07/22/2021 - Oliver Hagenlocher - Press
Analysis of high-frequency data for anomaly detection: New method enables evaluation during operation – “in-process anomaly detection” in manufacturing
At many supplier companies, the production conditions are subject to constant change: On the one hand, automotive components are getting increasingly complex. On the other, the OEM requirements for dimensional accuracy and tolerances are growing fast. And the error tolerance is “zero.” How can these trends be reconciled? A current Industry 4.0 solution from EMAG provides the answer. The machine manufacturer uses special functions of the machine controller to continuously collect in-process measuring values, which are then directly analyzed with the “EDNA” modular IoT system to detect anomalies. What possibilities does this innovative Industry 4.0 approach offer?
Images
When it comes to the details, industrial production is a fight for each micrometer and millisecond, with each process being optimized continuously. Anomalies need to be detected without delay – during the manufacturing process – to enable immediate corrective measures.
IoT Core analyzes measuring data
Independent of its mechanical engineering work, EMAG is systematically digitizing its production technology. The large amount of sensor, operating and production data generated by each machine tool during its operation is used extensively to further improve the stability and productivity of the processes. The recorded data are compared with target values to reliably detect process anomalies. The basis for this endeavor is the new comprehensive IoT solution EDNA, which is used to network, control and analyze the machines. At the heart of this system lies a powerful industrial PC – the aptly named EDNA IoT Core – which records, aggregates and analyzes the data. It is possible to flexibly adapt the scale on which the EDNA IoT Core is used: only locally within a standalone machine, connected to an edge solution (i.e., a company-wide internal network or cloud) or networked with the cloud. Simultaneously, the solution has a completely modular software architecture – if needed, additional protocols, data connections to customer systems, various analysis scripts (evaluations) etc. can be implemented.
Reacting as early as possible
Based on the recorded and analyzed data, EMAG’s specialists can detect sporadic anomalies in monitored parameters at a very early stage. The EDNA IoT Core records a potential non-conformance at the moment it occurs and analyzes the data within a few seconds. Taking into account which processing step is involved, it then decides whether it is necessary to stop the entire production process and reject the component. “For intelligent anomaly detection, a learning process is of course necessary at the beginning. Not every non-conformance in the production process inevitably results in a rejected part. For example, if a non-conformance occurs during the roughing step, but is compensated during finishing, this non-conformance has no effect on the quality of the component,” explains Rainer Seitz, head of Software Development & IoT at EMAG. For the user, the reverse also holds true: If an anomaly occurs and cannot be compensated, the component will not be (superfluously) processed to completion. Thus no further value-adding work is applied to a component that is defective anyway – a cost benefit not to be underestimated when large quantities are produced. But this is not the only potential cost saving. In components with high quality requirements, the anomaly detection can help reduce the number of parts that need to be measured, which reduces costs. “It is also possible to detect initial signs of wear on machine components, as a first example from practice has now shown. That means that this form of anomaly detection can potentially supplement our EDNA Health Check, with which it is already possible to monitor the operating condition of important machine components,” says Seitz.
A world of possibilities
What opportunities will this approach offer in the future – also considering other customers? The answer is manifold. The EDNA IoT Core provides access to a large amount of data that makes it possible to draw conclusions regarding the condition of the machine. Based on an analysis of the target and actual values, classification is possible: If a non-conformance occurs, the user is given early warning and can steer the process as necessary (e.g., rejecting the component). Furthermore, the entire solution can be connected to EMAG via the cloud, which makes it possible for the machine manufacturer to provide support with controlling and error analysis. As a result, the entire production process becomes significantly more transparent and efficient, as diverse other implementations of EDNA at customers with other use cases have impressively shown. The experts at EMAG estimate that, in general, a return on investment is possible after around a year, if all data are evaluated and used to derive actions. “With EDNA, we have definitely created a completely new tool specifically for increasing the productivity of our customers – without requiring investment in new machines, because the solution also works on many older models,” says Rainer Seitz. “Simultaneously, we are laying the foundation for the intelligent production of the future at our customers’ factories.”
Interview with Andreas Kühne, lead data scientist at anacision
Predictive maintenance, increasing output quantities and decreasing error rates – the performance promises of Industry 4.0 are great, although many users still doubt their feasibility: “It’s all a long way off,” as we often hear. At this point, we want to take a very practical look at this topic: At a major German automotive components supplier, IoT experts from EMAG, and their partner companies EXXETA, intuity, and anacision, have optimized a central production process – with amazing results, such as a significant increase in the production capacity of the EMAG line. A conversation with Andreas Kühne, lead data scientist at anacision, about the current successes of the associated EMAG EDNA technology, and how machine builders are comprehensively digitizing their machines.
Contact
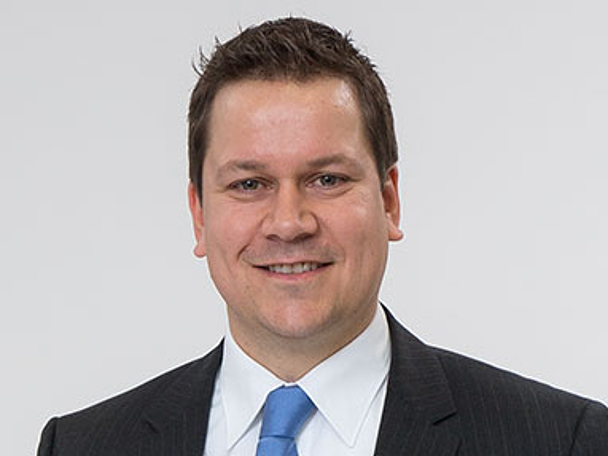
Oliver Hagenlocher
Area
Press and Communication