IoT retrofit from EMAG: Simply retrofit digitalization
Would you like to retrofit and gradually digitalize an ongoing production process? The first steps can be surprisingly easy - with the IoT retrofit from EMAG. The specialists simply retrofit IPC, sensory equipment and the like. The machine then uses data to provide information about its "health status," productivity and much more.
"Industry 4.0" is still the guiding principle of many production planners: the machines used are "networked," can be monitored from a central location and proactively inform about problems.
Retrofitting for Fanuc and Siemens controls
EMAG can also integrate central IoT technology as part of a retrofit. With EDNA, EMAG customers have a complete IoT ecosystem at their disposal, including the EDNA Cortex software, connecting MES / BDE / MDE via e.g. OPC-UA, MQTT, REST:API and various software applications. Whether these solutions can be used on an older machine depends on its control system. (Fanuc: starting with 31iB controller and Siemens: starting with 840 DSL).
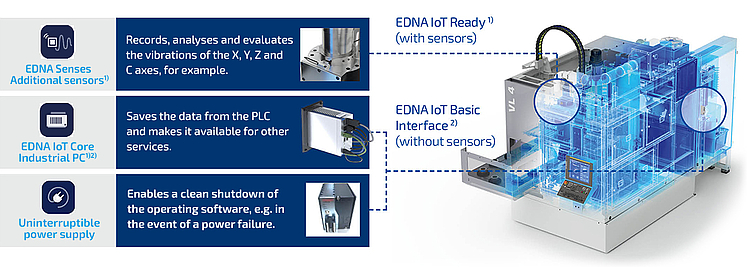
"Lean" hardware as the basis
The conversion can then begin. The used machine gets:
- a powerful industrial PC for processing the data generated,
- depending on the machine type, certain sensory equipment that measures vibrations,
- as well as additional hardware, an uninterruptible power supply and the router.
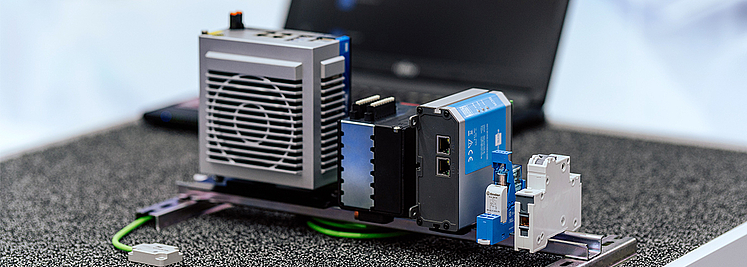
Monitor the "health" and the “performance” of the machine
Using this technology, customers can access a wide range of applications that can be individualized depending on the production task. One outstanding example would be the EDNA Health Check, which illustrates the "health trend" of the machine and proactively warns of problems. Equally interesting is the permanently recorded EDNA standard signal list, which can be used to analyze processes (e.g., tool changes, lack of availability) to improve OEE. Machine-dependent visualization of key information is also available.
Technical Hotline
Our technical hotline records all inquiries and gives you technical assistance
+49 7162 17-4300
service.salach@emag.com