15/06/2020 - Oliver Hagenlocher - Presse
VL 1 TWIN par EMAG : Réduire massivement les coûts par pièce des roues coniques
Les roues coniques des voitures sont des composants de masse. Les équipementiers produisent ces roues dentées au cœur des engrenages différentiels à des millions d’exemplaires – ça n’a rien de surprenant : chacun de ces différentiels en compte quatre. De plus, la part de véhicules à transmission intégrale (y compris ceux à deux différentiels) ne cesse de progresser. Il s’ensuit que les quantités de roues coniques sont elles aussi en augmentation et c’est pourquoi les processus de production de ce composant entre en ligne de mire chez de nombreux équipementiers. Ils recherchent des solutions de construction mécanique qui garantissent des coûts par pièce considérablement réduits et une qualité élevée constante. Avec son tour pick-up à double broche VL 1 TWIN, EMAG a justement conçu une telle solution : il permet d’usiner simultanément deux roues coniques identiques à une cadence élevée dans un espace de travail unique. De plus, cette machine peut aisément être chargée au moyen d’une cellule robotisée et d’une table pivotante, ce qui permet de réduire le temps de cycle à une durée minimale de 4,5 secondes.
Les véhicules à transmission intégrale gagnent rapidement du terrain. En Allemagne, par exemple, leur part représente désormais environ 20 pour cent pour les nouvelles immatriculations. Dans d’autres pays, comme la Suède ou la Suisse, cette part est encore plus importante. Cette évolution s’accompagne d’une forte croissance des chiffres de production de roues coniques, qui subissent la pression croissante des coûts, comme tous les autres composants de masse dans le secteur automobile. Leur processus de production commence généralement par un processus de forgeage exigeant, qui confère au composant sa denture de roue conique caractéristique. Celui-ci est suivi de divers processus de tournage : la surface conique par rapport à la denture, un léger épaulement sur la surface conique, l’alésage intérieur et une surface plane sont réalisés de cette manière. Que ces processus s’effectuent directement dans le cadre d’un usinage dur final ou que chaque composant soit d’abord soumis à un tournage doux avant le tournage dur dépend de la solution de production spécifique au constructeur. « Dans tous les cas, il s’agit de gérer de nombreuses quantités de façon rentable, rapide et exempte de défaut. » explique Daniele Loporchio, responsable technico-commercial chez EMAG. « C’est exactement pour cela que nous avons conçu le VL 1 TWIN. Cette machine convient parfaitement pour l'usinage doux et dur d’une large gamme de roues coniques qui ont un diamètre maximum de 75 millimètres. »
Un temps de cycle d’à peine 20 secondes
Le principe élémentaire de ce tour pick-up joue un rôle décisif. Il est équipé de deux broches pick-up (9,9 kW/136 Nm avec un facteur de marche de 40 %), à l’aide desquelles l’usinage s’effectue toujours simultanément sur deux roues coniques identiques à une cadence élevée (OP 10 – OP 10) : les deux broches chargent et déchargent l’espace de travail en à peine cinq à six secondes. Les étapes d’usinage décrites ci-dessus sont alors réalisées successivement et en un seul serrage, en un temps de cycle total d’environ 25 à 40 secondes (en fonction de la taille et du type de composant). Le temps moyen de copeau à copeau est ici d’à peine six secondes. Une solution de serrage spéciale reproduit en négatif la denture de la pièce qu'elle maintient dans une position stable. De plus, le VL 1 TWIN permet d’effectuer un « perçage en pleine matière ». C’est d’ailleurs ainsi qu’est réalisé l’alésage central de la roue conique.
Toute l’approche de cette machine consiste, d’une part, à produire des quantités élevées dans des délais courts. D’autre part, ses concepteurs ont considérablement réduit le prix par broche grâce à une maîtrise rigoureuse des coûts, ce qui contribue tout autant aux faibles coûts unitaires.
La qualité des composants également en point de mire
Toute une série de caractéristiques d’équipement propres à EMAG assure la qualité des composants et la fiabilité des processus. Ainsi, le VL 1 TWIN dispose d’un banc de machine en Mineralit®, qui réduit sensiblement les vibrations lors du processus de tournage. Une durée de vie prolongée des outils (et ainsi des coûts d’outillage en baisse) en sont une retombée directe. Les corps de poupée peuvent se déplacer de manière autonome. Le diamètre et la longueur (en sens X/Z) des deux composants peuvent ainsi être corrigés de manière indépendante lorsque des écarts se produisent – par exemple, à la suite d’un changement des plaquettes de coupe réversibles. L’entraînement linéaire sans usure dans l’axe X, comprenant des systèmes de mesure directe, constitue un autre facteur essentiel. Il dispose d’une accélération de 8 m/s2 avec une précision élevée constante. Les guidages à rouleaux sur tous les axes linéaires garantissent une précision accrue.
Chargement du VL 1 TWIN par robot
Concrètement, EMAG conçoit le dispositif lié à la production de la roue conique, y compris l’automation et l’enchaînement, d’une manière très souple et qui s’adapte à la mission du client. L’automation pick-up intégrée, responsable du flux de pièces au sein de la machine, constitue le fondement technique du flux de pièces. En vue d’accroître le volume de production, les concepteurs d’EMAG peuvent associer le VL 1 TWIN à une cellule robotisée performante et une table pivotante. Dans ce cas, la pince est adaptée avec précision à la forme du composant. Des conteneurs de composants prépositionnés facilitent le transport ainsi que le chargement et le déchargement. D’une part, le temps de cycle peut ainsi être réduit à une durée minimale de 4,5 secondes et les différentes gammes d’usinage peuvent être aisément reproduites. D’autre part, il est possible d’intégrer simultanément d’autres processus, tels que la mesure, le marquage et le nettoyage, dans le même temps de cycle.
Deux VL 1 TWIN peuvent en outre être chargés au moyen la cellule robotisée citée plus haut ou alors avec le système d'automation TrackMotion d’EMAG (OP 10 – OP 10, OP 10 – OP 10). Pour ce dernier, le dispositif appelé TransLift (un véhicule à inversion de course muni d’une pince électrique) prélève des pièces brutes sur le tapis d’alimentation et les transporte vers les machines. Les deux machines sont ainsi chargées et déchargées en rapide succession – une solution à la fois performante et très compacte pour quatre broches.
Tout aussi indiqué pour les entraînements électriques
Des coûts d’investissement et de production réduits, des temps de cycle courts et une grande fiabilité de processus – les constructeurs de machines se considèrent parfaitement équipés pour la production de roues coniques. « Le différentiel demeure pertinent pour tout type d’entraînement, qu’il s’agisse d’un moteur à combustion classique ou d’un entraînement entièrement électrique. Ceux qui modernisent maintenant leur production et se préparent à un nombre croissant de pièces ont tout à fait intérêt à s’intéresser de plus près à cette technologie. » souligne Loporchio en guise de conclusion. « Nous sommes convaincus que le VL 1 TWIN constitue une solution idéale pour de nombreux producteurs de roues coniques. »
Images
Téléchargements
Interlocuteurs
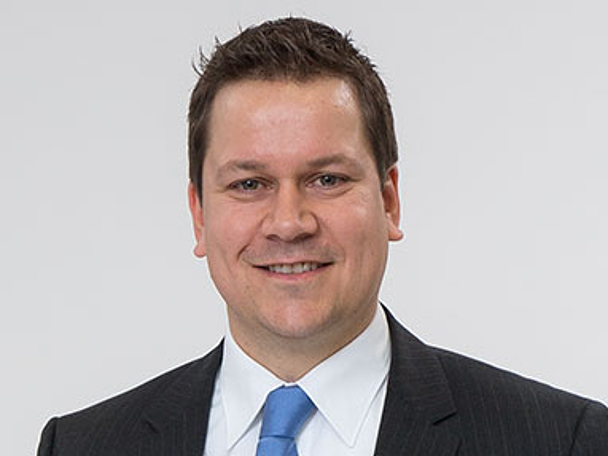
Oliver Hagenlocher
Zone
Press and Communication