27.02.2024 - Oliver Hagenlocher - Kundenstories
Bharat Forge Daun setzt auf EMAG: Den spanenden Prozess am Statorgehäuse rundum perfektionieren
Ungewöhnlich anspruchsvolle Bauteile, dazu hochfeste Werkstoffe für Hightech-Anwendungsfelder – bei Bharat Forge Daun entstehen beispielsweise Statorgehäuse für die Elektromobilität, wobei die Spezialisten immer im Mikrometerbereich für Qualität sorgen. Dabei mittendrin: Mehrere Vertikal-Drehmaschinen von EMAG, die rund um die Uhr an fünf Tagen der Woche ihren Dienst verrichten. Dass es dabei auch und gerade auf den nötigen Service von EMAG ankommt, liegt auf der Hand. Aber was genau gab den Ausschlag bei der Investitionsentscheidung für diese Maschinen?
Bilder
Komplexität ist so etwas wie das Steckenpferd von Bharat Forge Daun: Das Unternehmen mit Sitz im Herzen der Eifel, rund 50 Kilometer entfernt von Koblenz, produziert einerseits als Lohnfertiger rotationssymmetrische Serienbauteile sowie andererseits Werkzeuge und Formen, die anschließend beispielsweise bei den Schmiedeexperten von Bharat Forge CDP und Bharat Forge Aluminiumtechnik zum Einsatz kommen. Das heißt: Hier geht es immer um diffizile Oberflächen und Lageanordnungen. „Extreme Genauigkeitsanforderungen im Mikrometerbereich gehören bei uns immer dazu“, fasst Christoph Steffens, Leiter Mechanische Fertigung bei Bharat Forge Daun, die Ausgangssituation zusammen. „Vor diesem Hintergrund überwachen wir die Prozesse sehr umfassend, führen dabei viele Messungen durch und begleiten auf Wunsch sogar die Bauteilentwicklung – sodass die Produktion des Bauteils effizient vonstattengeht. Dieses Know-how bieten wir im Markt für Branchen wie der Automobilindustrie, dem allgemeinen Maschinenbau oder der Produktion von Landwirtschaftsmaschinen an.“
Schmiede-Statorgehäuse effizient bearbeiten
Was das konkret bedeutet, zeigt in besonderer Weise ein Statorgehäuse, das im Hybridabtrieb eines großen deutschen Automobilunternehmens zum Einsatz kommt. Schon auf den ersten Blick wird deutlich: Seine topfartige Form sowie diverse geometrische Details sind anspruchsvoll. Darüber hinaus ist der Rohling ein Schmiedebauteil aus Stahl – in diesem Anwendungsbereich eine Seltenheit. Dessen Materialeigenschaften fordern die südwestdeutschen Zerspanungsexperten zusätzlich heraus. Zudem hat der Auftraggeber im Laufe der Jahre die gewünschten Stückzahlen kontinuierlich gesteigert (und wird sie weiter steigern). Wie bringt man in diesem Umfeld also Genauigkeit, Effizienz und Prozesssicherheit zusammen? Die Antwort von Bharat Forge Daun hat in weiten Teilen mit dem Maschinenbau von EMAG zu tun, denn die Spezialisten setzen seit einiger Zeit auf Drehmaschinen von EMAG.
Vertikale Bauweise mit entscheidenden Vorteilen
Die vertikale Bauweise dieser Lösungen spielte für die Investitionsentscheidung eine wichtige Rolle. So machte die horizontale Maschine eines anderen Herstellers in der Vergangenheit einige Schwierigkeiten. Es bildeten sich zum Beispiel regelmäßig störende Spänenester, die man zwei- bis dreimal pro Schicht manuell entfernen musste. „Somit lag es für uns auf der Hand, dass wir diese Prozesse in Maschinen mit vertikaler Bauweise ausführen, weil ihr freier Spänefall viele Störungen verhindert. Unsere Zielsetzung war ein Maximum an Prozesssicherheit“, betont Steffens. Die Entscheidung für EMAG basierte darüber hinaus auf vorhandenem Know-how: Die Maschinenbauer zeigten an Beispielen von anderen Kunden, wie die Stator-Bearbeitung in ihren Maschinen abläuft – mit niedrigen Nebenzeiten und hochpräzisen Handlings-Prozessen. Eine integrierte Automation inklusive Pick-up-Spindel und seitlichem Transportband sichert schnelle Abläufe, während der stabile Grundkörper aus dem Polymerbeton Mineralit® für Qualität bei Dreh- und Fräsprozessen steht.
EMAG Service im Fokus
Nicht zuletzt spielt für Bharat Forge Daun die Reaktionszeit und das Know-how des Service von EMAG eine wichtige Rolle. So ist ein regionaler Servicetechniker immer in wenigen Stunden vor Ort und löst etwaige Probleme direkt. „Die Maschinen sind sehr robust. Nichtsdestotrotz ist dieses Thema wichtig, denn wir produzieren an fünf Tagen der Woche im Drei-Schicht-Betrieb und bislang wurde uns bei kleineren Störungen immer in Rekordzeit geholfen – etwa bei einer defekten Lichtschranke. Länger als zwei Stunden hat die Reparatur noch nie gedauert“, so Christoph Steffens, der im Übrigen davon berichtet, dass EMAG auch per Remote-Service bereits zur Stelle war.
Ansprechpartner
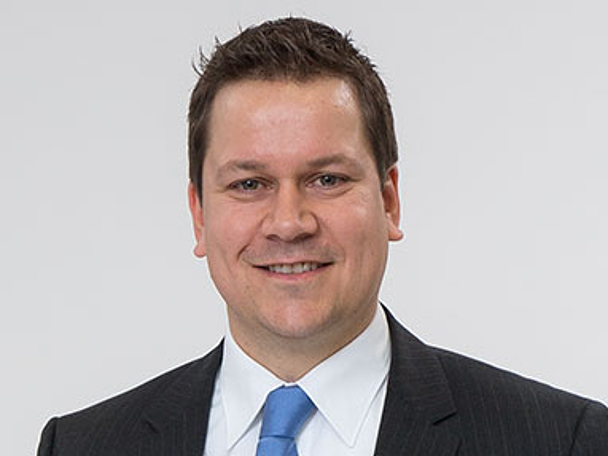
Oliver Hagenlocher
Bereich
Presse und Kommunikation