14.10.2019 - Oliver Hagenlocher - Presse
EMAG Produktionssystem: Die Finish-Bearbeitung der Turboladerwelle perfektioniert
Die Turboladerproduktion gehört zu den anspruchsvollsten Aufgaben im Automobilbau: Hochfeste Werkstoffe, präzise geometrische Anforderungen, große Stückzahlen und Preisdruck prägen die Aufgabenstellung bei OEMs und Zulieferunternehmen. Dazu kommt: Angesichts des zunehmenden Downsizings im Automobilbau – mehr Leistung bei immer kleiner werdenden Hubräumen – rücken Bauteile wie die Turboladerwelle stärker in den Fokus der Produktionsplaner. Gefordert werden automatisierte Produktionslösungen, die höhere Stückzahlen bei sinkenden „Costs per Piece“ ermöglichen, dabei aber hochpräzise Prozesse garantieren. Eine ganzheitliche Lösung für diese Aufgabenstellung hat aktuell EMAG entwickelt: In einem verketteten Produktionssystem „aus einer Hand“ erfolgt die komplette Finish-Bearbeitung der Turboladerwelle vom Vordrehen, Härten und Schleifen bis zum ECM-Auswuchten. In unter 50 Sekunden verlässt ein Bauteil in „Endqualität“ die Linie.
Der Downsizing-Trend im Automobilbau geht weiter. So prognostiziert beispielsweise der VDMA in seiner Studie „Antrieb im Wandel“, dass bis zum Jahr 2030 die Zahl der Zylinder in den Pkw von heute durchschnittlich 4,3 auf 4 zurückgeht. Die Motoren von morgen werden also noch kleiner. Gleichzeitig sinkt ihr Hubraum, was durch eine höhere Turboladeraufladung kompensiert wird: Die angesaugte Luft wird noch stärker verdichtet und mit maximalem Druck in den Brennraum gepresst. In der Praxis führt das zu extremen Leistungswerten: In modernen Motoren dreht sich das Verdichterrad mit bis zu 290.000 Umdrehungen in der Minute und es entstehen enorm hohe Temperaturen am Bauteil. Unter diesen Voraussetzungen gehört die Herstellung von Turboladerwellen zu den besonders anspruchsvollen Aufgaben im Automobilbau. Sie werden aus Hochleistungswerkstoffen wie Inconel hergestellt, die Temperaturen von über 1000 Grad Celcius standhalten, sich aufgrund ihrer Härte aber nur schwer bearbeiten lassen. Trotzdem gilt es gerade im Turboladerbereich, große Stückzahlen mit hoher Präzision und Prozesssicherheit zu produzieren – insgesamt eine klassische Aufgabe für EMAG, wie Markus Neubauer, Technical Application Engineer bei EMAG, betont: „Unser umfassendes Know-how kommt uns hier zugute, denn wir decken durch unser breites Technologiespektrum die gesamte Prozesskette von der Vorbearbeitung bis zum Finish inkl. Wuchten ab. Folglich kommt die komplette Linie mit Planung, Projektmanagement, Realisierung und Service aus einer Hand. Das ist eine Qualität, die auch und gerade bei der Etablierung einer neuen Turboladerproduktion eine entscheidende Rolle spielt. Für die Kunden vereinfacht sich massiv der gesamte Planungs- und Aftersale-Prozess.“
Drehen, Härten, Schleifen und Auswuchten in einer Linie
Warum das ein großer Vorteil ist, offenbart der Blick auf den anspruchsvollen Prozess, der vom Vordrehen und induktiven Wärmebehandeln über das Schleifen bis zum elektrochemischen Wuchten reicht. Insgesamt gibt es fünf Hauptoperationen:
- Zu Beginn der Linie setzt ein Palettier-Roboter die Rohteile auf das Förderband der Vertikaldrehmaschine VTC 100-4 ab, anschließend transportiert der Werkstückgreifer der Maschine das Bauteil in den Arbeitsraum. In einer Aufspannung erfolgt das Vordrehen der Turbinenwelle, wobei die Vier-Achs-Bearbeitung reduzierte Hauptzeiten garantiert. Durch den vertikalen Aufbau und dem damit verbundenen freien Spänefall werden Spänenester vermieden.
- Ein zweiter Roboter entnimmt die vorgedrehten Teile vom Förderband der VTC 100-4 und führt sie der Wärmebehandlung in der MIND-M 1000 von EMAG eldec zu, in der die Bauteile sehr schnell auf eine präzise Temperatur erwärmt werden. Die Experten sprechen hier von einem „Stress relieve“: Etwaige Spannungen, die im Bauteil vorliegen, werden so gezielt abgebaut. Sollte es nötig sein, die Lagersitze am Bauteil zu härten, wäre dies in dieser Maschine ebenso möglich.
- Diverse Schleifbearbeitungen finden in der dritten und vierten Operation statt: Zunächst vollzieht sich in einer HG 204 von EMAG die horizontale Schleifbearbeitung der Welle. Anschließend werden in der vertikalen Schleifmaschine VLC 200 GT Ringnuten und die Flügelaußenkontur des Turbinenrads feinbearbeitet. Optional kann mit einer zusätzlich angetriebenen Bürste im Arbeitsraum der VLC 200 GT die Flügelkontur entgratet werden.
- Nachdem die Bauteile eine Waschanlage und ein Messsystem durchlaufen haben, kommt es zur abschließenden Operation: dem Auswuchten per Elektrochemischer Metallbearbeitung in einer CS-Maschine von EMAG ECM. Der spanlose Prozess erfolgt mit nur einem Wiederholungsschritt. Durch den berührungslosen Materialabtrag ist der Werkzeugverschleiß minimal – ein großer Vorteil im Vergleich zu spanenden Verfahren.
Perfekte Prozesse für eine einbaufertige Endqualität
Die gesamte Finish-Bearbeitung der Pkw-Turboladerwelle (Turbinenläufer) erfolgt in weniger als 50 Sekunden Linien-Taktzeit. Im Dreischichtbetrieb führt das zu einer jährlichen Ausbringung von 420.000 bis 450.000 Turbinenläufern. In jedem Fall gilt: Nach dem abschließenden Auswuchten weist das Bauteil eine einbaufertige „Endqualität“ auf. „Letztlich garantieren wir bei diesen und ähnlichen Projekten immer eine passgenaue Anlagenarchitektur. Dazu bringt EMAG im Kontakt mit dem Kunden sein komplettes Wissen ein – über ganz unterschiedliche Werkzeuganwendungen, die Konzeption von multifunktionalen Werkzeugmaschinen, ihre ganzheitliche Steuerung und Verkettung sowie die Anbindung an übergreifende Systeme“, fasst Markus Neubauer zusammen. „Dieses Know-how aus einer Hand ist auch und gerade bei der Herstellung von anspruchsvollen Bauteilen ein Erfolgsgarant, mit dem wir im Markt überzeugen.“
Bilder
Downloads
Ansprechpartner
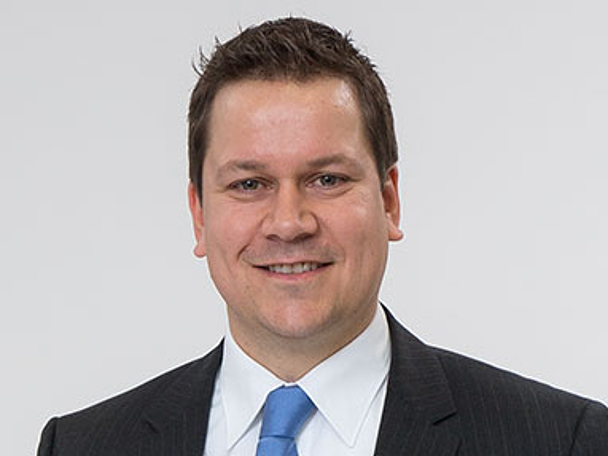
Oliver Hagenlocher
Bereich
Presse und Kommunikation