13/09/2021 - Oliver Hagenlocher - Press
EMO 2021 in Milan: EMAG shows highly flexible production solutions for electromobility
Highly flexible and at the same time productive grinding and turning processes for electromobility and co. - this is the claim EMAG is making at this year's EMO in Milan from October 4 to 9. Among other things, the focus will be on the G 250 machine from EMAG SU (formerly: Samputensili), based near Bologna. With this solution, axle drive gears, gear wheels and shafts with a maximum length of 550 millimeters can be produced cost-effectively by generating or profile grinding. If required, very small profile grinding wheels or generating grinding worms can also be used, which ensures maximum flexibility and productivity in production. What other solutions will be the focus of the EMO presentation, where EMAG SU's machines will be on display on an EMAG stand for the first time since the acquisition of Samputensili?
Images
Whether electric drive, hybrid motor or conventional drive - grinding machining is currently moving into the focus of production planners. On the one hand, they need new solutions for perfect component surfaces that guarantee the required smooth running at very high torques and speeds. On the other hand, the flexibility of the machines is important. They should be able to efficiently handle very different production tasks with short set-up times, which is not easy to implement, especially in the grinding sector. This makes the concept of the G 250 machine from EMAG SU for generating and profile grinding of gear components with a diameter of up to 250 millimeters and a length of 550 millimeters all the more impressive. This technology scores on various levels: For example, the machine has two table spindles to minimize chip-to-chip times during the manufacturing process. Here, generating grinding and profile grinding each take place on the main grinding spindle, so that there is no undesired thermal run, as is the case with attachment spindles. In addition, the machine can be converted to the other process in just a few minutes. "Input is via user-friendly dialog software, which makes setting up the machine simple and clear. Set-up times are minimal," emphasizes Francesco Zambon, Managing Director of EMAG SU Milan.
High speed gear machining
Another interesting feature of the G 250, which EMAG will be demonstrating live at the EMO: Grinding of workpieces with interfering contours is also possible thanks to the use of small-diameter (160 millimeter) roller screws on the main spindle. Centering takes place in the loading position during machining. The integrated dressing unit provides additional process reliability. In the G 250 HS variant, the machine also has a high-speed grinding head that makes 20,000 revolutions per minute possible when using a small grinding wheel. "This machine is both highly flexible and highly productive, which is normally difficult to combine in the grinding sector," says Zambon. "With this in mind, it is, among other things, an ideal solution for gear cutting tasks in electromobility and gear motors, where very small parts are often used.“
Modular turning machines ensure high performance
Overall, the messages of "flexibility" and "productivity" characterize EMAG's entire presence at EMO. The machine builders will also exhibit their VL 2 and VL 8 lathes and the high-performance WPG 7 cylindrical grinding machine. With their integrated automation, the modular VL lathes stand for maximum performance and low unit costs in the smallest of spaces. The basis for this is high-quality components: The VL machine base body is made of the damping polymer concrete MINERALIT®, the automation by means of a pick-up work spindle moves very quickly in the X and Z axes and the tool turret also guarantees short swivel times. Here, the VL 2 is suitable for machining small workpieces with a maximum diameter of 100 millimetres and the VL 8 accommodates workpieces up to a diameter of 400 millimeters. Both lathes are ideally prepared for use in line production. They can be interlinked with simple automation components such as conveyors, turners and transfer units - for example with downstream grinding processes based on EMAG SU technology.
Focus on integrated production solutions
"With our presentation of grinding and turning technology at EMO, we are making it clear that we are one of the few manufacturers whose production systems cover the entire process chain from soft to hard machining. The principle of 'One Face to the Customer' always applies: an experienced contact person at EMAG discusses the requirements with the customer. EMAG takes care of the complete manufacturing solution and defines its specifications. The customer's planning effort is massively reduced," emphasizes Zambon. "Of course, we also bring this know-how to bear when establishing new production solutions for electromobility." It is important to note that with the EDNA system, EMAG has a modular software ecosystem consisting of interconnected software and machine components, with which the establishment of Industry 4.0. applications succeed particularly quickly. Whether customers want to visualize their production figures, optimize shifts or avoid machine failures through predictive maintenance, EDNA provides a suitable solution for these problems. "In the end, the customer has a perfect production system that sets new benchmarks regarding cycle times, but at the same time has a high level of stability and process reliability. All machining processes from turning to grinding run in perfect sequence. We want to increasingly introduce these enormous advantages to the market. EMO is an ideal platform for this," concludes Zambon.
You can find everything about the EMAG Group's trade show appearance in Milan in Hall 4 at Booth A32 / B17 in the current issue of EMAG News 32: https://www.emag.com/press/customer-magazine/emag-news-32.html
Téléchargements
Interlocuteurs
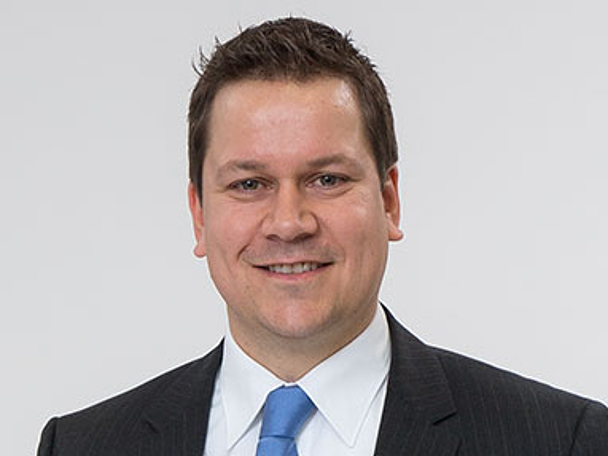
Oliver Hagenlocher
Zone
Press and Communication