02/12/2019 - Oliver Hagenlocher - Presse
Système de production EMAG: Un arbre de rotor léger fabriqué à partir de systèmes de production globaux
De nombreuses études pronostiquent une croissance fulgurante de l’électromobilité. Les chiffres d’affaires actuels laissent également présager le changement : Selon Center of Automotive Management, les ventes de voitures électriques ont progressé de manière importante en Chine et aux États-Unis l’année dernière. En Allemagne, les parts de marché ont été doublées à un faible niveau. Le génie mécanique occupe un rôle essentiel dans cette évolution : Il doit développer la technique de production permettant de fabriquer de manière fiable et précise les composants essentiels de l’entraînement électrique - à des volumes beaucoup plus importants que par le passé. L’arbre de rotor en est un tel composant : Il doit transmettre de manière précise et stable le couple élevé du moteur électrique. En même temps, il s’agit de trouver la combinaison la plus légère possible de l’ensemble de tôles de rotor et de l’arbre de rotor, afin d’augmenter l’autonomie de la voiture électrique. Mais comment est-il possible de fabriquer un arbre de rotor complexe de manière efficace ? Les constructeurs de machines EMAG développent différentes solutions à cet effet. Celles-ci seront parfaitement adaptées à la géométrie des pièces et à la planification de production - du système de production parfaitement automatisé jusqu’à la machine autonome spécifiquement adaptée aux besoins du client.
Depuis des dizaines d’années, une attention particulière est apportée à la construction légère dans l’industrie automobile : Chaque composant du pignon de transmission en passant par les arbres d’entraînement jusqu’aux différents boîtiers doit devenir plus léger et plus petit, afin de réduire la consommation des voitures particulières. Il est intéressant de constater que ce sujet a presque plus d’importance pour les voitures électriques, car un poids moindre permet de parcourir des distances plus longues sans recharger la batterie. Ainsi, le thème de "l’autonomie" reste pour l’instant l’une des missions essentielles du développement dans l’électromobilité. Dans ce contexte, les arbres de moteurs électriques massifs et ainsi lourds, pourvus d’ensembles de tôles de rotors relativement volumineux, ne conviennent pas. EMAG montre actuellement de quelle manière il est possible de fabriquer des arbres de rotors d’un poids optimisé (et par conséquent des moteurs électriques d’un poids optimisé) en grande série : Les spécialistes des systèmes de production globaux ont conçu une ligne permettant d’enchaîner directement les opérations d’usinage avant le traitement thermique, de durcissement et d’usinage après le traitement thermique d’un arbre creux et ainsi léger. "Dans l’ensemble, la production d’une telle pièce est dans tous les cas une mission idéale pour EMAG", explique Ulrich Heiermann, Manager Technical Application chez EMAG. "Nous disposons du savoir-faire nécessaire pour ces applications comprenant les opérations de tournage, perçage, fraisage, durcissement et rectification. En outre, nous développons les systèmes d’automatisation associés depuis des dizaines d’années. Par conséquent, l’intégralité de la ligne et le développement du processus sont gérés par le même interlocuteur. De l’autre côté, nous fournissons des solutions spécifiques adaptées aux besoins du client pour des processus partiels essentiels comme le tournage ou la rectification avec, par exemple, un chargement manuel. Lors de l’installation de machines autonomes, ces solutions peuvent constituer le départ d’une transformation ultérieure vers une ligne automatique complète. Dans les deux cas, des solutions sont utilisées issues d’un système modulable d’une grande souplesse. Nous configurons des machines sur mesure à partir de différents modules technologiques. Nous sommes préparés à chaque demande."
Un arbre assemblé doté d’importants avantages
L’arbre de rotor "assemblé" est actuellement un exemple impressionnant pour cette approche souple : Selon la demande, EMAG devait développer un système de production à plusieurs niveaux rassemblant l’usinage avant le traitement thermique, le soudage laser, le durcissement et l’usinage après le traitement thermique. En outre, l’arbre est assemblé à partir de deux embouts différents pendant le processus - un principe de base connu du domaine des arbres à cames assemblés, par exemple. Il est ainsi possible de diviser le processus en processus partiels courts et parfois parallèles. En outre, l’approche offre souvent des libertés plus importantes aux développeurs des pièces. La fabrication finale de cet arbre s’effectue de manière parfaitement cadencée dans le système EMAG. Au cours des deux premières opérations (10 et 20), les deux pièces brutes différentes sont usinées à l'intérieur et à l’extérieur en créant également la géométrie intérieure creuse. Quatre machines EMAG Pick-Up de type VL 4 sont utilisées. À la suite d’un processus de nettoyage (OP 30), les embouts sont assemblés par soudage laser grâce à une EMAG ELC 250 (OP 40) – un procédé extrêmement rapide et fiable. L’énergie concentrée du faisceau laser peut être dosée avec précision et permet ainsi une vitesse élevée de soudage et des déformations minimales au niveau de la pièce soudée. L’opération suivante comprend le durcissement ultraprécis des logements de paliers en quelques secondes dans la machine de durcissement par induction MIND 750 d’EMAG eldec (OP 50). L’usinage après le traitement thermique de l’arbre commence par le tournage extérieur dans la machine EMAG Pick-Up VT 4-4 (OP 60) et le tournage intérieur dans la gamme modulable VL (OP 70). Les opérations OP 80 et 90 comprennent le taillage de l’arbre ainsi que le tournage de finition extérieur de différents épaulements. Le processus de rectification sur une machine verticale de rectification d’arbres de la gamme VTC (OP 100) assure enfin l’usinage de finition avec des tolérances serrées et des exigences élevées en matière de qualité de surface.
L’arbre est ensuite préparé pour l’assemblage avec l’ensemble de tôles associé. Quant à la technologie d’automatisation assurant le transport entre les machines, EMAG s’adapte aux attentes du client. Les systèmes utilisés sont par exemple des portiques de ligne, des cellules d’empilage, des convoyeurs à accumulation ou le système maison EMAG TrackMotion - dans tous les cas, le système bénéficie de l’homogénéité des machines utilisées avec leurs interfaces optimisées et notamment de la solution complète pour le client avec un système global et EMAG comme seul interlocuteur nécessaire pendant l’étude, la mise en œuvre et pour toute demande de SAV. En outre, la technologie EMAG Pick-up assure une certaine allure dans le processus : L’arbre (ou les deux pièces détachées au début) est transporté dans la zone de travail et en évacué par la broche mobile de la pièce à usiner. Le processus vertical de tournage et de fraisage s’effectue ensuite avec des vitesses de coupe élevées et une évacuation des copeaux optimisée.
Une solution rapide offerte par un seul interlocuteur
Un arbre de rotor fini quitte cette ligne environ toutes les 45 secondes. Les temps secondaires indésirables pendant lesquels la machine est à l’arrêt sont réduits à un minimum. "La qualité d’un tel processus de production se décide déjà au début de son étude. EMAG apporte ici tout son savoir - concernant les différentes applications d’outils, la conception de machines-outils à fonctions multiples, leur commande et leur interconnexion. L’objectif est toujours de produire une pièce optimale dans le temps de cycle et la qualité demandés par le client. C’est finalement le client qui choisit entre une ligne globale avec un volume annuel élevé et, par exemple, une solution autonome à chargement manuel avec des volumes plus faibles, mais avec plus de souplesse", explique Ulrich Heiermann.
More information about Assembled Rotor Shafts for Weight-Optimized Electric Motors you will find here...
Images
Téléchargements
Interlocuteurs
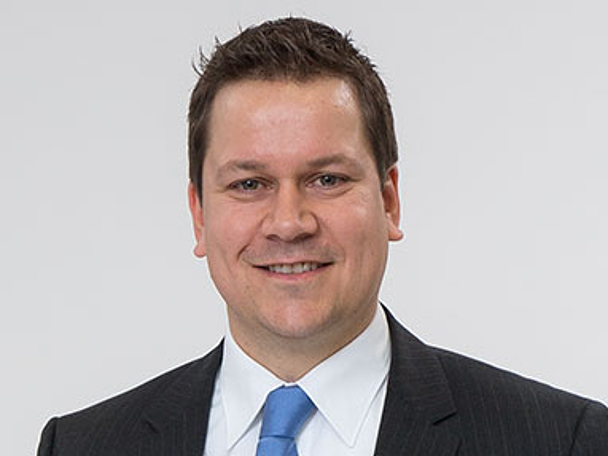
Oliver Hagenlocher
Zone
Press and Communication