06.08.2019 - Oliver Hagenlocher - Presse
EMO 2019 – Linienlösungen mit der VL 1 TWIN: Die Stückkosten für Planeten- oder Kegelräder massiv herunterdrehen
Kostendruck, hohe Qualitätsanforderungen und nicht zuletzt riesige Stückzahlen – im Pkw-Getriebebau prallen Extreme aufeinander. Dabei dürften die Fertigungsmengen in den nächsten Jahren sogar noch zunehmen. So schätzen die Autoren der aktuellen „Shell Pkw-Szenarien“, dass sich die globale Pkw-Flotte bis 2050 auf 2,5 Milliarden Fahrzeuge mehr als verdoppeln könnte. Fast unvermeidlich rücken dabei die „Cost per piece“ in den Fokus der Produktionsplaner: Wie lassen sich typische Getriebe-Massenbauteile wie Planetenräder oder Kegelräder noch effizienter produzieren? Eine passgenaue Antwort auf diese Frage gibt die EMAG Gruppe mit der Entwicklung der zweispindligen Pick-up-Drehmaschine VL 1 TWIN. Sie bearbeitet zwei gleiche Bauteile simultan in einem Arbeitsraum. Auf dieser technischen Basis eröffnen sich weitreichende Möglichkeiten: Wenn zwei Maschinen zu einer Linie verbunden werden, kann eine Bearbeitung des Planetenrads von zwei Seiten erfolgen – und das mit niedrigen Taktzeiten. Wie genau sieht die Linienlösung für Planetenräder oder Kegelräder aus?
Bilder
Es ist keine Seltenheit, dass an einzelnen Produktionsstandorten pro Jahr bis zu einer Million Planetenräder entstehen – bereits der einfache Blick auf den Einsatz des Bauteils in einer sogenannten Wandlerautomatik liefert dafür eine Erklärung, denn das dazugehörige Planetengetriebe besteht zumeist aus vier Planetenradsätzen mit jeweils drei Planetenrädern und einem Sonnenrad. Insgesamt befinden sich hier also 16 Zahnräder. Interessant ist darüber hinaus, dass die Wandlerautomatik aktuell an neuer Bedeutung gewinnt. Zum einen gilt sie nach wie vor als eine komfortable, kompakte und robuste Getriebelösung. Zum anderen setzen einige Hersteller auch bei der Konstruktion von modernen Hybridantrieben auf die Technologie. „Vor diesem Hintergrund erklärt sich die Entwicklung der VL 1 TWIN. Sinkende Kosten bei der Herstellung von Planetenrädern und Kegelrädern standen ganz oben auf der Agenda“, erklärt Björn Svatek, Sales & Marketing Director Modular Solutions bei EMAG. „Deshalb setzen wir bei dieser doppelspindligen Maschine auf eine Simultanbearbeitung von zwei gleichen Bauteilen in einem Arbeitsraum. Das führt zu hohen Ausbringungsmengen in kurzen Zeiträumen. Auf der anderen Seite haben wir durch konsequentes Kostencontrolling den Preis pro Spindel deutlich reduziert. Das trägt zu niedrigen ‚Cost per Piece‘ bei.“
Planetenrad: Alle 20 Sekunden zwei Fertigteile
Wie genau sieht eine denkbare VL-1-TWIN-Linienlösung für die Weichbearbeitung von jenen Planetenrädern aus? Grundsätzlich vollzieht sich der Prozess in zwei Maschinen, die per TrackMotion-Automationssystem miteinander verbunden sind. Dabei greift der dazugehörige TransLift (ein Hub-Wendewagen mit Elektrogreifer) gleichzeitig zwei Rohteile vom Zuführband und transportiert sie zur ersten Maschine. Hier übernehmen die zwei Pick-up-Spindeln der VL 1 TWIN und führen die Bauteile dem Arbeitsraum zu. Es folgt die Drehbearbeitung der ersten Seite von Innen- und Außendurchmesser (OP 10 – OP 10). Durchmesser und Länge (X-/ Z-Richtung) der beiden Bauteile lassen sich dabei unabhängig voneinander korrigieren, weil die Spindelkästen autark verfahren können. Dies ist insbesondere nach einem Werkzeugwechsel wichtig, um Abweichungen (beispielsweise nach Wechsel der Wendeplatten) zu kompensieren. Nach dem Heraustransport aus dem Maschinenraum übernimmt wieder der TransLift, dreht die zwei halbfertigen Bauteile um 180 Grad und transportiert sie zur anderen VL 1 TWIN. Hier wird die zweite Seite des Außendurchmessers plangedreht (OP 20 – OP 20). Abschließend landet das fertige Bauteil per TrackMotion auf dem Speicherband, das bis zu 400 Fertigteile auf den integrierten Stacker-Einheiten aufnehmen kann. Der Gesamtprozess vollzieht sich mit einer Taktzeit von rund 20 Sekunden für zwei Bauteile. Dabei beträgt die durchschnittliche Span-zu-Span-Zeit nur knapp 5 Sekunden. Eine Reihe von technischen Ausstattungsdetails ermöglicht dieses enorme Tempo: So weisen die zwei Pick-up-Spindeln hohe Antriebswerte von 9,9 kW und 136 Nm bei 40% ED auf. Gleichzeitig verfügt der verschleißfreie Linearantrieb in der X-Achse (in Kombination mit direkten Wegmess-Systemen) über eine hohe Beschleunigung von 8 m/s2 – hohe Dauergenauigkeit inklusive. Dadurch können die häufig geforderten H6-Passungen der Hauptbohrung prozesssicher hergestellt werden.
Kegelrad: Bohren, Schruppen und Schlichten in einer Maschine
Aufgrund des steigenden Kostendrucks bei der Fertigung von Kegelrädern müssen sämtliche Prozesse mit hoher Effizienz erfolgen – die Herstellung per Schmiedeprozess hat hier Vorteile: Modern gefertigte Kegelräder verlassen die Schmiede häufig mit einer bereits „finish bearbeiteten“ Kegelradverzahnung. In diesem Fall ist lediglich ein Drehprozess in einer Aufspannung nötig. Hier bietet EMAG mit der VL 1 TWIN die optimale Lösung für die parallele Weichbearbeitung an zwei Kegelrad-Rohlingen (OP 10 – OP 10). In der Maschine laufen vier Bearbeitungsschritte hintereinander ab und die Taktzeit beträgt nur rund 25 Sekunden: Nach der Zuführung per TrackMotion beziehungsweise Pick-up-Spindel entsteht die zentrale Bohrung des Bauteils per Bohrprozess „ins Volle hinein“, danach startet das Schruppen der Kalotte. Im dritten und vierten Schritt erfolgt das Schlichten von Bohrung und Kalotte. Eine spezielle Spannlösung bildet die Verzahnung des Bauteils negativ ab und hält es die ganze Zeit über stabil in Position. Mit Blick auf den massiven Bohrprozess spielt das Maschinenbett aus Mineralit® eine besondere Rolle, denn der Polymerbeton reduziert die Schwingungen während des Bohrprozesses und sorgt somit für zusätzliche Präzision. Ein optional angebotenes Messsystem für die Werkstückvermessung zwischen Arbeitsraum und Pick-up-Stationen erhöht die Prozesssicherheit. Grundsätzlich ist es auch möglich, zwei VL 1 TWIN mit nur einem TrackMotion-System zu verketten und in den Maschinen dann den gleichen Prozess zu vollziehen (OP 10 – OP 10, OP 10 – OP 10). Hier ist entscheidend, dass sich der TrackMotion-Greifer mit einer Geschwindigkeit von bis zu 150 Metern pro Minute bewegt und den Zu- und Abtransport an den parallel arbeitenden TWIN-Maschinen garantiert.
Perfekte Lösung für den Getriebebau
Insgesamt ermöglicht der TWIN-Ansatz große Produktivitätssprünge bei einer ganzen Reihe von weiteren Bauteilen – von Nockenstücken über Lagerringe bis hin zu Flanschen. Je nach Anforderung entstehen Multi-Technologie-Fertigungslinien, zu denen beispielsweise auch EMAG Wälzfräs- und Entgratmaschinen gehören. „Wir sind überzeugt davon, dass die VL 1 TWIN eine perfekte Lösung für die wachsenden Stückzahlen und den zunehmenden Wettbewerb im Getriebebau darstellt“, sagt Björn Svatek. „Anwender profitieren von sinkenden Stückkosten, kurzen Taktzeiten und einer hohen Prozesssicherheit. Diese Vorteile wollen wir verstärkt in den Mark einbringen.“
Die VL 1 TWIN live auf der EMO 2019
Ansprechpartner
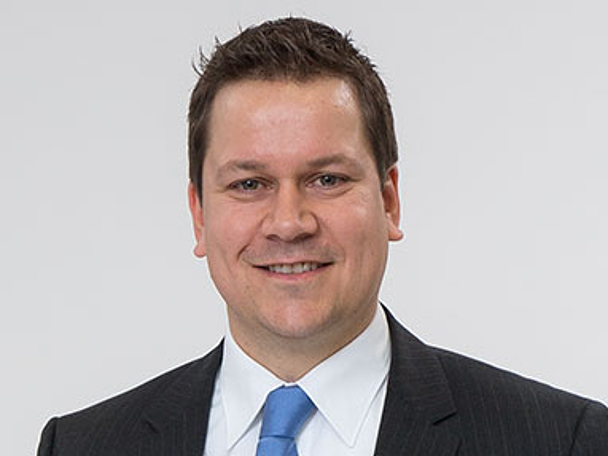
Oliver Hagenlocher
Bereich
Presse und Kommunikation