09.09.2024 - Oliver Hagenlocher - Presse
Die neue VST 50 von EMAG: Alle sieben Sekunden verlässt ein neuer Kugelzapfen die Maschine
Ob im Bereich von Lenkung oder im Fahrwerk – Kugelgelenke sind in unseren Pkws unverzichtbar. Sie fungieren nicht nur als eine Art Drehpunkt zwischen verschiedenen Elementen, sondern sind zumeist auch ständig in Bewegung und dabei einer hohen physikalischen Belastung ausgesetzt. Vor diesem Hintergrund gehören die Kugelzapfen und Kugelhülsen zu den sicherheitskritischen Pkw-Bauteilen, die ausnahmslos mit einer hohen Oberflächenqualität und mikrometergenau die Produktion verlassen müssen – und das trotz hoher Stückzahlen und einem allgemeinen Kostendruck. Wie lässt sich diese Aufgabe besonders effizient und mit minimalen Span-zu-Span-Zeiten umsetzen? Mit einer neuen Maschine gibt EMAG darauf jetzt eine Antwort: Bei der VST 50 verlässt alle sieben Sekunden ein fertiger Kugelzapfen die Maschine, wobei jedes Bauteil eine außergewöhnlich umfassende Messung durchläuft.
Bilder
Es ist eine neue Aufgabe für die süddeutschen Drehspezialisten – bislang gehörten Kugelzapfen nicht zu den typischen Automotive-Bauteilen, die eine EMAG Maschine durchliefen. Wie kam es also zu dieser Entwicklung? „Dazu muss man sagen, dass die Aufgabe in vielerlei Hinsicht grundsätzlich sehr nach EMAG klingt. Es geht um große Stückzahlen, spezielle Oberflächenanforderungen und niedrige Stückkosten. Diese Qualitäten stellen wir immer wieder für verschiedene Bauteile sicher“, erklärt Projektleiter und Entwicklungsingenieur Frank Haas von EMAG. „Insofern lag es auf der Hand, dass ein großer Kunde vor einiger Zeit mit dieser Aufgabe auf uns zukam. Die Frage war dabei vor allem, ob wir die Leistungswerte von vorhandenen Maschinen bei der Kugelzapfen-Produktion übertreffen können. Dies war der Startpunkt für die Entwicklung der VST 50.“
Das Ergebnis liegt nun bereits seit einiger Zeit vor und ein einfacher Blick auf diese Maschine macht deutlich: Hier haben die Entwickler eine besonders gute Arbeit geleistet. Die VST 50 verfügt einerseits über hochautomatisierte Prozesse, wobei unter anderem drei Roboter zum Einsatz kommen. Andererseits lässt sie sich mithilfe der EDNA Apps einfach bedienen, was im Übrigen auch diverse Messungen und die Roboter miteinschließt. Für die eigentliche Drehbearbeitung von Kugel und Hals des Kugelzapfens (nur um diese Bereiche geht es hier) gibt es zwei hängende Werkstückspindeln, die sich unabhängig voneinander verfahren lassen. Folglich wird immer eine Spindel be- und entladen, während die andere beim Bearbeitungsprozess im Einsatz ist. Der dazugehörige Werkzeug-Kreuzschlitten ist gewissermaßen zweigeteilt: Die Werkzeuge auf der linken Seite sind auf einer rotativen B-Achse montiert, die es ermöglicht, die Kugel präzise zu drehen und zu glätten. Zusätzlich kann der Kugeldurchmesser und die Kugelform mithilfe einer linearen U-Achse angepasst werden. Auf der rechten Seite sind spezielle Werkzeuge für die Halsbearbeitung angebracht.
Hochproduktive Beladung
Für die Be- und Entladung dieser Konstruktion sorgen wiederum die drei Roboter, die sich parallel angeordnet vor der Maschine befinden, wobei jeder für einen anderen Teilprozess verantwortlich ist: Der linke Roboter übernimmt das Werkstückhandling zwischen der Übergabestation und der ersten Werkstückspindel. Der mittlere Roboter führt dieselbe Aufgabe an der zweiten Werkstückspindel aus, während der rechte Roboter das Werkstückhandling zwischen der Übergabestation und den äußeren Automationsbaugruppen übernimmt. Aber warum setzt man an dieser Stelle nicht auf einen Roboter, der diese drei Aufgaben abwechselnd ausführt? „Das wäre sicherlich möglich“, bestätigt Haas. „Allerdings würden wir so die extrem kurzen Taktzeiten nicht erreichen. Die verschiedenen Bewegungen werden teilweise zeitgleich ausgeführt. Unsere Lösung sorgt dafür, dass alle sieben Sekunden ein fertiges Werkstück die Maschine verlässt und die Span-zu-Span-Zeit unter 2 Sekunden beträgt.“
Rasantes Tempo und Präzision – vor diesem Hintergrund erklärt sich auch, warum die angesprochenen Roboter zusätzlich beim Werkzeugwechsel zum Einsatz kommen, wobei EMAG den gesamten Prozess gewissermaßen zweigeteilt hat. Da ist zum einen die Aufgabe des Bedieners: Er sieht auf dem zentralen Bedienpanel immer eine Vorhersage zum Werkzeugwechsel. Wenn er ein Werkzeug austauschen will, drückt er einfach eine Taste und das Werkzeugmagazin schwenkt für den Tausch nach außen. Wichtig dabei: Der Produktionsprozess wird währenddessen nicht unterbrochen. Nach dem Austausch schwenkt das Magazin zurück in seine Ausgangsposition. Der händische Prozess ist somit abgeschlossen und es folgt ein automatisierter Prozess im zweiten Schritt. Dazu legt der linke Roboter zunächst seinen Werkstückgreifer ab und nimmt einen Werkzeuggreifer auf. Anschließend entnimmt er das verschlissene Werkzeug aus dem Innenraum der Maschine und tauscht es gegen ein neues aus, das er aus dem angesprochenen Magazin entnimmt. Um die Prozessfähigkeit weiter zu steigern, ist jedes Werkzeug mit einem RFID-Chip codiert, damit die Werkzeugdaten entsprechend übertragen werden können. Der gesamte Werkzeugwechsel vollzieht sich dabei in weniger als 90 Sekunden.
Lichtband-Mikrometer liefert viele Messwerte
Bleibt zuletzt ein Blick auf das Thema Prozesssicherheit als zentraler wirtschaftlicher Faktor bei einem Bauteil, das ohne jede Fehlertoleranz die Produktion verlassen muss. Hier setzt EMAG auf eine 100-Prozent-Lösung: Jedes Bauteil durchläuft ein Lichtband-Mikrometer, das die benötigten Messwerte in Sekundenbruchteilen ermittelt, wobei das Ergebnis sehr umfassend ist. Es wird der finale Kugel- und Halsdurchmesser bestimmt und zugleich etwaige Späne detektiert. Dazu kommt eine hochauflösende Prozesskamera, die sich unmittelbar vor den Ladeluken befindet. Ihr Live-Bild erscheint nach Knopfdruck auf dem Panel. Der Bediener kann somit einfach überprüfen, ob beispielsweise die Spänebildung eine Störung im Prozess verursacht.
Insgesamt ist diese Lösung sehr variabel, denn die VST 50 eignet sich grundsätzlich sowohl für kurze Kugelzapfen (Kugeldurchmesser 16 bis 40 mm, Bauteillänge 50 bis 150 mm) als auch für lange Kugelzapfen (Kugeldurchmesser 22 bis 35 mm, Bauteillänge 150 bis 455 mm). Zudem können Kugelhülsen mit ihr bearbeitet werden – und das alles mit dem angesprochenen enormen Tempo. Nach einer Schätzung von EMAG ist die VST 50 rund doppelt so schnell wie andere Produktionslösungen für dieses Bauteil, was natürlich auch für sinkende Stückkosten sorgt. So verlässt mit einem rasanten Tempo ein perfektes und vermessenes Bauteil die Maschine. Dabei ermöglichen die EDNA Apps immer eine weitgehend intuitive Bedienung. „Wir heben die Produktion des Kugelzapfens auf ein neues Niveau“, fasst Frank Haas das Ergebnis zusammen. „Vor diesem Hintergrund sind wir überzeugt davon, dass diese Maschine sehr positiv im Markt aufgenommen wird – übrigens auch von anderen Branchen, denn Kugelgelenke kommen ja nicht nur im Auto vor.“
Ansprechpartner
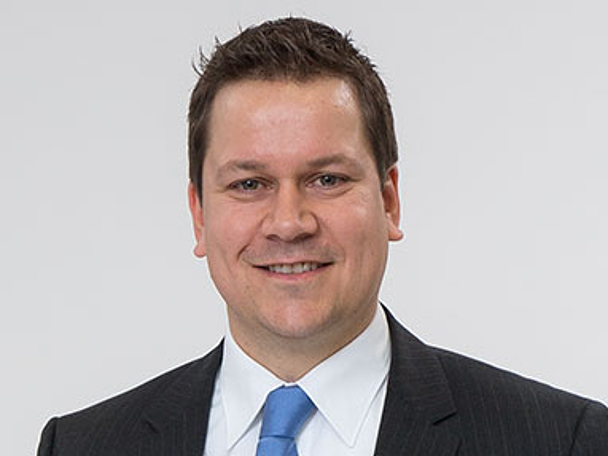
Oliver Hagenlocher
Bereich
Presse und Kommunikation