02.12.2019 - Oliver Hagenlocher - Noticias
Sistema de Producción de EMAG: Fabricación de ejes de rotor ligeros con sistemas de producción integrales
Numerosos estudios pronostican un rápido crecimiento de la movilidad eléctrica. Las cifras actuales de ventas también indican el cambio. En este sentido, según datos del Center of Automotive Management, las ventas de automóviles eléctricos aumentaron masivamente en China y Estados Unidos el año pasado. En Alemania, la cuota de mercado se duplicó a un nivel bajo. La ingeniería mecánica desempeña un papel central en este desarrollo: debe desarrollar la tecnología de producción con la que los componentes centrales del accionamiento eléctrico puedan fabricarse de forma segura y precisa, en cantidades mucho mayores que antes. El eje del rotor es uno de estos componentes. Debe transmitir el elevado par de giro del electromotor de forma precisa y estable. Al mismo tiempo, la combinación del paquete de placas del rotor y el eje del rotor debe ser lo más ligera posible para aumentar la autonomía del coche eléctrico. Pero, ¿cómo puede fabricarse un complejo eje de rotor de forma eficiente? Los fabricantes de máquinas de EMAG desarrollan diversas soluciones que se adaptan perfectamente a la geometría de los componentes y a la planificación de la producción, desde sistemas de producción perfectamente automatizados hasta máquinas individuales específicas para cada cliente.
Desde hace décadas, la construcción ligera es una de las tareas centrales de la construcción de automóviles: todos los componentes, desde las ruedas dentadas y los ejes de transmisión hasta las diferentes carcasas, deberían ser cada vez más ligeros y pequeños para poder reducir el consumo de los turismos. El tema llega a ser casi más importante en coches eléctricos porque pueden cubrir distancias más largas con menos peso sin recargar la batería. Por tanto, el tema «autonomía» sigue siendo una de las tareas de desarrollo claves en el segmento de la movilidad eléctrica. En este sentido, no encajan los ejes de los motores eléctricos macizos y, por lo tanto, pesados, que cuentan con paquetes de placas de rotor relativamente grandes. En la actualidad, EMAG está mostrando cómo se pueden fabricar en grandes series ejes de rotor de peso optimizado (y, por lo tanto, motores eléctricos de peso optimizado). Los especialistas en sistemas de producción integrales han diseñado una línea en la que el mecanizado suave, el templado y el mecanizado duro se realizan directamente uno tras otro en un eje hueco y, por tanto, ligero. «La producción de un componente de este tipo es, en cualquier caso, una tarea ideal para EMAG», explica Ulrich Heiermann, Manager Technical Application en EMAG. «Disponemos de los conocimientos de aplicación necesarios, desde torneado, taladrado y fresado hasta templado y rectificado. Además, llevamos décadas desarrollando los sistemas de automatización correspondientes. Por lo tanto, el desarrollo completo de la línea y del proceso proviene de una sola fuente. Por otra parte, suministramos soluciones individuales específicas del cliente para subprocesos centrales como torneado o rectificado, que luego se cargan manualmente, por ejemplo, y que también pueden ser el punto de partida para su posterior ampliación a una línea automática completa cuando se instalan máquinas individuales. En ambos casos se utilizan soluciones modulares flexibles. Configuramos máquinas precisas a medida a partir de distintos módulos tecnológicos. Estamos preparados para cualquier requisito».
Eje montado con grandes ventajas.
En la actualidad, el eje de rotor «montado» es un ejemplo impresionante de un enfoque flexible: Según el encargo, EMAG debía desarrollar un sistema de producción de varias etapas que combinara el mecanizado suave, la soldadura láser, el templado y el mecanizado duro. Además, el eje se ensambla durante el proceso a partir de dos piezas finales diferentes; un principio básico conocido, por ejemplo, en los árboles de levas ensamblados. De este modo, el proceso puede dividirse en subprocesos cortos, algunos de los cuales se ejecutan en paralelo. Además, el enfoque a menudo ofrece a los desarrolladores de componentes una mayor libertad. La fabricación final de este eje se lleva a cabo en el sistema EMAG de forma perfectamente sincronizada: en las dos primeras operaciones (10 y 20), las dos piezas brutas diferentes se someten a un mecanizado interior y exterior y se forma también la geometría interior hueca. Se utilizan cuatro máquinas pickup de EMAG del tipo VL 4. Tras un proceso de limpieza (OP 30) se ensamblan las dos piezas terminales en una ELC 250 de EMAG mediante soldadura por láser (OP 40); se trata de un procesamiento sumamente rápido y seguro. La exacta dosificación y concentración de la energía del rayo láser permite una alta velocidad de soldadura y mínimas desviaciones en el componente soldado. A continuación sigue el templado ultrapreciso de tan solo segundos de muñequillas y apoyos en la máquina de templado inductiva MIND 750 de EMAG eldec (OP 50). El mecanizado duro del eje empieza con el torneado exterior en la máquina pickup VT 4-4 (OP 60) de EMAG y el torneado interior en la serie modular VL (OP 70). En OP 80 y 90 se practica un dentado en el eje y se realiza un torneado exterior en los topes. Para el mecanizado de acabado con tolerancias estrechas y elevados requisitos en cuanto a la calidad superficial se recurre al proceso de rectificado final en una máquina rectificadora vertical de ejes de la serie VTC (OP100).
A continuación, el eje está preparado para el ensamblaje con el paquete de chapas correspondiente. En la tecnología de automatización, que garantiza el transporte entre máquinas, EMAG se adapta a las necesidades del cliente. Por ejemplo se utilizan portales de línea, células de apilado, cintas transportadoras o el sistema TrackMotion de EMAG; en cualquier caso, el sistema se beneficia de la uniformidad de las máquinas utilizadas con sus interfaces optimizadas y, no en último término, de la solución completa para el cliente con un sistema completo y EMAG como único contacto necesario durante la planificación, la implementación y el servicio. Además, la tecnología pickup de EMAG garantiza rapidez en el flujo del proceso: el eje (o las dos piezas individuales en el inicio) son transportadas con un husillo portapieza desplazable en la zona de trabajo. Posteriormente, el proceso de torneado y fresado vertical se lleva a cabo con altas velocidades de corte y una caída de viruta optimizada.
Solución rápida a través de un único interlocutor
Cada 45 segundos se produce un eje de rotor en esta línea. Los tiempos improductivos no deseados de una máquina están reducidos al mínimo. «La calidad de un proceso de producción de este tipo se decide ya en una fase de concepción temprana. Aquí es donde EMAG aporta su conocimiento completo sobre las diversas aplicaciones de herramientas, el diseño de máquinas-herramienta multifuncionales, su control y su conexión en cadena. El enfoque se centra siempre en producir un componente óptimo en el tiempo de ciclo y la calidad requerida por el cliente. Si esto se hace en una línea integrada para grandes cantidades anuales o, por ejemplo, con soluciones individuales cargadas manualmente para cantidades más pequeñas y, por lo tanto, con más flexibilidad, es decisión final del cliente», afirma Ulrich Heiermann.
More information about Assembled Rotor Shafts for Weight-Optimized Electric Motors you will find here...
Descargas
Persona de contacto
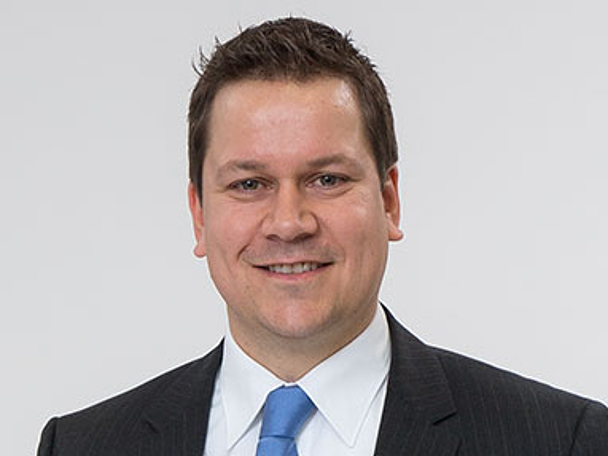
Oliver Hagenlocher
Área
Press and Communication