02/06/2021 - Oliver Hagenlocher - Stampa
Soluzione produttiva per autocarri: EMAG offre una soluzione di produzione compatta per i mozzi delle ruote per autocarri
L’e-mobility sta prendendo sempre più piede non solo nel settore delle automobili ma anche, da tempo, nel settore degli autocarri, dando il via a una competizione per guadagnarsi le fette di mercato future. Oltre ai produttori rinomati, nuovi marchi nuovi e start up stanno conquistando il mercato. Le prime grandi commesse per questi nuovi prodotti dimostrano che la posta in gioco è alta e non è ancora detta l’ultima parola su chi si imporrà sul mercato. Una cosa però è chiara: la produzione nel settore dei veicoli utilitari è sempre più diversificata e complessa. Per soddisfare questi requisiti i produttori e i fornitori puntano soprattutto su sistemi di produzione versatili.
Consapevole di questa sfida, EMAG ha sviluppato una soluzione di produzione compatta per i mozzi delle ruote per autocarri, non esclusivamente per i camion elettrici.
Immagini
Durante la fase di pianificazione della linea di produzione per i mozzi delle ruote per autocarri, ci si è orientati verso le soluzioni produttive compatte tipiche di EMAG. L’ingombro ridotto è dovuto in gran parte all’elevato grado di automazione e alla struttura verticale delle macchine pick-up verticali impiegate. In combinazione con il sistema di automazione TrackMotion, che attraversa praticamente le macchine, è possibile una disposizione particolarmente ravvicinata delle macchine. Vengono realizzate celle di produzione compatte che possono essere duplicate o moltiplicate a seconda della quantità di pezzi da produrre.
Combinazione ideale di centro di tornitura pick-up e TrackMotion
Il funzionamento preciso delle soluzioni produttive altamente flessibili EMAG è dimostrato dalla struttura della linea: i mozzi delle ruote per autocarri vengono lavorati solitamente in tre sole fasi di serraggio, quindi con tre mandrini o macchine. Nella OP 10 viene eseguita la lavorazione di tornitura del contorno esterno ed interno. La sgrossatura e la finitura di un lato vengono eseguite in un’unica fase di serraggio. Dopo il ribaltamento del mozzo della ruota da parte del TrackMotion, nella OP 20 viene lavorato il secondo lato. Utilizzando la torretta con utensili motorizzati è possibile eseguire anche le operazioni di foratura per la realizzazione di fori filettati per le viti. Nella OP 30 viene eseguita la finitura del pezzo e la fresatura delle scanalature. Anche in questo caso viene utilizzata la torretta con utensili motorizzati per filettare i fori. Queste macchine vengono concatenate con il sistema di automazione EMAG TrackMotion, nel quale una pinza si muove su una rotaia (track) lungo un asse lineare. Dall'alimentazione dei pezzi grezzi, la pinza trasporta il pezzo da una macchina o fase di processo all'altra fino alla rimozione dei pezzi finiti. I vantaggi: da un lato l’utilizzatore può modificare l'intero sistema in qualsiasi momento, ad esempio è possibile "scollegare" una macchina dal processo se alcune fasi non sono necessarie per un determinato pezzo oppure per variare la sequenza di processo di una macchina. Quest'operazione può risultare necessaria in caso di diversi tipi di mozzi a causa della diversa sequenza di serraggio. Ciò consente di ridurre al minimo i lunghi tempi richiesti dal riattrezzamento su più dispositivi di serraggio. Dall'altro lato EMAG consente di integrare all'interno di questa catena più macchine che svolgono parallelamente la stessa operazione. In questo caso il sistema TrackMotion distribuisce i pezzi sulla macchina di volta in volta libera. Così, durante gli interventi di allestimento su una macchina, la linea di produzione non è mai completamente ferma.
Il centro di tornitura pick-up VL 8
Il centro VL 8 utilizzato dispone di un diametro dell’autocentrante di 500 mm, il mandrino pick-up è in grado di prelevare pezzi con un diametro fino a 400 mm. Nella versione high-performance (opzione), il mandrino principale ha una potenza motrice fino a 71,7 kW e una coppia di 1102 Nm (con rapporto d’inserzione 40%) e consentendo così l’asportazione di truciolo per una lavorazione velocissima dei mozzi delle ruote per autocarri. Viene inoltre utilizzata la torretta proprietaria di EMAG. Questa può essere equipaggiata con 12 utensili rotanti o, a scelta, come torretta per utensili motorizzati con frese e punte a forare azionate. Il basamento della macchina è in calcestruzzo polimerico Mineralit. Questo materiale garantisce vibrazioni ridotte durante la lavorazione, con una durata elevata degli utensili e un’eccellente qualità della lavorazione.
EDNA – Piattaforma dell’industria 4.0
Non da ultimo il concetto “Industria 4.0” riveste un ruolo di primo piano per EMAG. Con EDNA, acronimo di EMAG DNA, l’azienda ha sviluppato un ecosistema software modulare esclusivo. Questo ecosistema consente non solo migliorare la configurazione e l’uso delle singole macchine e di interi sistemi produttivi: le applicazioni basate sull'analisi dei dati offrono anche la trasparenza necessaria nel processo produttivo generale e costituiscono il punto di partenza per la smart factory.
Per quanto riguarda la manutenzione delle macchine, con “EDNA Healthcheck”, ad esempio, è possibile riconoscere in anticipo e senza particolare sforzo l’usura degli azionamenti degli assi e pianificare tempestivamente gli interventi di manutenzione necessari.
Flessibilità, velocità, precisione ed elevata produttività – grazie a questi fattori, negli ultimi decenni EMAG si è assicurata una ottima posizione di mercato nell'ambito delle linee di produzione. Ciò vale ovviamente anche per la linea qui presentata per la lavorazione dei mozzi delle ruote per autocarri. Con questi vantaggi EMAG rivestirà sicuramente un ruolo di primo piano anche nel settore dei veicoli utilizzati.
Referenti
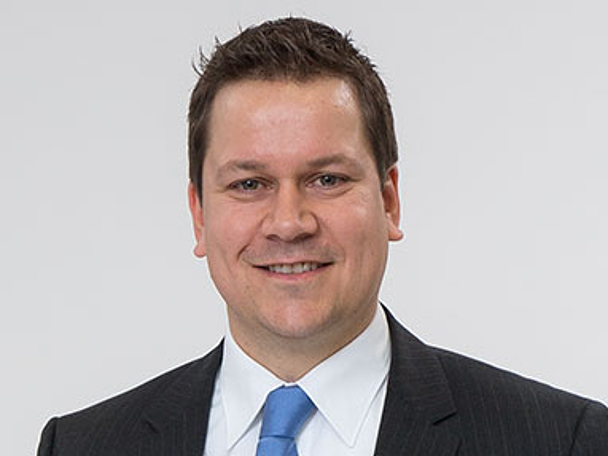
Oliver Hagenlocher
Zona
Press and Communication