09/30/2020 - Oliver Hagenlocher - Press
Using scroll-free turning to optimize the production of rotor shafts
The automotive industry is in transformation and production planners are placing increasing importance not only on new components, but also on new manufacturing methods. After all, the increased demand for electric vehicles is also leading to higher production capacities. This raises the question of how this production can be optimized to be as efficient as possible.
A core element is certainly the electric motor itself. For its main component, i.e. the rotor shaft with laminated core, EMAG has developed a highly efficient machining procedure that offers virtually unrivaled speed and quality.
Images
For quite a while now, some projects have implemented overturning instead of grinding in the production of rotor shaft laminated cores. Since EMAG manufactures not only vertical turning centers but also grinding machines, the decision of whether grinding or turning should be the technology of choice for the respective inquiries was made based on customer preferences and the surface requirements. Turning additionally offers the advantage that dry machining of the laminated core is possible. However, achieving surface qualities of Rz < 6.3 μm is time-consuming with conventional longitudinal turning. Therefore EMAG started to experiment with scroll-free turning. Since this technology has already been in use at EMAG for quite some time and it is constantly being further developed, EMAG is well aware of the great potential it offers in combination with the high performance of the vertical turning centers.
Twist-free surfaces and rapid feed rates
With scroll-free turning, an inclined cutting edge is swiveled past the rotating workpiece. The point of contact moves progressively along the cutting edge. Thus the entire cutting edge is used and the tool life is improved. The advantage of this technology is very short cycle times (up to 10-times faster than grinding or longitudinal turning).
Scroll-free turning has many advantages for the user:
- The possibility of creating twist-free surfaces with hard machining
- Very short cycle times resulting from a higher feed rate per rotation
- Improved tool life achieved by using the entire cutting edge
The challenge was to implement this technology in the machining of rotor shafts and laminated cores in such a way that these advantages can be exploited — and EMAG succeeded. This machining technology has proven to be particularly suitable for creating surface qualities of Rz < 6.3 μm with maximum feed rates of up to 1 mm/rev. Due to the layered structure of the laminated cores, the chip breaks after 1 to 1.5 revolutions, depending on the thickness of the metal and the feed rate. This prevents the formation of balls of chips that usually result from long strip chips getting wound up during conventional turning at low feed rate.
Reduced costs for rotor shaft machining
It should come as no surprise that the advantages of scroll-free turning also have positive effects on the unit costs. The shorter cycle times lower the machine costs, while the tool costs and tool change costs are reduced thanks to longer tool lives (resulting from the short contact time of each point along the entire cutting edge).
However, scroll-free turning is a very sophisticated manufacturing process that requires an appropriate machine base and the necessary know-how. And this is where EMAG shines with the comprehensive package the company can offer.
4-axis machining of rotor shafts
The vertical 4-axis shaft turning machines of the VT series are ideal for manufacturing rotor shafts. When it comes to machining components with a maximum length of 630 millimeters and a maximum diameter of 200 millimeters, the machines are able to fully exploit their qualities:
- Simultaneously: The machining process is performed with four axes, from two sides simultaneously. To this end, the machine is equipped with two tool turrets with twelve posts each, of which 11 can be loaded with turning tools or driven tools; one post on each turret is occupied by a workpiece gripper.
- Automatically: The workpiece grippers ensure the parallel loading and unloading of the machine. While one gripper brings a new raw part into the clamping position, the other one transfers the finished part out onto the workpiece conveyor. To achieve this, the VT series is equipped with circulating parts storage units from which raw parts can be picked up and into which finished parts can be deposited. The TrackMotion automation system allows multiple VT machines to be interlinked very easily and cost-efficiently.
Scroll-free turning on VT machines
Thanks to EMAG’s many years of experience, the scroll-free turning technology is already optimally adapted for use in series production. The same applies to the machines used, which have been perfectly configured for this technology based on the lessons learned from many applications and tests. For example, the turning turret of the VT series has been adapted to the special requirements of scroll-free turning. This applies not only to the mechanical components, but also to the parameterization of the swiveling axis and the settings used to control it. On the software side, there is also nothing that prevents scroll-free turning technology from being used on the vertical shaft turning centers. Appropriate programs for the control system makes setting up the machine as easy as when using conventional turning processes.
Further information:
This animation illustrates the interlinking, based on the example of rotor shaft machining: https://www.youtube.com/watch?v=B9pywqiPg-s
Downloads
Contact
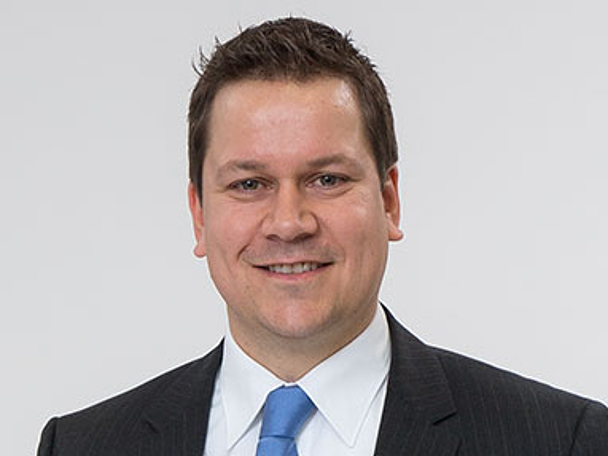
Oliver Hagenlocher
Area
Press and Communication