02/06/2019 - Oliver Hagenlocher - Press
EMAG Automation becomes EMAG LaserTec: Driving laser welding and joining technology with a new name
EMAG laser welding technology has been an impressive success story for years: The system ensures efficient light construction and lower component costs in the manufacture of numerous vehicle components. The relevant turnkey production systems are made at EMAG’s site in Heubach near Schwäbisch Gmünd – under a new name: As of January, the technology company that used to be known as “EMAG Automation” is called “EMAG LaserTec.” The new name better fits the new focus and strategic orientation of the company, since the specialists are seeing excellent market opportunities for its end-to-end laser production solutions. Which applications and technologies will be driving the development of the new EMAG LaserTec in the future?
Images
Modern drive trains are becoming an increasingly complex challenge for developers and production planners: In established systems like the automatic torque converter and dual-clutch transmissions, the number of speeds is increasing. At the same time, hybrid drives and assistance systems are entering the scene. In combination, this first creates additional components and therefore extra weight, which needs to be reduced as far as possible. This is why laser welding has become indispensable in modern transmission construction: Components can be joined perfectly, without the heavy and expensive threaded connections used in the past. In addition, the process enables the production of weight-optimized clutch components, for example, by combining a forged and then machined hub with a formed sheet metal part. “This basically explains the success of our technology,” says Dr. Andreas Mootz, Managing Director at EMAG LaserTec. “Our process offers great new opportunities for lightweight design and reducing the cost of components. However, it always needs to be integrated in holistic solutions. This is why we take responsibility for the entire process technology, from machining through the laser welding process itself, up to thermal joining and high-precision ultrasonic inspection processes. This know-how is what makes us unique in the market.”
New market opportunities – increasing technological know-how
More than 160 of these laser welding systems have been developed and delivered by the specialists in Heubach – every single one of them customized for the specific application. All leading automotive companies are using the systems with the ELC tag (EMAG Laser Cell) to manufacture shift gears differentials, clutch components, engine and steering components, and many other products. These “Customized Solutions” have been the main driver of company revenues for a long time. It is only natural for EMAG LaserTec to sharpen its focus on this field of application with the new name. In addition, the technological development is more or less converging on laser technology. The increased market share of hybrid drives for example increases the number of clutches that require components joined by laser welding. What’s more: The specialists are continuously expanding their laser process and application know-how. For example, they have already designed machines with laser cleaning processes. The process uses high-performance lasers to effectively remove residues like cooling lubricants or preservatives before welding. This procedure is quicker than conventional washing, and it is easier to integrate into the process. Another interesting field is laser hardening, which enables partial hardening of edge layers with minimum warp.
Joining technology remains key
EMAG LaserTec continues to stand out for its patented pre-heating and joining technology that is used in the production of transmission shafts or “built” camshafts and transmission shafts: Inside the EMAG machine, cams are heated precisely through induction and subsequently joined to the shaft without application of force. This process enables the realization of cam shafts with demanding geometric details. Components can also be made much lighter by replacing a heavy cast shaft with a hollow pipe. In addition, forged cams can be used that do not require grinding after joining. Less important parts like plugs or end pieces can be made of cheaper materials to reduce cost. “We have a lot of experience with regard to the sensitive production workflow of heating, joining, and holding. This allows us to configure the entire equipment perfectly for the specific production environment. This application remains extremely important for us,” Mootz confirms.
Exploring new fields of application
EMAG LaserTec intends to continue its growth over the coming years. Prospects are good, since the demands of OEMs for lower component costs and effective lightweight design continue to create new applications for laser and joining technology. This can be seen in a number of examples, including some from outside the production of passenger cars. For example, the engineers in Heubach are currently designing the first ELC machine for a truck differential with workpiece weights of more than 100 kilograms. Other interesting fields include laser welding systems used in the production of rotor shafts or differentials for electric motors. “Again and again, customers benefit from our process-specific know-how and our development method,” Mootz explains. “Our approach starts with the workpiece as the basis for developing the overall production solution. This is done based on modular EMAG engineering, which includes numerous proven components. The end results are exceptionally stable and cost-effective processes for laser welding and joining. Under the new name, we will redouble our efforts to carry these strengths into the market.”
Contact
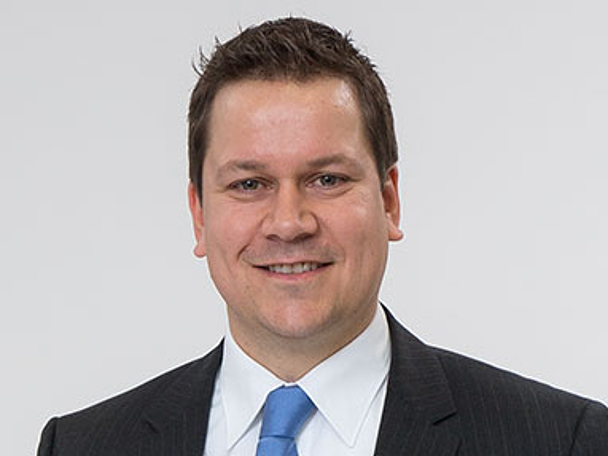
Oliver Hagenlocher
Area
Press and Communication