretta della corsa. Dispone di un’accelerazione di 8 m/s2 con un’elevata precisione a lungo termine, accresciuta ulteriormente dalle guide a rulli in tutti gli assi lineari.
Caricamento della VL 1 TWIN tramite robot
Le operazioni concrete legate alla produzione degli ingranaggi conici – comprese automazione e concatenazione – vengono sviluppate con estrema flessibilità da EMAG e adattate alle attività del cliente. La base tecnica di partenza per l’alimentazione dei pezzi è l’automazione pick-up integrata, che è responsabile del passaggio dei pezzi all’interno della macchina. Per aumentare il volume produttivo, gli sviluppatori EMAG possono combinare la VL 1 TWIN con una potente cella robot e una tavola orientabile. In questo caso, la pinza viene adattata in maniera precisa alla forma del componente. I portacomponenti preposizionati semplificano le operazioni di trasporto, carico e scarico. In questo modo, da una parte il tempo ciclo diminuisce fino a 4,5 e i singoli workflow produttivi sono riproducibili in maniera molto semplice, dall’altra è possibile integrare nel processo ulteriori processi, come ad esempio la misurazione, la marcatura e la pulizia, parallelamente al tempo ciclo.
Inoltre, è possibile caricare due VL 1 TWIN con la cella robot adatta o in alternativa con il sistema di automazione TrackMotion di EMAG (OP 10 – OP 10, OP 10 – OP 10). In questo caso il cosiddetto TransLift (un carrello sollevatore/ribaltatore con pinza elettrica) preleva i pezzi grezzi da un nastro di alimentazione e li trasporta fino alle macchine. Così facendo, le due macchine vengono caricate e scaricate celermente – il TransLift è una soluzione potente ma al contempo compatta per quattro mandrini.
Essenziale anche per motori elettrici
Costi di investimento e produzione ridotti, tempi ciclo brevi ed elevata sicurezza del processo: sono le basi da cui sono partiti gli ingegneri meccanici per rispondere alle sfide lanciate dalla produzione di ingranaggi conici. “Indipendentemente dal tipo di propulsione, sia il classico motore a combustione che il motore elettrico, il differenziale è un componente essenziale. Chi vuole modernizzare la propria infrastruttura produttiva e prepararsi all’aumento dei quantitativi di pezzi da lavorare, dovrebbe rivolgere la propria attenzione proprio a questa tecnologia”, conclude Loporchio. “Siamo convinti che la VL 1 TWIN sia la soluzione ideale per molti produttori di ingranaggi conici.”
Immagini
Download
Referenti
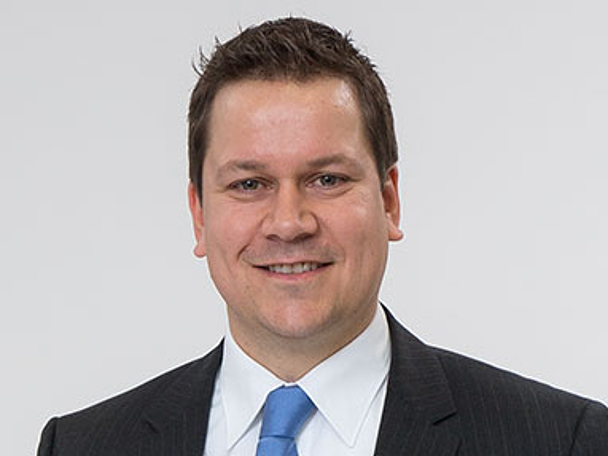
Oliver Hagenlocher
Zona
Press and Communication