Low cost production for high volumes of precise bevel gears
The VL 1 TWIN from EMAG is the perfect solution for the turning and drilling of bevel gears. This vertical turning center has two pick-up spindles that allow for the parallel machining of two bevel gears up to 75 mm in diameter. High production speeds and a small footprint ensure lower unit costs. This machine can also be loaded by a robot cell and swivel table, bringing the cycle time down to 4.5 seconds.
Complete Turning in a Single Clamping Operation
As a key element in differentials, bevel gears are mass-produced for passenger car manufacturing—many supply companies produce these components by the million every year. Bevel gear production starts with a forging process that gives the component its typical bevel gear teeth.
The subsequent turning operation differs from one manufacturer to another. In some cases, it starts with soft machining of taper faces, offsets, and end faces. After hardening comes the finish turning operation. Alternatively, the bevel gear may be hardened directly after forging, in which case it will only be turned once.
Be it soft or hard machining—the VL 1 TWIN turning center from EMAG is perfect for both processes and ensures lower costs with its simultaneous machining:
- Two pick-up spindles (9.9 kW/136 Nm at 40% duty cycle) machine two identical bevel gears simultaneously, at high speed (OP 10 – OP 10).
- All the turning steps are performed on the bevel gear in succession and with a single clamping operation, within a total cycle time of about 25 to 40
- seconds (depending on type and size of component).
- The two spindles load and unload the machining area in just five to six seconds.
- The turning center is able to drill into solid material, which is how the bevel gear’s center bore is produced.
- Diameter and length (X/Z directions) of the two workpieces can be readjusted independently of each other, since the headstocks can move autonomously.
Automation via a Robot Cell
In order to increase production, EMAG developers can combine the VL 1 TWIN with a high-performance robot cell and swivel table. This drops the cycle time to 4.5 seconds and makes individual process flows easily reproducible. Additional processes such as measuring, marking and cleaning can also be integrated into the same cycle time. Watch the video below to see this solution in action.
Linking Two Machines
It is also possible to load two VL 1 TWINs using either a robot cell or EMAG’s TrackMotion automation system (OP 10 – OP 10, OP 10 – OP 10). This allows both machines to be loaded and unloaded, quickly – a solution for four spindles that are both powerful and compact.
More information about VL 1 TWIN
Advantages Bevel gear
- Fast parallel machining of two identical bevel gears
- Linear drive in the X-axis for maximum dynamics
- Integrated automation system
- Simple interlinking of two machines with a robot
- Outstanding accessibility to the machining area and service units
- Small footprint
- Optional: measuring probe outside the machining area
- Wide range of components up to 75 millimeters (3 inches) in diameter
Low Investment Costs—Small Footprint
Another deciding factor is that EMAG integrates this high performance technology in an incredibly compact machine. The VL 1 TWIN has two spindles, and only requires about five square meters (54 square feet) of floor space. Even when two machines are installed together, connected by a robot, the footprint remains very small. Additionally, EMAG has considerably reduced the price per spindle through rigorous cost control. Both of these factors contribute to lower costs per piece for bevel gear production.
More information about VL 1 TWIN
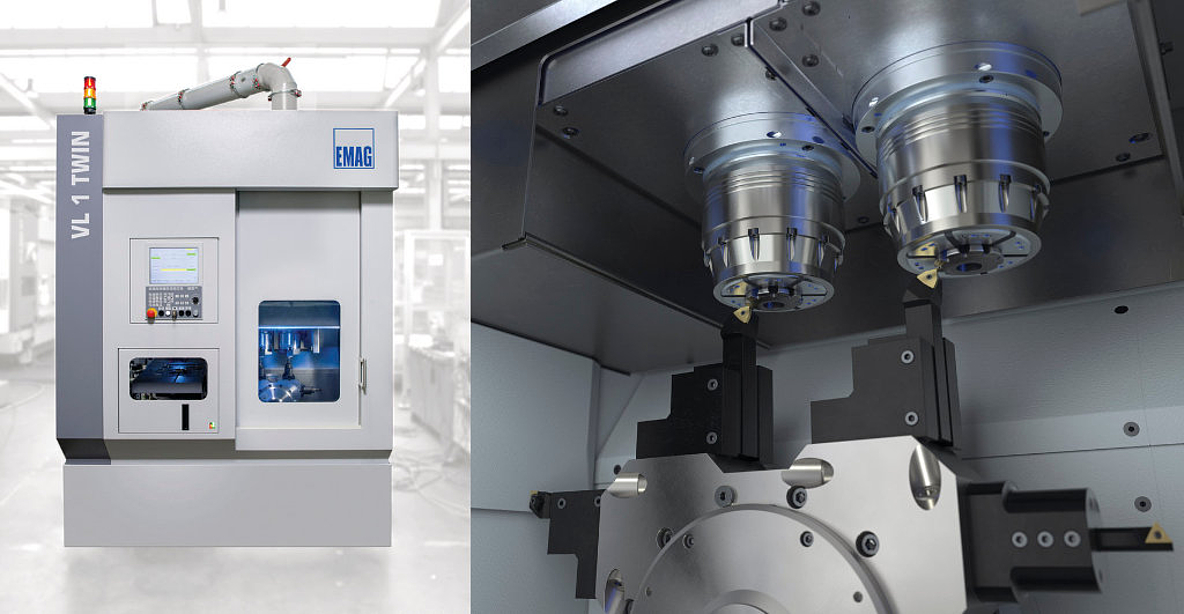
The VL 1 TWIN turning center only requires about 5 square meters (54 square feet) of floor space.
Technologies
Complex Manufacturing Systems from a Single Source thanks to a High Range of Technologies
Vertical turning is a machining process for metal components. EMAG was one of the first machine tool manufacturers to use the vertical turning process…