Laser Cleaning Technology
Laser cleaning is a fast and space-saving process that can replace conventional washing machines in many applications. One of its main strengths is its easy integration in manufacturing systems.
Laser Cleaning: Energy-Efficient, Reliable and Cost-Effective
The success of the laser as an alternative to conventional cleaning methods can be attributed to the numerous process advantages. For one, the process is very low cost, since no cleaning agents are used and no waste disposal is required. Secondly, the process is very precise and gentle on surfaces. Finally, the excellent cleaning results that can be achieved with a laser beam are ultimately the deciding factor. The laser evaporates oxides, dirt particles of all kinds and above all impurities from coolants, which are particularly difficult to remove, in a matter of seconds. The remaining surface is perfect for subsequent machining, e.g. laser welding.
Laser Cleaning in Detail
During laser cleaning, the high-energy laser beam evaporates impurities from surfaces.
Evaporation residues are extracted and neutralized with catalyzers or filter systems.
This process is extremely environmentally friendly and stands out because of its compact design and low noise emissions.
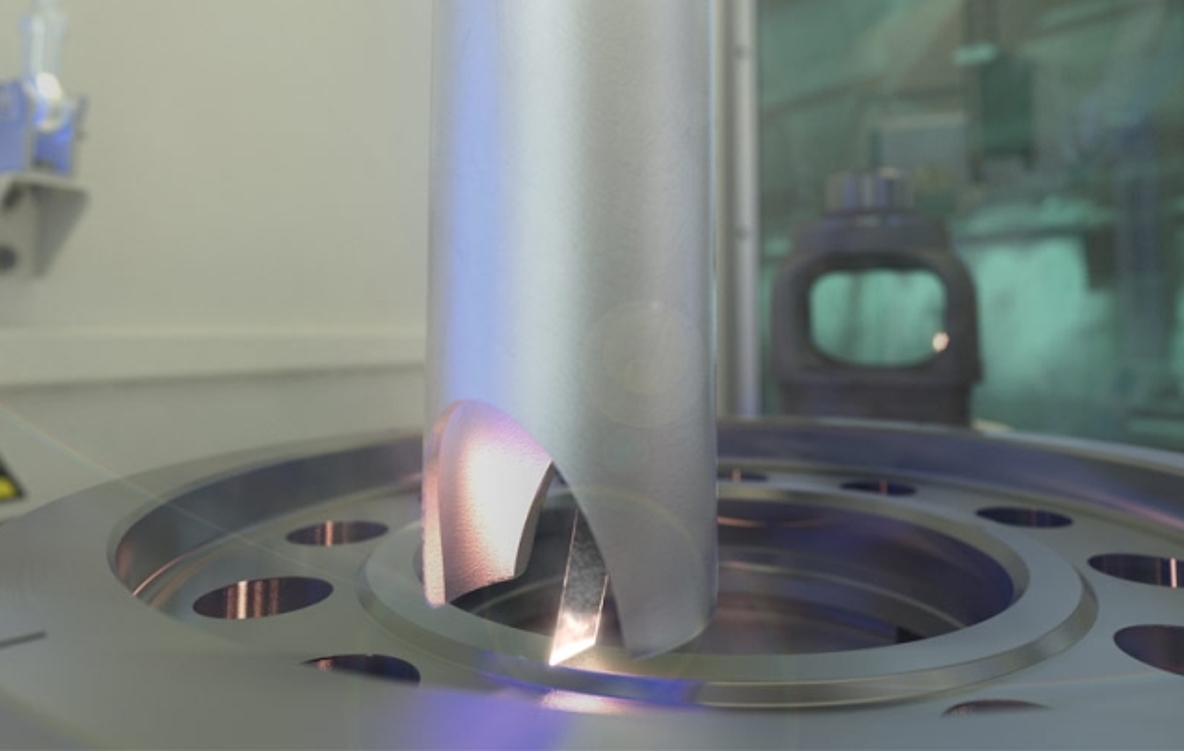
During laser cleaning, the high-energy laser beam evaporates impurities from surfaces. Evaporation residues are extracted and neutralized with catalyzers or filter systems.
Advantages Laser Cleaning
- Energy-efficient: lower energy consumption than conventional washing units
- Reliable: no additional contamination from cleaning agent residues; practically maintenance-free
- Fast: no parts traveling around the plant and lengthy non-productive times, since laser cleaning can be fully integrated into manufacturing systems
- Quality: all typical organic residues are removed
- Very cost-efficient
- Stable process: not dependent of water quality or its additives
Workpieces
The Right Manufacturing Solution for Every Workpiece
Machines for your requirements
(3) machines found