06/08/2019 - Oliver Hagenlocher - Presse
EMO 2019 – Solutions de ligne avec la VL 1 TWIN: Réduire considérablement les coûts unitaires des roues planétaires ou coniques
Pression sur les coûts, exigences de qualité strictes, sans oublier les énormes quantités de pièces – la construction de boîtes de vitesses pour VP voit les extrêmes s’affronter. Les volumes de production doivent même augmenter au cours des prochaines années. Les auteurs des derniers « Shell Passenger Car Scenarios » estiment que le parc mondial des voitures particulières va plus que doubler, pour atteindre 2,5 milliards de véhicules d'ici 2050. Il est alors quasi inévitable que la première préoccupation des planificateurs de la production soit le « coût par pièce » : comment optimiser encore la production des composants de boîtes de vitesses typiques de type roues planétaires ou coniques ? Le groupe EMAG apporte une réponse concrète à cette question avec le développement du tour pick-up à double broche VL 1 TWIN. Le tour usine simultanément deux composants identiques dans un seul espace de travail. Cette base technique ouvre de vastes possibilités : lorsque deux machines sont reliées en ligne, la roue planétaire peut être usinée des deux côtés - en réduisant les temps de cycle d'autant. À quoi ressemble exactement la solution de ligne pour roues planétaires ou coniques ?
Images
Souvent, les sites de production fabriquent jusqu'à un million de roues planétaires par an, nécessité qui s'explique par l'utilisation de ce composant dans les boîtes automatiques séquentielles. En effet, le réducteur planétaire associé se compose généralement de quatre trains planétaires, chacun d'entre eux comportant trois roues planétaires et une roue solaire. Le total de 16 roues dentées est ainsi vite atteint. Par ailleurs, il est intéressant de constater que la boîte automatique séquentielle est en passe de gagner du terrain. D’un côté, elle représente une solution confortable, compacte et robuste. De l'autre, certains fabricants misent sur cette technologie pour les entraînements hybrides de dernière génération. « Voilà ce qui explique le développement de la VL 1 TWIN. La réduction des coûts de fabrication des roues planétaires et coniques était une priorité absolue », explique Björn Svatek, Sales & Marketing Director Modular Solutions chez EMAG. « C'est pourquoi nous utilisons cette machine à deux broches pour usiner simultanément deux pièces identiques dans un même espace de travail. Nous obtenons ainsi des quantités de production élevées en un temps record. Nous avons également considérablement réduit le prix par broche grâce au contrôle systématique des coûts. Ce qui contribue à diminuer le coût unitaire ».
Roue planétaire : deux pièces finies toutes les 20 secondes
Comment envisager une solution de ligne VL-1 TWIN pour l'usinage avant traitement des roues planétaires ? En principe, le processus se déroule sur deux machines enchainées par un système d'automation TrackMotion. Le TransLift correspondant (véhicule à inversion de course muni d’une pince électrique) prélève simultanément deux pièces brutes sur le tapis d'alimentation et les transporte vers la première machine. C'est là que les deux broches pick-up de la VL 1 TWIN prennent le relais et introduisent les composants dans l’espace de travail. Le tournage du premier côté des diamètres intérieur et extérieur (OP 10 - OP 10) est alors effectué. Le diamètre et la longueur (en sens X/Z) des deux composants peuvent être corrigés indépendamment l'un de l'autre car les corps de poupée se déplacent en toute autonomie. Ce point est crucial après un changement d'outil car il est indispensable de compenser les écarts (p. ex. après le changement des plaquettes). Après l'extraction hors de la salle des machines, le TransLift reprend le relais et fait pivoter les deux composants semi-finis de 180 degrés pour les transporter sur l'autre VL 1 TWIN. C'est alors que commence le surfaçage du second côté du diamètre extérieur (OP 20 - OP 20). Finalement, la pièce usinée atterrit via TrackMotion sur le tapis de stockage, qui peut accueillir jusqu'à 400 pièces finies sur les unités de stockage intégrées. Le temps de cycle du processus complet est d’environ 20 secondes pour deux composants. Le temps moyen copeau à copeau est d'à peine 5 secondes. De nombreux détails techniques de l'équipement permettent d'obtenir cette vitesse remarquable : par exemple, les deux broches du poste pick-up ont des valeurs d'entraînement élevées de 9,9 kW et 136 Nm avec un facteur de marche de 40%. En même temps, l'entraînement linéaire exempt d'usure de l'axe X (combiné avec des systèmes de mesure directe de la course) présente une accélération élevée de 8 m/s2- donc une précision élevée en continu. Cela signifie que les ajustements H6 souvent nécessaires de l'alésage principal sont réalisables en toute fiabilité.
Roue conique : forage, dégrossissage et finition sur une même machine
En raison de la pression croissante qui s'exerce sur les coûts de production des roues coniques, il est indispensable d'optimiser tous les processus. Et le forgeage présente des atouts indéniables : les roues coniques quittent en général la forge avec une denture prête à l'emploi. Il ne reste alors plus qu’à effectuer une opération de tournage en un serrage. Avec la VL 1 TWIN, EMAG présente la solution optimale d'usinage parallèle avant traitement de deux ébauches de roues coniques (OP 10 - OP 10). Quatre étapes d'usinage se succèdent dans la machine et le temps de cycle ne dépasse pas 25 secondes environ : TrackMotion ou par broche pick-up assurent l'alimentation, puis l'alésage central de la pièce est réalisé « dans la masse », suivi par le dégrossissage de la calotte. La finition de l'alésage et de la calotte constituent les troisième et quatrième étapes de l'usinage. Une solution de serrage spéciale reproduit à la négative la denture de la pièce qu'elle maintient dans une position stable. Pendant l'opération de forage, le bâti machine en béton polymère Mineralit® joue un rôle prépondérant car il réduit les vibrations et assure ainsi une précision supplémentaire. Un système disponible en option mesure les pièces entre l'espace de travail et les postes pick-up, ce qui améliore la sécurité du processus. En principe, il est également possible de relier deux VL 1 TWIN avec un seul système TrackMotion et de réaliser le même processus dans les machines (OP 10 - OP 10, OP 10 - OP 10). Il est essentiel ici que la pince TrackMotion se déplace à une vitesse pouvant atteindre 150 mètres par minute pour assurer l'alimentation et l'évacuation des machines TWIN fonctionnant en parallèle.
Solution parfaite de fabrication des boîtes de vitesses
Dans l'ensemble, la méthode TWIN permet des gains de productivité importants pour toute une série de composants allant des pièces de cames aux brides, en passant par les bagues de roulement. Selon les besoins du client, des lignes de fabrication à technologie multiple sont élaborées, comme par exemple des machines de fraisage par développante et d’ébavurage EMAG. « Nous sommes convaincus que la VL 1 TWIN est la solution parfaite qui permet d'assurer des quantités en augmentation constante et de tenir tête à une concurrence de plus en plus sévère dans la fabrication des boîtes de vitesses », déclare Björn Svatek. « Les utilisateurs bénéficient de coûts unitaires en baisse, de temps de cycle courts et d'une grande fiabilité des processus. Nous souhaitons améliorer la part de marché de ces atouts».
La VL 1 TWIN en direct à l'EMO 2019
Interlocuteurs
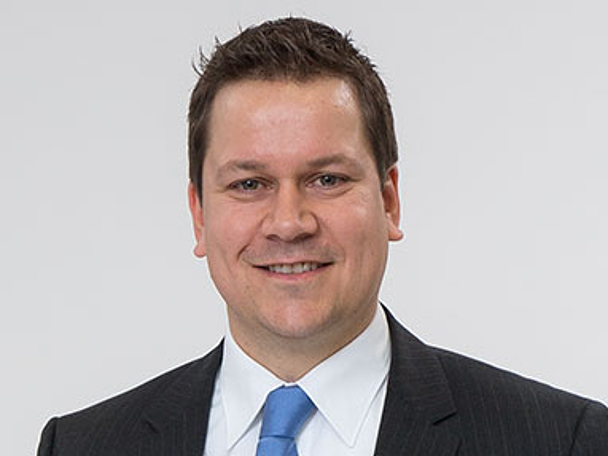
Oliver Hagenlocher
Zone
Press and Communication