25/04/2024 - Oliver Hagenlocher - Press
EMAG at the GrindingHub 2024 – Grinding technology for the low-emission mobility of the future
Grinding is a key technology for the resource-saving and low-emission mobility of the future. Examples of this include electric drives, which place the highest demands on the precision and surface properties of transmissions and engine components, or brake discs with reduced fine dust and hard coatings that are difficult to machine. EMAG will be presenting solutions for these machining requirements at Grinding Hub 2024 in Stuttgart. International grinding experts from production and planning are invited to experience the latest designs and developments at the EMAG stand in Hall 9, Stand C31.
Immagini
The VLC 450 DG brake disk grinding machine:
In March 2024, the European Parliament adopted the EURO 7 standard. For the first time, it sets limit values for brake particle emissions for cars and light trucks. Irrespective of the drive system used, a switch to new brake technology is necessary. The most promising approach to reducing particulate matter in the braking system is currently the use of hard-coated brake discs. The friction layer consists of a soft matrix with carbides, e.g. titanium carbide. Due to the fundamentally different cutting behavior of the two materials, the design and development of suitable grinding tools and the design of the static and dynamic machine properties as well as the spindle drives is very complex. Our solution: the VLC 450 DG - a double-sided surface grinding machine for hard-coated brake discs. This machine was developed with a focus on rigidity and durability in order to meet the high requirements of batch production. The vertical design ensures optimum removal of the hard material particles without damaging the machine axes and excellent accessibility for set-up and maintenance work. Workpiece handling by means of a feed shuttle and pick-up spindle simplifies automation and offers short chip-to-chip times. The machine concept is based on decades of experience in the manufacture of vertical turning and grinding machines. An intelligent sensor concept enables adaptive process control. This makes the VLC 450 DG a reliable solution for brake disc production that meets the highest productivity levels and workpiece quality requirements. During three years of successful prototype testing, the first double-sided surface grinding machine has already processed thousands of brake discs with a wide range of geometries and coating systems. EMAG currently produces prototypes of various designs and with different coating systems on four VLC 450 DG machines, optimizing the grinding technology and the tools used.
In particular, the energy input during laser metal deposition influences the geometry and material properties of the hard coating of brake discs and thus the relevant input variables for the grinding process. The EMAG Group offers manufacturing solutions for the entire machining chain after the brake disc casting process. The interactions between the individual manufacturing processes are specifically investigated on our own turning, laser and grinding machines.
The multi-functional VTC 100 GT turning and grinding machine:
The VTC 100 GT is a multi-functional turning and grinding machine for the efficient machining of gear and rotor shafts. It can be used to perform complex machining requirements such as hard turning and grinding in a single setup, which minimizes concentricity errors and significantly increases process efficiency. The optional Y-axis enables high-productivity scroll free turning. Driven tools for milling grooves make the machine concept universally applicable.
The G 160 gear generating grinding machine:
The G 160 is a high-performance gear generating grinding machine. With an unprecedented chip-to-chip time of less than 2 seconds and an innovative axis concept designed for the highest precision in batch production, the G 160 offers enormous productivity. Ideally suited for machining in the module range from 1.0 to 3.5 mm, it can machine workpieces with a diameter of up to 160 mm and a length of up to 300 mm, making it the ideal solution for efficient large-scale production.
The W 11 CNC universal cylindrical grinding machine:
The W 11 series complements EMAG's product lines for high-productivity series machining of large quantities on horizontal grinding machines with flexible workshop grinding machines with individually configurable equipment. The W 11 CNC from EMAG Weiss is a high-precision CNC cylindrical grinding machine that has been specially developed to meet the requirements of contract manufacture, medical technology and general mechanical engineering. It enables external and internal cylindrical grinding with maximum dimensional accuracy and cost-effectiveness, even for small batches or prototypes. The machine holds up to three grinding spindles on a swiveling B-axis. It can also be retooled quickly and easily, offering great flexibility for changing machining requirements. The dialog-based programming, which can be intuitively mastered even without in-depth programming knowledge is especially valuable. Easily grind workpieces with a diameter of 350 mm and a length of 2,000 mm.
The conventional cylindrical grinding machine W 11 EVO:
The W 11 EVO from EMAG Weiss is a conventional cylindrical grinding machine that combines traditional know-how with modern technology. It was specially developed for demanding tasks in tool and mold making or maintenance staff. The W 11 EVO combines manual precision with the possibility of using servo-electric axes for automated processes, making it a flexible and high-quality solution for specialized grinding tasks.
Referenti
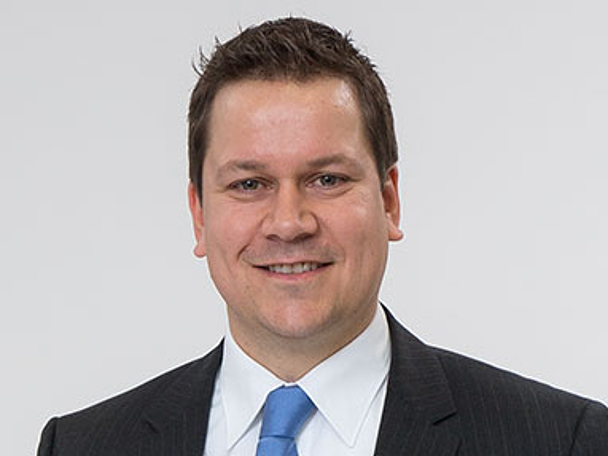
Oliver Hagenlocher
Zona
Press and Communication