Automated Production of Planetary Gears
A planetary gear is a component of a planetary gearbox, also known as a planetary gearset. The name "planetary gears" is derived from the fact that, similar to the planets in the solar system, the planetary gears revolve around a central wheel, often referred to as the sun wheel. To be more precise, the planetary gears revolve around the fixed axle on circular paths. Accordingly, a distinction is made between the central or sun gears mounted on the fixed axes and the orbital or planetary gears mounted on the revolving axes.
The production of planetary gears
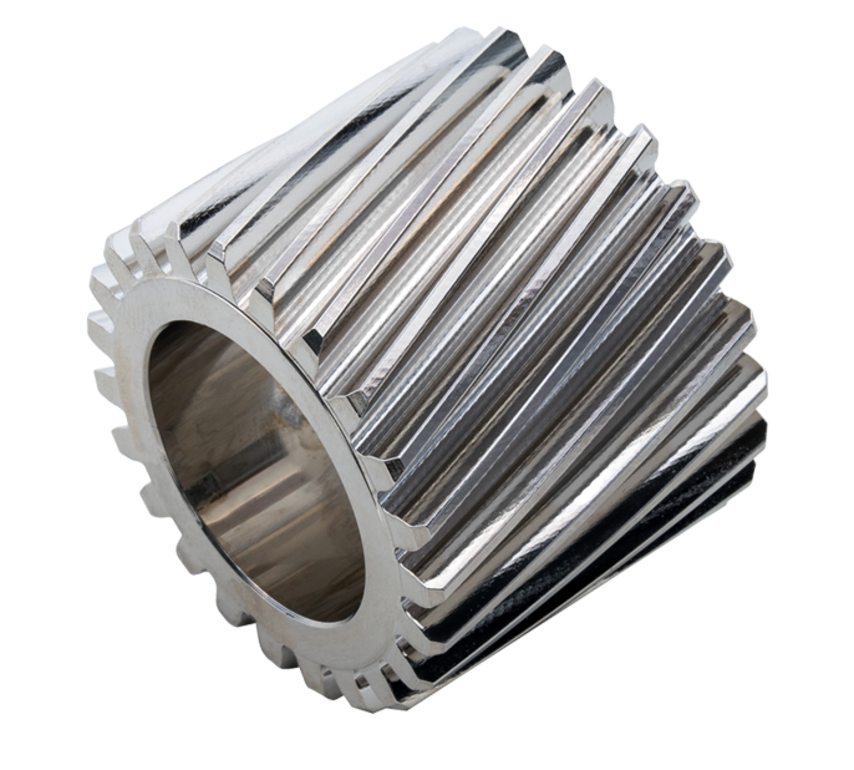
Gearboxes are used to transmit torque efficiently and to adjust motor speeds and torques between the input and output. Planetary gearboxes are used to increase torque, particularly in the automotive industry – for example in transfer cases for all-wheel drives and, of course, in automatic transmissions. Planetary gearboxes are also used in trucks, buses, construction machinery and agricultural machinery to enable the transmission ratio to be reduced (reduction gearbox).
Planetary gears and, therefore, planetary gears are therefore manufactured in very large quantities.

The process chain at EMAG
Traditionally, the process chain for manufacturing a planetary gears in the automotive sector consists of four steps:
In the first process step, the gear blank is turned. This is followed by rough-machining of the tooth profiles, usually as a dry hobbing process. The planetary gears are then hardened, followed by hard finishing. The technology used for hard finishing depends on the required quality of the finished part. A quality class 6 can easily be achieved on a gear hobbing machine using skiving. In the field of electromobility, however, a smoother running of the transmission components and, thus, a higher quality of the tooth flanks of the planetary gears is often required. In this case, the planetary gears must be machined by gear generating grinding.

Turning of the raw-parts
With its comprehensive machine and technology portfolio, EMAG is able to cover almost the entire process chain for the production of planetary gears and offer them as a turnkey manufacturing system.
The manufacturing process begins with the turning of the OP 10 / OP 20 raw-parts on vertical turning machines from the VL or VSC series. These machines are characterized by precision and efficiency and ensure optimal preparation of the workpieces for the subsequent processing steps.

Rough-machining the tooth profiles
The gear hobbing machines from EMAG Koepfer, such as the K 160, are then used to rough-machine the tooth profiles. These machines offer high-performance and precision during rough-machining, which is crucial for the quality of the planetary gears that are produced later.
After rough-machining, the planetary gears are case-hardened to increase their strength and wear resistance. This hardening process is a crucial step in ensuring the longevity and reliability of the planetary gears.
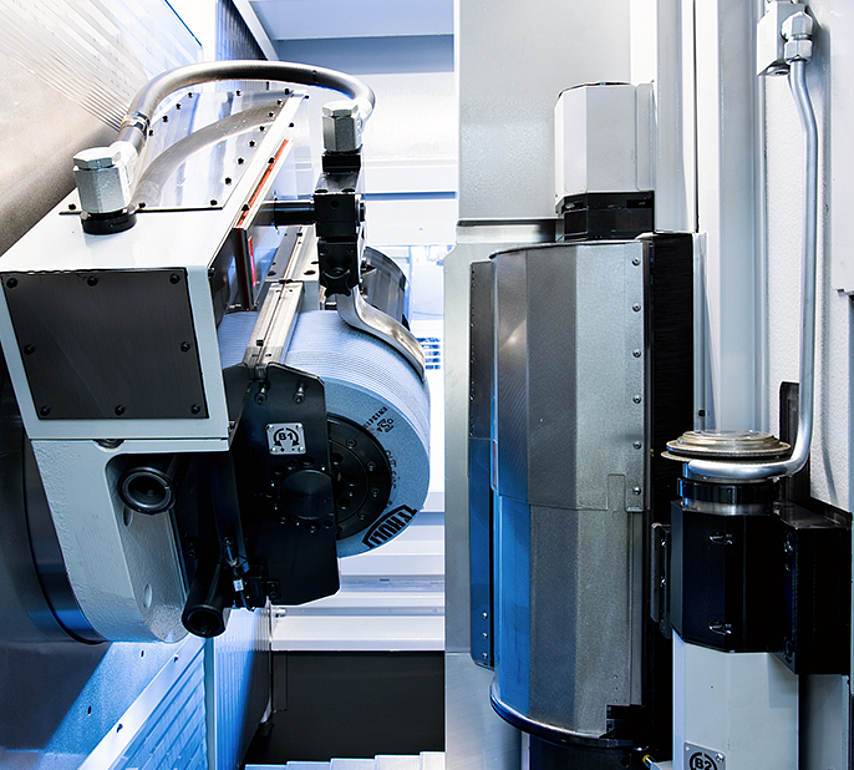
The final hard finishing
The final hard finishing can either be carried out on the K 160 by skiving or on a G 160 gear generating grinding machine from EMAG SU. Both machines offer high-precision machining options to bring the planetary gears to the required dimensional and surface tolerances.
This comprehensive and precision manufacturing process enables EMAG to guarantee consistently high quality and efficiency in planetary gear production, ensuring the performance and reliability of the manufactured components.
Watch the gear cutting process in this video!
(3) machines trouvées
Technologies
Complex Manufacturing Systems from a Single Source thanks to a High Range of Technologies
During the machining of the tooth flanks of shafts and gears by means of generating grinding or gear grinding, it is important to achieve…
Flexible, highly productive, highly accurate - as a continuous gear production process, hobbing is indispensable in many industries, as it allows any…
Vertical turning is a machining process for metal components. EMAG was one of the first machine tool manufacturers to use the vertical turning process…
Blog
In our blog read an interview with expert Jörg Lohmann.