10/25/2021 - Oliver Hagenlocher - Press
Vertical Turning Center from EMAG Scherer: Machining Large Quantities of Stator Housings with Speed and Precision
Electric cars still account for a relatively small proportion of total car sales, and a trend toward rapid growth for electric car production is still a long way off. But there are exceptions, as demonstrated using EMAG Scherer’s technology at a supplier in Central America. A total of 12 CNC vertical turning centers of type VDZ 520 XL ensure that up to 3,000 stator housings, used solely in electric car motors, are machined every day. This solution is extremely accurate and reliable. Which performance features of the machines stand out?
Images
Electric mobility is currently in a transitional phase, at least according to analysts from BloombergNEF. They maintain that the number of electric cars sold rose to 2.5 million worldwide in 2020, which corresponds to a growth rate of 20 percent – although this number was higher in recent years. Even so, the “hot spot” is changing. Although in recent times China has driven the development, the role of the European market is now becoming more important. Quantities are rising more quickly here than in the rest of the world. For this reason, BloombergNEF is predicting a bright future for this technology.
EMAG Scherer ‘s experience in electric car manufacturing
Mechanical engineering is playing a major role in this development. It developed the production technology to enable reliable and precise manufacturing of key components of the electric drive – in much larger quantities than before. For EMAG Scherer changing trends are not a long way off. At its headquarters in Alzenau, near Hanau, already has earned experience in production of a key electric motor component: the complex and at the same time very thin-walled stator housing. As early as in 2018, the specialists developed a highly efficient solution for cutting machining based on the CNC vertical turning center VDZ 520 XL on behalf of a Central American supplier. Eight processes take place on the stator housing in only 240 seconds of chip-to-chip time. Ultimately about 320 components can be produced per machine and day, although the customer ordered six machines to produce higher quantities. In the meantime, twelve machines are being used, which clearly shows that this solution is meeting expectations in every respect.
Experts for sophisticated components
But how did this assignment come about in a field of work that represents uncharted territory for many machine manufacturers? “The customer contacted us at a trade fair,” explains Alexander Ott, sales manager at EMAG Scherer. “It certainly played a role that we have been making a name for ourselves for many years with efficient machining solutions for sophisticated components. From the very beginning it was clear that this was a special task regarding the component geometry and demanded tolerances.” The technical data of the stator housing confirmed this assessment. For example, the finished component has a wall thickness of merely four millimeters – with tolerances of only 0.016 to 0.25 millimeters and very precise roundness. At the same time, there are many bore holes and grooves, and the geometry is not rotationally symmetric.
The specialists subsequently adapted the production processes perfectly to meet these conditions. In the VDZ 520 XL, eight cutting processes take place in succession on the injection-cast blank – from the highly precise roughing and finishing of internal surfaces, external connecting surfaces and sintered bushes up to the milling of grooves and drilling or milling of various cross and oblong holes. A special role is played by the customized clamping solution from SAV, in which the sensitive component is aligned and centered with high precision. Furthermore, the entire design of the machine is advantageous. Its vertical machining ensures optimal chip flow despite the closed stator housing. Its synchronous drive technology with 64.4 kW power and 1,110 Nm nominal torque ensures reliable, quick machining processes, and the stable cast machine bed guarantees good damping behavior.
Machining time decreasing further
Furthermore, the entire production process is extremely uncomplicated. The operator places the blanks on the corresponding revolving conveyor and takes them off once they are fully machined. The conveyor serves as an integrated part storage device, which means the machine can operate for a time without supervision, while a highly efficient process takes place inside. A pick-up spindle picks the components off the drag frame and feeds them at high speed to the machining area with integrated 12-station tool turret. Short distances ensure minimum chip-to-chip times. The specialists from EMAG Scherer are currently working on further optimization. For example, a multi-cutter will be used in future in the tool turret to decrease the machining time by a further 30 seconds.
Two operations on the stator housing in a single machine
Overall, EMAG Scherer is adapting these and similar mechanical engineering solutions very precisely to the tasks of the customers, and even complex processes do not pose any problems. For example, the specialists have designed a VDZ 420 XL DS with two spindles for a Chinese customer, in which two different operations take place in succession on the stator housing: roughing and finishing of the external geometry (OP 10) and roughing and finishing of the internal surface and connecting surface including a few drilling and milling processes (OP 20). The solution includes an NC rotary axis between the two machining areas. It is used to unload the workpieces between OP 10 and OP 20 with the correct orientation and transfer them. The cycle time for the component is only 130 seconds, with both operations running simultaneously on two components. Undesired idle times are reduced to a minimum.
In this context, EMAG Scherer is ideally prepared for the “electric car boom,” according to Alexander Ott. “We benefit from our experience, because the quality of such production processes on a complex component is always determined in the early phase of the design. This is when we apply our complete knowledge – to the various tool applications, the design of multi-functional tool machines and their control and interlinking. We show the customer any problems in a transparent manner and illustrate how we intend to solve these problems during the quotation phase. The main objective is always to produce optimum components – in the cycle time and quality requested by the customer. This applies, of course, also to every electric motor component.”
Downloads
Contact
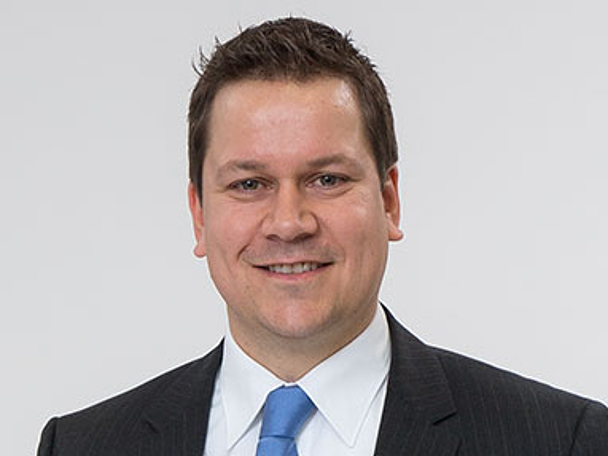
Oliver Hagenlocher
Area
Press and Communication