15/02/2023 - Oliver Hagenlocher - Presse
TrackMotion, robots & Co : Comment les fournisseurs et les sous-traitants profitent des solutions d'automatisation simplifiées
Le recours à l'automatisation et à la robotique dans l'industrie de production est motivé par de multiples raisons, allant du besoin de compenser le manque de main-d'œuvre et de simplifier les processus de production à la réduction des coûts unitaires. Les solutions de dernière génération permettent de tirer parti comme jamais des avantages d'une production parfaitement cadencée ; et c'est précisément dans ce contexte que l'automatisation gagne actuellement en importance, y compris dans la sous-traitance et les entreprises de sous-traitance de taille moyenne. Mais comment développer des solutions adaptées et économiques pour ses propres tâches de production ? Les constructeurs de machines du groupe EMAG apportent leur réponse. Vos solutions d'automatisation émanent d'un seul et même fournisseur et sont élaborées en détail en fonction des besoins spécifiques du client. Il en résulte des processus flexibles et automatisés, qui permettent d'une part de réduire les coûts et d'autre part d'améliorer la qualité des pièces et la sécurité des processus.
Images
La société Pucktechnik à Solbiate Arno, non loin de Milan, en est une illustration concrète. Fondée en 2017, cette entreprise de sous-traitance fabrique actuellement des outils de fonderie et divers composants. Au total, l'entreprise dispose de près de 30 machines - dont onze machines EMAG VL et une K 160 L de EMAG Koepfer, ces solutions EMAG assurant une production en série automatisée à grand volume. Ces machines permettent actuellement de fabriquer environ 650 000 roues/moyeux de roue par an. Et relevons avec intérêt la mise en œuvre de quatre lignes de production indépendantes, avec un haut degré d'automatisation. Les machines de ces lignes sont chacune entièrement interconnectées par le système TrackMotion de EMAG, différentes opérations se succédant les unes après les autres. En conséquence, le nombre de pièces produites dans ce domaine a massivement augmenté en quelques années, ce succès reposant sur une approche propre à EMAG : assurer une productivité maximale dans un espace restreint. L'utilisation des machines VL en combinaison avec l'automatisation TrackMotion en témoigne. Le principe technologique de base des lignes est toujours le même (indépendamment du modèle précis de la machine) :
- Le TransLift, un chariot élévateur-retourneur équipé d’un préhenseur électrique programmable, prélève la pièce brute du magasin de pièces, l’achemine à une vitesse de 150 mètres par minute jusqu’à la machine et la dépose sur le shuttle interne.
- Le positionnement vertical de la broche lui permet de prendre la pièce à partir de la position de pick-up du shuttle et de l'amener dans la zone de travail de la machine.
- Une fois la pièce usinée, elle est évacuée de la machine par le shuttle et transportée par le système TrackMotion vers la machine suivante ou le tapis d'évacuation. Le TransLift peut également retourner la pièce lorsque cela s’avère nécessaire.
TrackMotion : configurable en toute flexibilité
Cette base ouvre une multitude de possibilités avec les différents types de machines EMAG. Il est notamment possible de transformer une VL 3 DUO, disposant de deux broches entièrement autonomes dans des espaces de travail séparés pour OP 10 et OP 20, en un système complet et performant. Le système d'automatisation TrackMotion assure non seulement le transport entre le stockage des pièces et les espaces de travail, mails il pivote aussi les pièces entre OP 10 et OP 20. Des solutions « à grande échelle » sont également possibles avec TrackMotion, par exemple pour la fabrication de carters de différentiel. Quatre machines sont utilisées à cet effet : à l'OP 10 et à l'OP 20, le tournage des deux côtés du carter est effectué sur un centre de tournage vertical VL 4. Pour l'usinage de la face extérieure à l'OP 30, EMAG mise sur le tour VT 4. Celui-ci permet un usinage 4 axes de la face extérieure complète en un seul serrage. À l'OP 40, un centre de tournage vertical est à nouveau utilisé, cette fois-ci un VL 6.
Les cellules robotisées : de plus en plus intéressant pour les sous-traitants
Les exigences sur la pièce à usiner et sur le processus de production correspondant sont également au centre des préoccupations des développeurs de solutions robotiques de EMAG. Parmi les questions décisives figurent notamment la taille des lots à produire dans un laps de temps donné et le degré d'autonomie de la solution. Parallèlement, la connexion des machines basée sur la technologie pick-up est particulièrement simple. Le robot dépose la pièce sur un porte-pièce du shuttle de la machine, où l'automatisation interne prend le relais comme décrit. L'alimentation des pièces dans la cellule robotisée se fait par exemple à l'aide de tapis d'alimentation et d'évacuation, de palettiseurs, de tiroirs ou par bin picking, chaque solution présentant des points forts et des conditions de base différentes. Cette approche offre de nombreuses possibilités, comme le montre la combinaison de deux VL 3 DUO avec un robot : deux pièces sont d'abord usinées simultanément d'un côté dans la première machine. Ensuite, le robot les reprend, les retourne et les amène à la machine pour l'usinage simultané du deuxième côté, pour un rendement global élevé sur de courtes périodes. Par ailleurs, la cellule peut être facilement adaptée à d'autres processus. L'exemple du « frein à tambour pour camion » est également intéressant : ici, l'enchaînement de quatre machines de type VL 8 s'effectue au moyen d'un robot sur un axe de déplacement supplémentaire – un concept qui allie la flexibilité d'un robot et la portée d'un portique.
En résumé, la combinaison de la technologie de pick-up EMAG avec diverses solutions d'automatisation, du TrackMotion au robot, aboutit à des systèmes extrêmement performants et adaptables individuellement. De nouvelles machines peuvent être intégrées à tout moment dans le processus. Voilà qui profite aussi et directement aux sous-traitants et aux fournisseurs : ils produisent plus rapidement, sans erreur et à moindre coût - des roues dentées aux arbres et aux moyeux de roue, en passant par les carters de différentiel et de nombreux autres composants.
Interlocuteurs
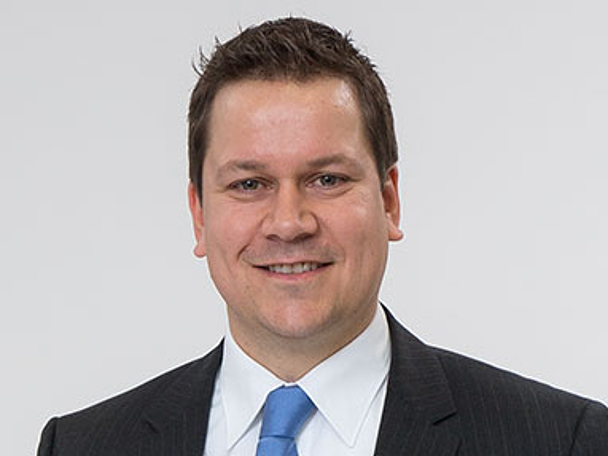
Oliver Hagenlocher
Zone
Press and Communication