04/11/2020 - Oliver Hagenlocher - Stampa
Macchina per pulizia laser LC 4-2: rapidi processi di pulizia e ottimizzazione delle superfici dei componenti
La pulizia industriale è una procedura piuttosto comune: molti componenti presentano infatti impurità, come olio e colla, o sono rivestiti da strati di ossido, ruggine, fosfato o vernice, che devono essere rimossi prima della lavorazione successiva. Partendo da queste premesse, i responsabili della pianificazione produttiva puntano tutto sull'elevata efficienza dei processi laser di pulizia e rimozione degli strati. Con la nuova macchina per pulizia laser LC 4-2 gli specialisti di EMAG LaserTec hanno ulteriormente perfezionato tali processi. La macchina LC 4-2 garantisce infatti una pulizia eccellente dei componenti a fronte di un ingombro minimo e di una manutenzione ridotta. Può inoltre essere utilizzata come soluzione stand-alone a caricamento manuale o integrata in una linea produttiva in modo completamente automatizzato e consente di ottenere dei risultati affidabili e riproducibili. Questa tecnologia può venire impiegata inoltre per la funzionalizzazione delle superfici, ad esempio per migliorarne l'umettabilità. Che cosa contraddistingue l'ingegneria meccanica di EMAG in questo settore?
Immagini
Il principio alla base della pulizia laser è affascinante: la radiazione laser pulsata colpisce la superficie con un'elevata potenza di picco. Poiché il materiale evapora istantaneamente, viene riscaldato solo uno strato ridotto del componente. In questo modo è possibile rimuovere dal componente, impulso dopo impulso, molti tipi di impurità o rivestimenti: lubrorefrigeranti e oli, strati di ossido e grafite, ruggine, strati di vernice e di fosfato. È inoltre possibile sfruttare questa tecnologia per preparare le superfici per le fasi di lavorazione successive (ad esempio l'irruvidimento). In breve, il processo risulta estremamente flessibile e particolarmente efficiente da un punto di vista energetico. Durante lo sviluppo delle nuove macchine occorre invece puntare sul know-how, come sottolinea Nikolas Meyer, direttore vendite di EMAG LaserTec. "Molti parametri di processo essenziali, come la durata di lavorazione, devono poter essere adattati al tipo di lavorazione nel modo più semplice possibile attraverso l'unità di controllo della macchina. In caso contrario l'applicazione di tale tecnologia diventerebbe troppo complessa. Questa tecnologia deve inoltre essere flessibile sotto ogni punto di vista; ad esempio deve poter funzionare come soluzione autonoma o all'interno di una linea di produzione. Questi e altri requisiti vengono pienamente soddisfatti dalla nostra nuova macchina per pulizia laser LC 4-2, che vanta la comprovata tecnologia modulare di EMAG. La nostra soluzione è estremamente sicura dal punto di vista del processo, oltre ad essere efficiente e compatta".
Gli specialisti della lavorazione laser del gruppo EMAG hanno alle spalle una lunga esperienza: nella sede di Heubach, presso Schwäbisch Gmünd, vengono prodotti da circa 15 anni impianti chiavi in mano di saldatura laser in grado di produrre componenti complessi degli organi di trasmissione. Questo know-how è stato applicato in modo mirato allo sviluppo di un sistema di pulizia laser per componenti con diametro massimo di 200 mm e altezza massima di 350 mm. Cinque requisiti centrali sono stati al centro della nostra attenzione:
1. Integrazione: soluzione in linea o stand-alone
Il complesso processo produttivo della saldatura laser di differenziali è composto da più operazioni singole: dal riscaldamento a induzione (se necessario) e dalla giunzione alla saldatura laser al controllo conclusivo. Tutto è preceduto però da un processo di pulizia, poiché dalla corona e dalla scatola del differenziale è necessario rimuovere gli strati di fosfato o le impurità. Questi e altri scenari applicativi della produzione in serie di componenti automobilistici erano ben chiari agli specialisti EMAG durante la fase di sviluppo dell'LC 4-2. La macchina può dunque essere integrata in linee di produzione o utilizzata come unità autonoma. Dispone difatti di una tavola circolare separata dall'area di lavoro, che può essere caricata o scaricata, se necessario, in modo automatizzato (o manuale) in parallelo. Opzionalmente è inoltre possibile serrare contemporaneamente due componenti, mentre altri due vengono sottoposti al processo di pulizia. Ciò consente di ridurre i tempi di ciclo, eliminando i tempi morti o le interruzioni nel flusso del materiale.
2. Processo: elevata sicurezza garantita
Un vantaggio essenziale di questa tecnologia è l'impiego di "luce" fortemente concentrata durante la pulizia. Nel caso della LC 4-2 viene utilizzato un laser da 200 watt estremamente efficiente, che viene attivato solo per pochi secondi per ogni componente. Nelle linee di produzione è estremamente importante che il posizionamento del raggio laser venga eseguito con un'elevata sicurezza di processo. In alternativa è possibile posizionare l'ottica della macchina per la pulizia manualmente. Il software opzionale "EMAG EC Clean" registra tutti i dati di processo e facilita la gestione degli errori.
3. Flessibilità: soluzione adatta a numerose operazioni
La tecnologia al laser della macchina LC 4-2 è adatta a numerosi materiali e svariate operazioni. La sua durata di impulso estremamente breve riveste un ruolo particolarmente importante, poiché diminuisce drasticamente il tempo di interazione riducendo al minimo i danni apportati alle superfici. Dall'altro lato la durata ridotta degli impulsi consente una potenza di picco elevata. Questa caratteristica può essere sfruttata per ottenere determinate caratteristiche superficiali, ad esempio una migliore aderenza.
4. Costi: ingombro in pianta e tempo attivo ridotti
Rispetto ai sistemi di lavaggio industriali tradizionali, la pulizia laser con il modello LC 4-2 garantisce costi per pezzo inferiori. Da un lato infatti il nuovo modello necessita di un ingombro in pianta ridotto, pari a soli 4,5 m². Dall'altro lato il laser viene attivato solo per pochi secondi ed è praticamente esente da manutenzione. L'intero processo di pulizia o di trattamento della superficie si svolge in pochi secondi e in modo completamente automatizzato. Al contrario gli impianti di lavaggio tradizionali hanno spesso un ingombro in pianta di oltre 20 m² e richiedono un apporto continuo di energia per regolare la temperatura della soluzione di lavaggio. A ciò si aggiungono i processi di risciacquo e asciugatura, che rallentano ulteriormente il processo produttivo.
5. Ambiente: tecnologia ecosostenibile
Un altro vantaggio della pulizia laser è l'elevata compatibilità ambientale, soprattutto rispetto al lavaggio chimico a umido che fa uso di detergenti che, una volta completato il processo, devono essere smaltiti. I residui rimasti sul componente lavorato possono causare inoltre problemi nei processi produttivi a valle. La pulizia laser rende superfluo invece l'uso di detergenti.
L'ingegneria meccanica di EMAG offre numerosi vantaggi
"Nel complesso abbiamo realizzato una soluzione completa potente e altamente flessibile", sintetizza Nikolas Meyer. "La macchina può essere utilizzata sia in modalità stand-alone che all'interno di una linea automatizzata. Vanta un ingombro in pianta ridotto, può essere configurata facilmente per svariate operazioni e garantisce costi per pezzo inferiori grazie ai suoi sistemi laser e di caricamento. Siamo certi che queste caratteristiche ne garantiranno il successo sul mercato. Questa tecnologia è particolarmente adatta ad applicazioni di saldatura o di incollaggio per i settori automobilistico e aerospaziale, che sono caratterizzati da elevati volumi di produzione. Un fattore decisivo per il suo successo è anche la modularità delle macchine di EMAG. Questo costruttore di macchine della Germania meridionale realizza infatti le sue soluzioni di sistema personalizzate "in modo modulare". Vengono quindi impiegati componenti di alta qualità ampiamente comprovati. Ovviamente tutto ciò vale anche per la macchina per pulizia laser LC 4-2".
LC 4-2: vantaggi in sintesi
- Basso consumo energetico e manutenzione ridotta
- Possibilità di impiego in linee di produzione o in modalità stand-alone
- Ingombro in pianta ridotto
- Processo stabile, indipendente dalla qualità dell'acqua e dagli additivi (a differenza dei processi di lavaggio)
- Eliminazione di quasi tutte le impurità e i rivestimenti
Referenti
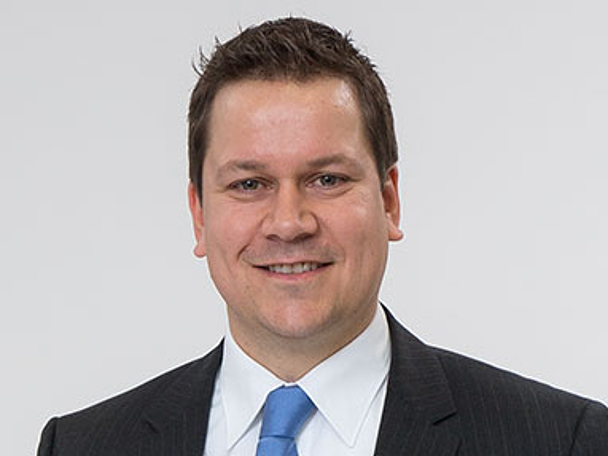
Oliver Hagenlocher
Zona
Press and Communication