06/09/2021 - Oliver Hagenlocher - Press
Laser Metal Deposition: EMAG develops production solution for coated brake disks
The car brake disk of the future is wear-resistant – and lasts as long as the car. This is made possible by a two-layer carbide coating that is applied to the disk using laser welding. EMAG LaserTec is currently engineering the associated integrated machine solution with the name ELC 450 LMD. The machine incorporates laser metal deposition into a comprehensive process that includes quality assurance. What exactly is special about the production solution from EMAG?
Modern brake systems have always generated many fine dust particles. But now there is a new challenge: brake oxidation. Since recuperation of the motor produces enough braking effect, the brakes on electric cars are infrequently used and may even start to rust. With this in mind, car manufacturers are rethinking brake disk technology. As a result, drum brakes could experience a renaissance, releasing fewer fine particles into the environment. For example, carbide-coated brake disks, which are free from wear and corrosion, are an interesting alternative, since this type of disk does not produce any fine particles and lasts as long as the car.
Focus on efficient coating technology
For now, however, coating the disks with tungsten carbide or similar materials still poses a particular challenge. The most frequently used process for this is high velocity oxygen fuel spraying (HVOF), where the coating is “fired” at high speed onto the component – a method that is associated with high levels of material loss. Is there a more efficient and controlled alternative? “Component suppliers came to us with this question some time ago, because our laser expertise is generally a perfect basis for laser coating methods,” says Dr. Andreas Mootz, managing director of EMAG LaserTec based in Heubach near Aalen. “We also have a lot of experience in developing integrated processes. We brought both together to develop the new ELC 450 LMD, which ensures an extremely controlled laser metal deposition process. Here, a bond layer and the carbide layer on top of it are each applied to the brake disk using a laser welding process. So, almost no material is lost.”
A look at the details of the machine reveals exactly how this process works. It contains a turntable with five stations, on which each component passes through a total of four times (twice per side as the coating consists of two layers):
- Weighing: In the first station, the component is first weighed uncoated. This value is used as a reference to be able to determine the coating weight later (when the component is weighed again after one pass). The result indicates whether the correct quantity of material is on the disk.
- Laser cleaning: Then the blank is cleaned in the next station to remove working materials and dirt. This involves applying pulsed laser radiation to the surface, which vaporizes the material immediately.
- Preheating: In the third station, induction technology from EMAG eldec ensures an ideal processing temperature at the component.
- Laser cladding: Now, the actual laser coating starts. One layer is applied per pass, first a bond layer, then the carbide coating. The entire process benefits from the sophisticated design of the laser tool, to which the material powder is fed through a channel. The material fuses with the disk surface at the melting point of the welding process.
- Flip-over unit/measuring: The final station on the turntable is a measuring and flip-over unit. The latter is used when the first side of the component has completed two coating passes and the second side needs to be done next.
Integrated solutions from EMAG
All in all, the development of the new coating technology is not yet quite complete, as Mootz confirms: “We’re still conducting coating tests with the customer at the moment. But we can already see that we’ll be able to offer our customers an extremely efficient solution in the future. The combination of high-precision laser coating technology with other processes like cleaning, preheating and quality assurance measures like weighing guarantees the necessary process control, which is of course vital when dealing with large quantities in car manufacturing.” And, true to form, EMAG offers another advantage: the machine manufacturer also develops tailor-made production technology for upstream turning processes on the disk blank and final grinding processes on the fully coated brake disk. This means that the customer will be able to get the complete production solution for the next generation of brake disks from EMAG, if they wish. “With our extensive process expertise in many fields of application, we stand for integration solutions ‘from a single source.’ Soon, we will also be able to provide this for coated brake disks,” says Mootz in conclusion.
Interview
A conversation with Dr. Andreas Mootz, managing director of EMAG LaserTec, about the benefits of laser metal deposition and the corresponding new machine, ELC 450 LMD. Read more on our blog:
“We are developing a comprehensive solution for coating brake disks” - EMAG Group - Company Blog
Immagini
Referenti
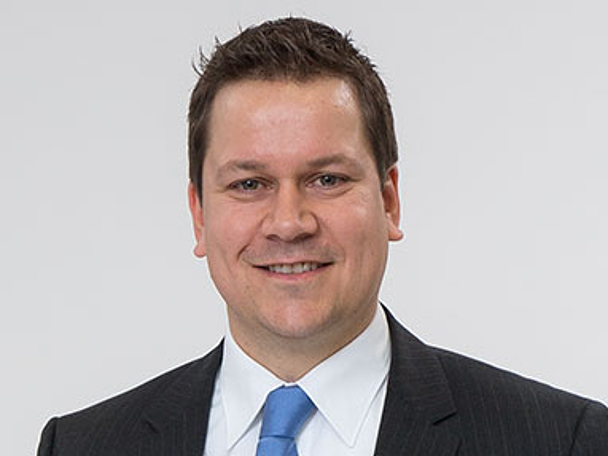
Oliver Hagenlocher
Zona
Press and Communication