EMAG Zerbst Maschinenfabrik: Status of CO2 reduction
In order to fully capture the CO2 footprint of companies, the Greenhouse Gas Protocol (GHGP) standard was introduced, which divides emissions into three "scopes". Scope 1 refers to direct emissions caused by the company itself, e.g. by burning fossil fuels in heating systems or vehicles. Scope 2, on the other hand, refers to indirect emissions caused by the use of external electricity, heating or cooling. Scope 3 of the GHGP refers to indirect emissions that occur outside a company's direct control and production. These include emissions from the value chain such as the production of purchased materials, transport-related emissions, product use by the end user, and product disposal.
- Scope 1: Direct GHG emissions
- Scope 2: Indirect GHG emissions
- Scope 3: Upstream and downstream GHG emissions
With regard to Scope 1, EMAG Zerbst Maschinenfabrik has made significant efforts to reduce its direct carbon footprint. This was achieved through a combination of energy efficiency measures and the integration of renewable energies.
Since 2013, investments have been made in energy-saving technologies, parts of the heating infrastructure have been modernized, and continuous temperature monitoring of the production facilities has been introduced.
A detailed description of the measures implemented can be found at:
In terms of indirect CO2 emissions from Scope 2, EMAG Zerbst Maschinenfabrik has made significant progress in reducing external electricity consumption. This was achieved through a combination of investments in more efficient technologies and equipment and the use of renewable energy sources.
The installation of photovoltaic (PV) systems makes a significant contribution to this.
In the case of EMAG Zerbst Maschinenfabrik, Scope 3 is challenging because it involves a number of complex and often external factors that are difficult to control and quantify.
For example, a key factor in Scope 3 is the emissions generated in the production and supply of materials and services that EMAG Zerbst procures from its suppliers. It requires deep engagement and collaboration with external partners, suppliers and customers, as well as strategic planning and implementation to make significant progress. However, through the environmental certification of its suppliers, the EMAG Group has taken an important step towards CO2 neutrality in Scope 3.
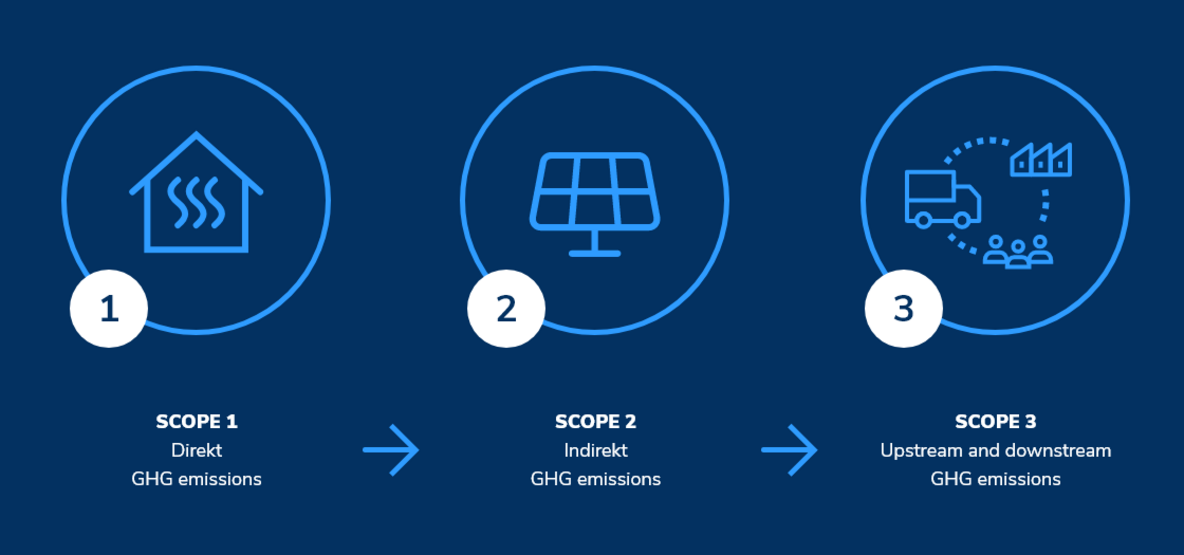
Details on CO2 reduction
EMAG Zerbst Maschinenfabrik has been DIN ISO 50001 certified since 2013 and has since embarked on an ambitious path to CO2 reduction. Sophisticated energy monitoring and a series of innovative measures have enabled the company to significantly reduce its energy consumption and establish a more environmentally friendly production method.
Reduction of power consumption
The company's electricity consumption has been almost halved since 2013.
The following projects contributed significantly to this:
- Replacement investments with focus on power consumption
- Improvement of compressor controls and acquisition of new compressors
- Renewal of the cooling system for machine cooling
- Reduction of the compressed air pressure
- Conversion of all light sources to LED
- Creation of shutdown rules for weekends and public holidays and raising employee awareness
- successive replacement of obsolete technology, e.g. welding equipment
- automatic switching off of hall lighting at break times
Reduction of gas consumption
At EMAG Zerbst Maschinenfabrik, only a very small amount of gas is used for process operations. The majority is used to heat the production areas in the winter months. In addition, a switch to bio-methane gas was made for the year 2023.
A reduction in gas consumption was achieved through the following measures:
- Renewal of the heating system
- Establishment of continuous temperature monitoring and lowering of the hall temperature to 19-20 °C during the heating period.
- Successive conversion of propane gas forklifts to electric forklifts
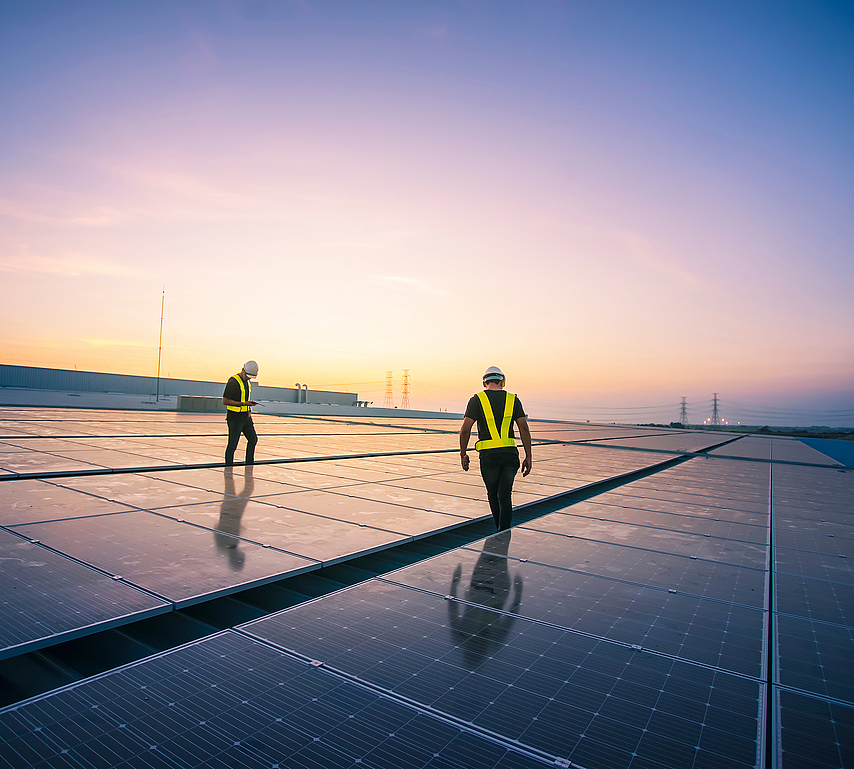
Use of photovoltaics
The installation of photovoltaic systems with a capacity of 2.6 MWp has greatly reduced external electricity purchases.
Around 30 % of the electricity required is generated on site by the photovoltaic systems. The electricity not consumed by the company itself is fed into the grid.