05/10/2021 - Oliver Hagenlocher - Press
Manufacturing solution for trucks: EMAG presents a compact manufacturing solution for large brake drums in the commercial vehicles segment
Trucks are the most commonly used means of freight transportation in the world. In Germany, more than 71 percent of goods are delivered by truck; in the USA, that figure is up to 72.5 percent. More than 3.2 bn tons of goods were moved on German roads in 2019 alone. In the USA, the volume was almost 4 times as high, at 11.8 bn tons—and the trend is moving upward, across the globe. It's clear that trucks are set to remain the most important means of transport for the logistics industries, despite competition from rail, water, and air. This increase in demand is also being felt by manufacturers, so they are constantly on the lookout for highly productive and reliable manufacturing solutions in this segment. When EMAG was asked by a leading manufacturer if it could apply its expertise from the automotive industry to the manufacturing of truck brake drums, the response was easy.
EMAG is known, above all, for very compact manufacturing solutions. That is due to the high degree of automation and the vertical structure of its pick-up machines. This allows the machines to be positioned very close to manufacturing cells, which can then be copied and reproduced according to the output capacity required. This concept was applied once again when designing the manufacturing line for truck brake drums, where the company succeeded in compressing the entire machining process into just three operations.
Machining of truck brake drums in three operations
The entire manufacturing system has been geared to simplicity and maximum functionality. It is important to note that all its components come from a single provider: from the machines (VL 8 turning centers from EMAG, used for all the machining work), robotic handling, and automation, through to the peripherals, clamping devices, tools, and technology, optimized by EMAG's experts. The customer receives a perfectly coordinated system, designed for maximum productivity. EMAG also takes care of all service and maintenance. Regardless of which component is involved, all the customer needs to do is contact EMAG Service, which then arranges everything else – which is a big plus for many customers.
However, what does the process look like in detail?
First, the raw parts are delivered on pallets. The highly flexible automation system takes over all the handling of the parts from there. EMAG has opted for a robotic rail system to handle this task, which is a solution that offers both high performance and many degrees of freedom. In OP 10, which is carried out on two machines due to the cycle time, all the turning work on the first side of the brake drum is done, both inside and outside.
The part is turned over between OP 10 and OP 20, and now the
bolt ring on the brake drum can be machined, including drilling the holes for the bolts. This is made possible by a turret on which driven tools can be used. OP 30 then follows with the final balancing work, which is also performed on a system developed by EMAG. The flexible system is fully capable of adding another station, such as a measuring station, before the finished part is stacked on its pallet. Also, the VL 8 machines from EMAG can be optionally equipped with measuring probes that can carry out pre- and post-process measurements. This is why a measuring station was not included here.
Optimum turning machine for truck brake drums
The VL 8, which is used for the machining work, is based on EMAG's successful VL series. With a chuck diameter of 500 millimeters, the pick-up spindle picks up workpieces with diameters as large as 400 millimeters. For machining, the directly driven main spindle provides 60 kW drive power and up to 1220 Nm torque. This gives it enough cutting power to make fast work of the brake drums. The machine's base is made from Mineralit polymer concrete. It guarantees low-vibration processes, ensuring long tool lifetimes and very high machining quality. Like every machine in the VL series, the VL 8 features the special EMAG tool turret with direct drive, which can be equipped with 12 turning tools or 12 driven drilling and milling tools. Linear scales on all linear axes ensure the greatest possible long-term accuracy on the workpieces and high process reliability.
IoT-ready
Starting in 2021, the VL series machines used will be supplied IoT-ready. That means that every machine comes with a preinstalled industrial PC. This allows the customer to move into data-driven manufacturing at any time without difficulty. To some, that may still seem a long way off, but EMAG is certain that requirements in this area are going to rise quickly in the coming years. Demand has been growing since the beginning of the year.
With this manufacturing solution, EMAG shows that simplicity, productivity, and flexibility do not have to be mutually exclusive. Combined with its expertise in data analysis, this machine maker is positioning itself as a powerful partner for the industry, which is facing great challenges in the conversion to electric propulsion. EMAG is ready to tackle those challenges.
Images
Contact
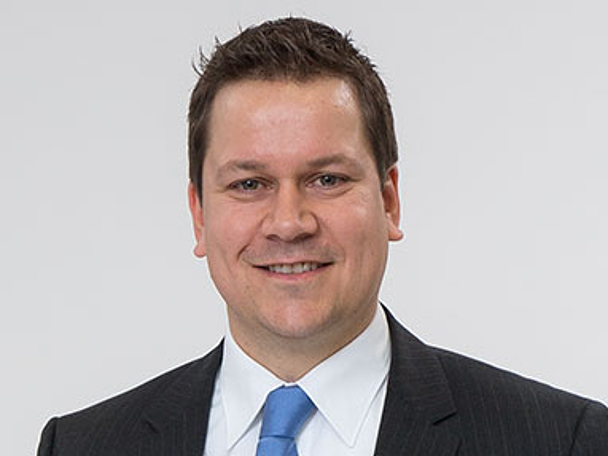
Oliver Hagenlocher
Area
Press and Communication